Это вам не 3D-принтер гонять, тут все по-взрослому. Покажем производство корпусов по очень популярной технологии литья полиуретана в силиконовые формы — как это делается; и расскажем о рисках и ошибках. Зачем? Чтобы цена разработки и производства корпуса неожиданно не стала в несколько раз выше, чем вы планировали.
Когда мы говорим нашим заказчикам, что скоро доберемся до серийного производства корпусов, они иногда пугаются. Страх — это неизвестность, поэтому мы расскажем (и покажем), как делают корпуса по относительно недорогой и распространенной технологии литья в силиконовые формы. На настоящей фабрике, все как у больших. После этого вы скажете, что видели в этой жизни уже все, а бояться будет больше нечего.
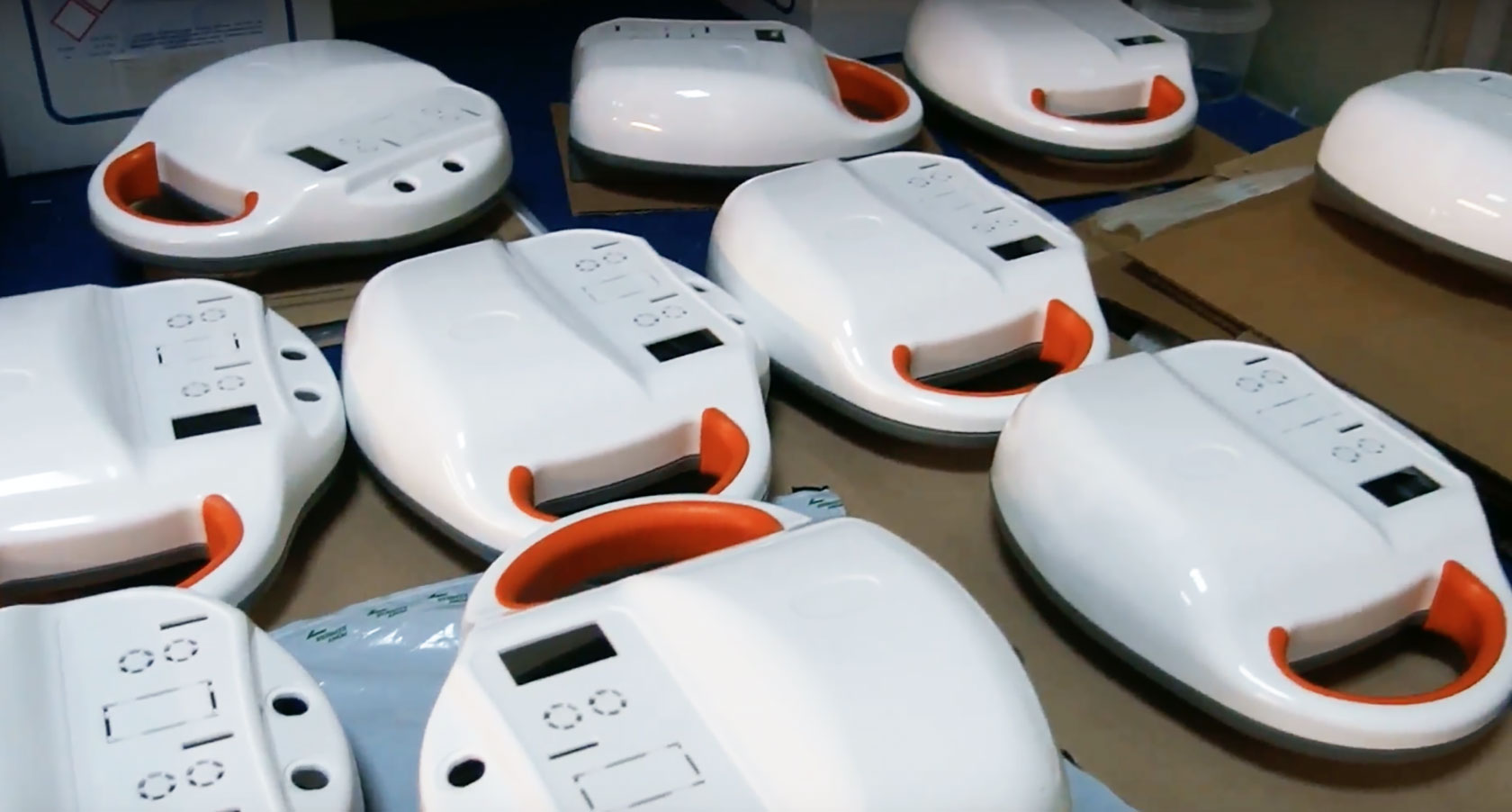
Полиуретан — это так же, как и остальные пластики, полимер, но со специфическими свойствами. Он обладает высокой ударопрочностью, хорошими механическими свойствами, высокой твёрдостью и годится для литья толстостенных изделий. Разработка корпусов под технологию литья полиуретана в силикон, пожалуй, самый распространенный тип проектов. По крайней мере, у нас.
Два случая, когда литье в силикон выгодно
Производство корпусов методом литья полиуретана в силиконовые формы, оно же литье в силикон, оправдывает себя только в паре случаев:
а) когда ты выпускаешь единицы (иногда — десятки) изделий для тестирования. Ты еще не знаешь, как к твоему продукту отнесутся пользователи, как они будут с ним взаимодействовать и, таким образом, обходишься без капитальных затрат, пока продукт не будет проверен на деле;
б) если у тебя дорогое изделие, которое будет меняться со временем. Например, через год ты изменишь начинку, потому что сейчас продукт полностью не сформулирован. Планируется, что он будет дорабатываться исходя из запросов пользователей. У нас есть такой в работе — корпус дозиметра, его постоянно совершенствуют. Здесь вкладываться в пресс-формы надо очень аккуратно и хорошо считать экономику.
Поэтому в большинстве таких случаев литье в силикон — единственная приемлемая технология для производства корпусов.
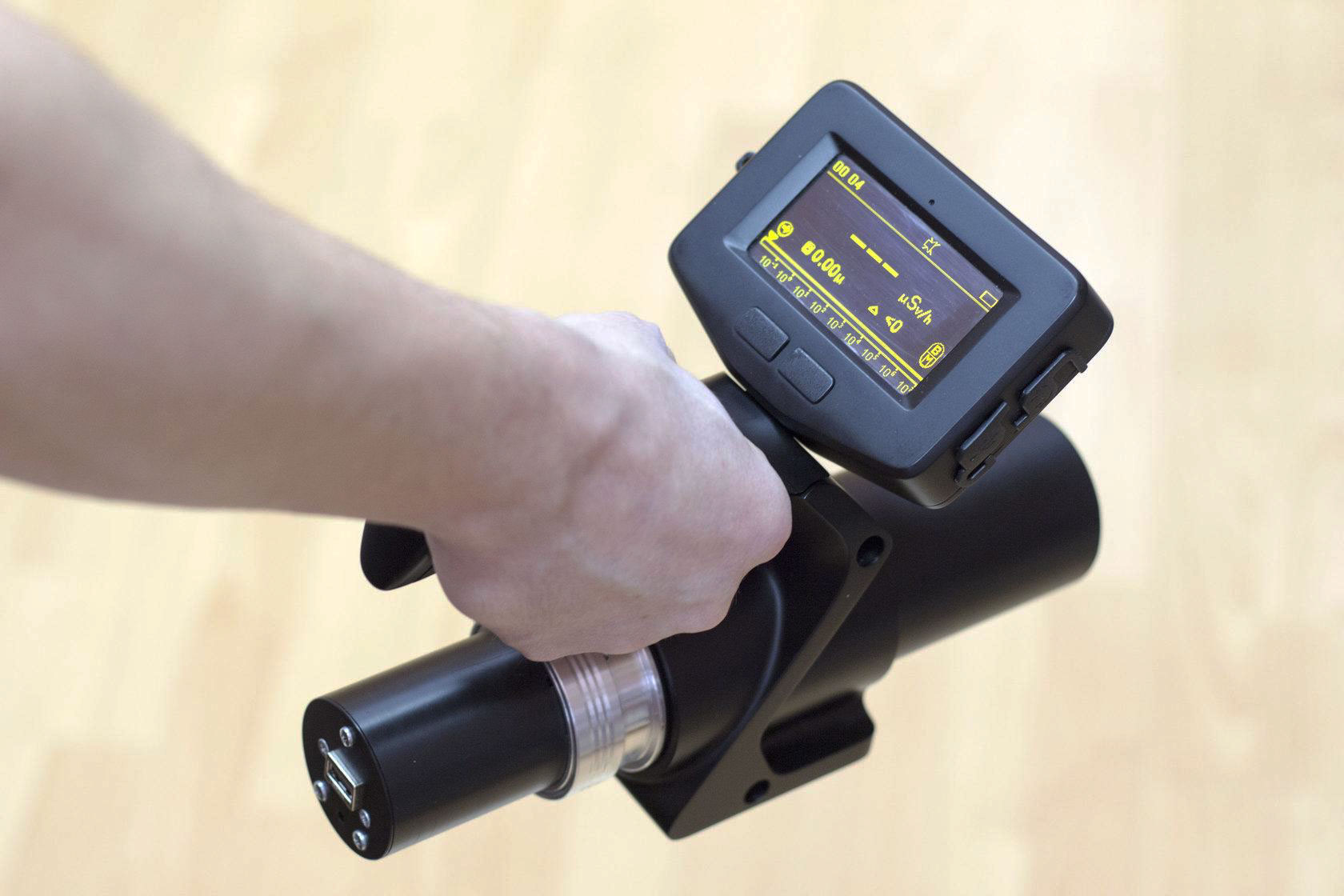
Во всех остальных случаях литье полиуретана себя не оправдывает:
-
корпуса получаются дорогими;
-
цена с увеличением тиража не падает;
-
низкая скорость производства (сегодня нельзя заказать 25 штук, а завтра — 200, придется ждать);
-
очень много ручного труда;
-
чем больше тираж, тем больше брака;
-
и за все это платишь ты, а не кто-то посторонний.
Производство корпусов литьем в силикон: этапы
1. Фабрика получает вашу КД и проверяет её
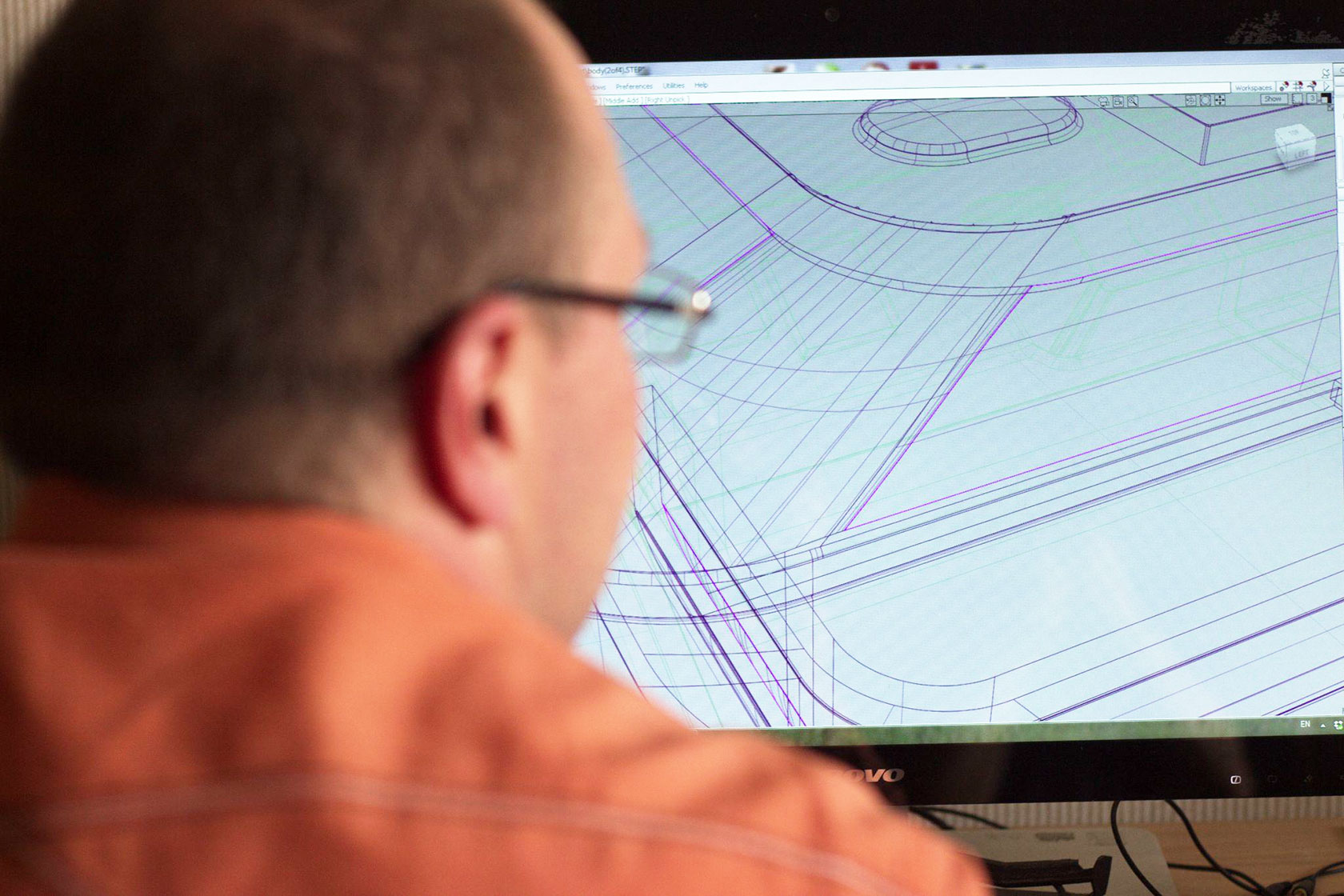
На производстве убеждаются, что размеры корпуса на чертежах соответствуют его макету в реальности.
2. Печатается макет, его проверяют на собираемость
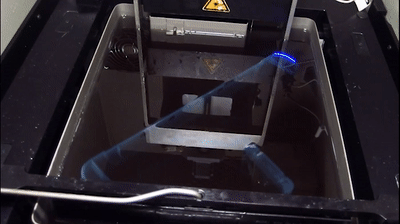
По большому счету, фабрике по барабану на детали: например, собирается корпус или нет, — это проблема клиента. Но большинство все же проверяет, что может — сборку, гибкость, зазоры и так далее.
3. Делается мастер-модель
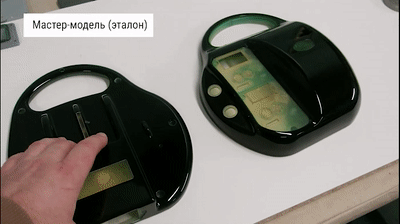
На заметку: мастер-модель «живет» 6 месяцев, не больше. А потом может, например, набрать влаги из воздуха и деформироваться.
4. По мастер-модели изготавливается силиконовая оснастка
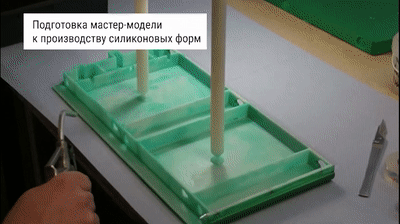
Последняя при правильном проектировании выдерживает до 25 идентичных друг другу отливок. Затем силиконовая форма изменяет геометрию из-за многократных циклов открывания-закрывания, и это не лучшим образом сказывается на конечном продукте.
Важно: про проектирование деталей
На этом этапе имеет огромное значение, правильно ли спроектирована деталь. От этого зависит, как она будет выниматься из формы, как будет проливаться материал, появятся ли дефекты после усадки (так называемые утяжины).
Правильное проектирование — это когда деталь спроектирована конусообразно/имеет уклоны. Но есть случаи, когда в проекте это игнорируют. Тогда засада: прямая деталь свободно выскользнуть из формы не в состоянии, значит, она будет разрывать силиконовую оснастку. Это — попадалово на деньги: с одной формы ты получишь не 25 корпусов, а 3, потому что оснастку придется постоянно менять.
Или когда литьем в силикон хотя сделать корпус с защелками. В силиконе нет подвижных знаков, как в стальных формах. При таких условиях защелки, по сути, «выдираются» из формы. Изготавливать изделие с защелками по этой технологии нельзя.
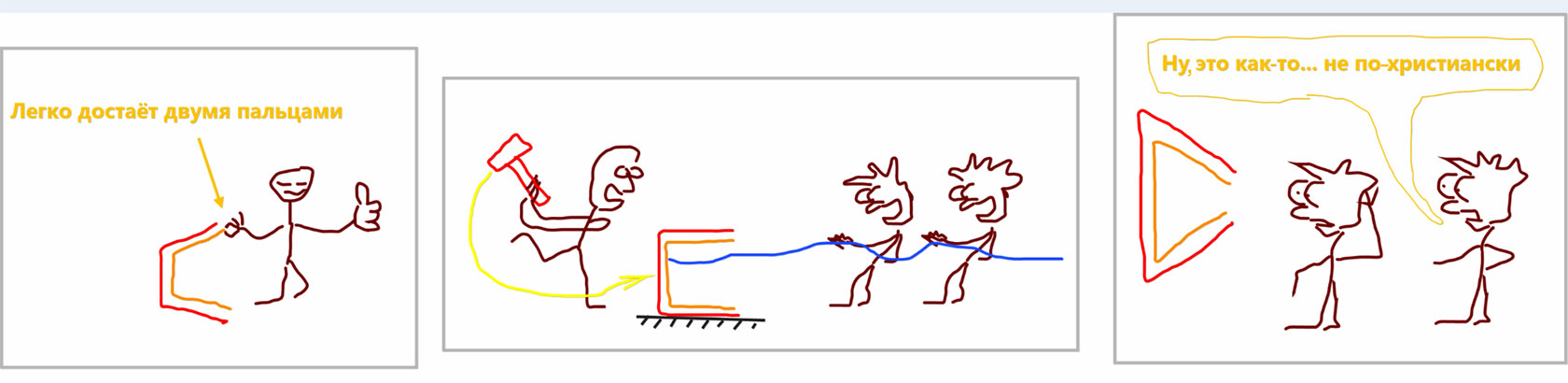
Конструкторские косяки в разработке корпусов — очень частая ошибка. Люди проектируют деталь, не понимая логики процесса. У нас в блоге уже несколько лет висит годная переводная статья про проектирование корпусов из пластмассы (https://formlab.ru/kak_razrabotat_korpus_iz_plastika/), но люди игнорят все правила и проектируют
жопойкриво.
Так что для литья в силикон проектируйте деталь с учетом того, как и под каким углом она будет выниматься. Вытаскивать ее просто, от балды, нельзя («Авось покорячатся и вытащат»), нужно иметь опыт.
Более того: изделие, как правило, проектируется под определенную технологию производства. Это значит, что для литья под давлением КД на деталь, спроектированную под литье в силикон, подойдет далеко не всегда. Еще точнее — практически никогда (исключение: случай, когда вы заранее ставите конструктору задачу сделать универсальную КД, рассчитанную на две технологии производства).
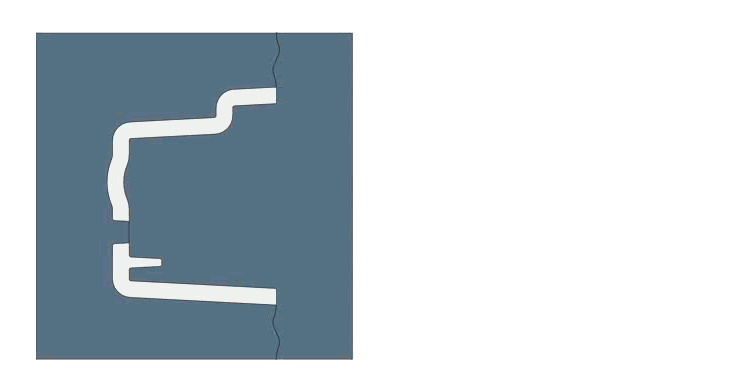
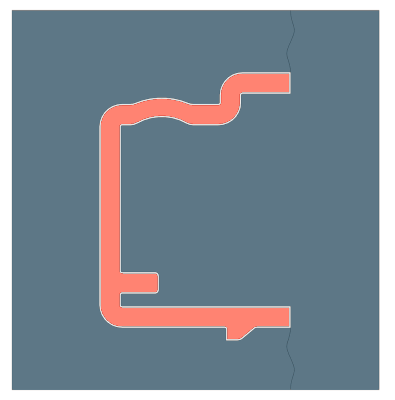
5. Силикон заливается в оснастку
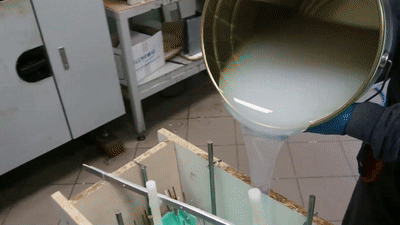
Внимание: материалы здесь используются преимущественно импортные, поэтому их стоимость зависит от курса валют.
6. В камере дегазации удаляются пузырьки воздуха
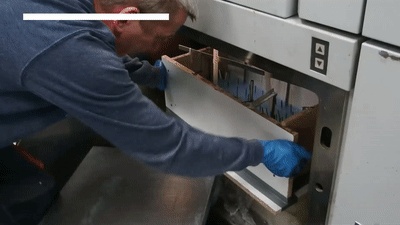
Пузырьки воздуха, в народе — «баблы» (bubble), всегда есть на отливках из полиуретана. Особенно там, где у материала большая толщина. «Правильный подрядчик» знает об этом и размещает деталь в оснастке так, чтобы эффект от «баблов» не выходил на наружные видовые поверхности.
7. На производстве разделяют силиконовую форму на части
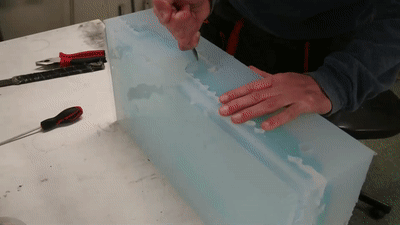
На картинке видно, что форму разрезают волнообразно. Это делается для того, чтобы позиционирование половин было точнее: при разрезе по прямой у тебя всегда появится смещение. А тут половины точно сопрягутся, перепутать точки соприкосновения нельзя.
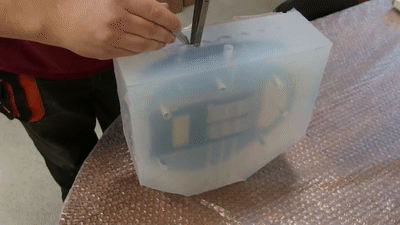
8. Заливается полиуретан
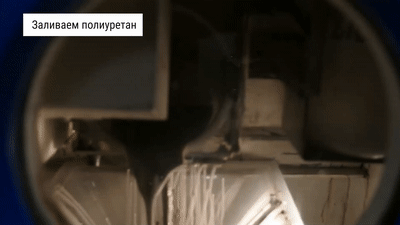
Возможные косяки на этом этапе: в полиуретан может попасть мусор (зависит от аккуратности производства); неравномерно распределен колер; забыли добавить УФ-стойкую добавку.
9. Излишки полиуретана удаляются
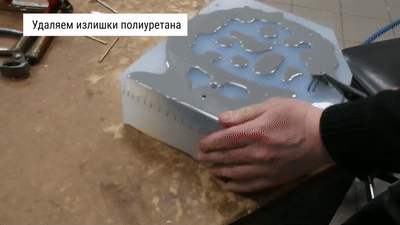
Вместе с излишками материала сразу удаляются литники (полиуретан, который остаётся в том месте, где материал заливался в форму).
10. Силиконовая форма раскрывается
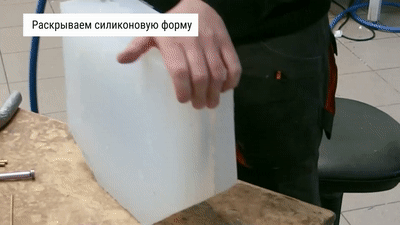
Риск: в случае несоблюдения технологии производства форма может не раскрыться.
11. Обработка
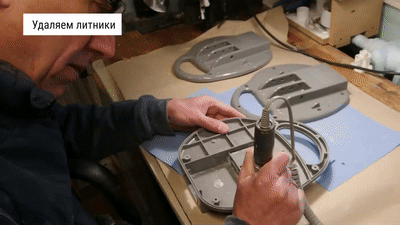
Обрабатываются места, где были литники (сами литники уже удалили вместе с излишками).
12. Готовая продукция
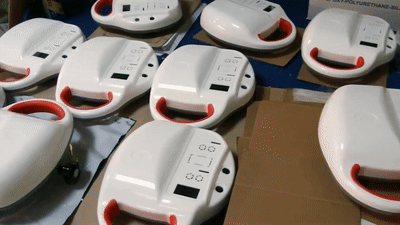
Вот и все, корпус изготовлен.
Ограничения при литье в силиконовые формы
Красятся детали, изготовленные литьем в силикон, очень условно: то есть покрасить можно, но краска может протираться на углах. Но при качественных материалах и хорошей работе может и не протираться.
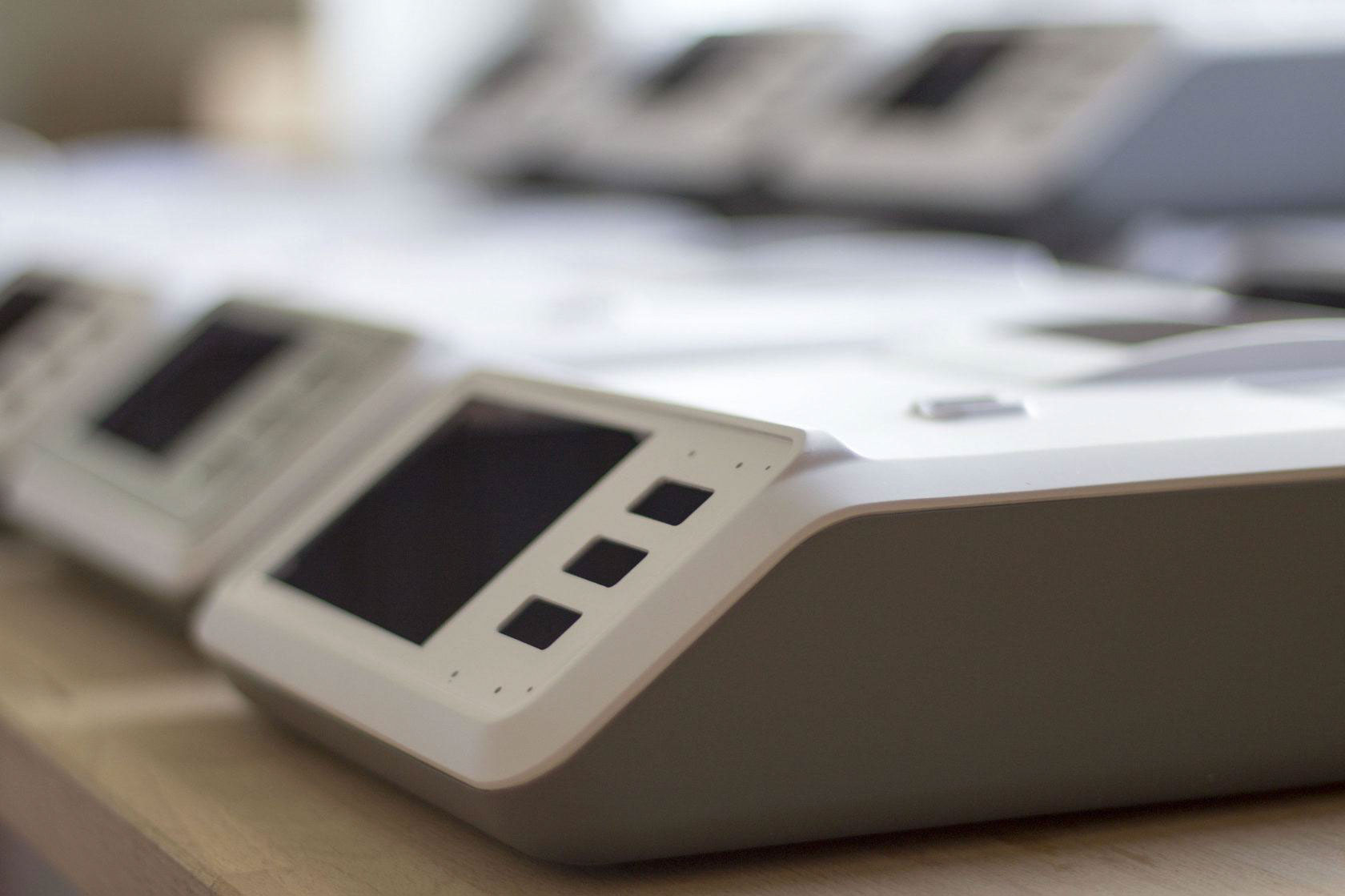
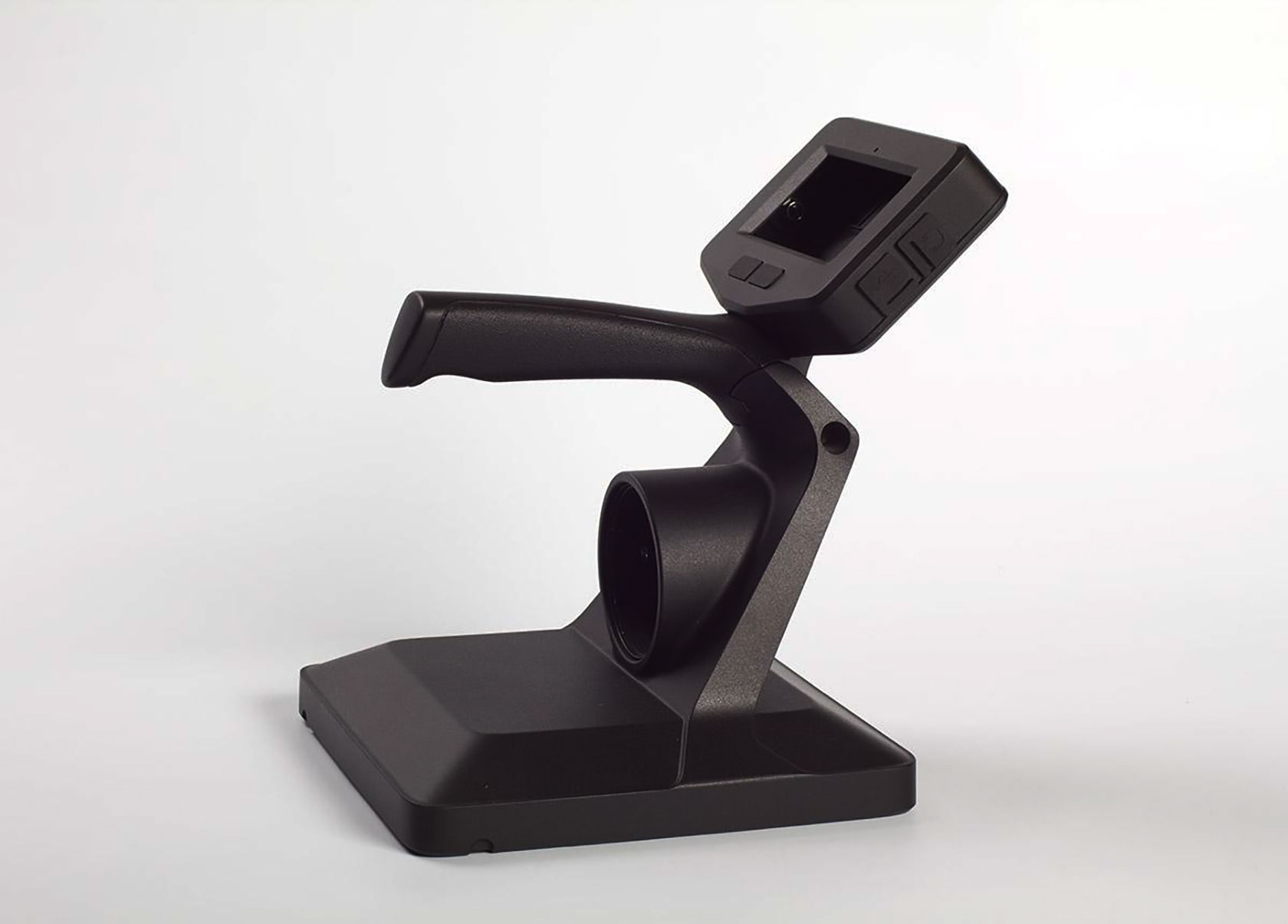
Но: если у тебя прибор активно взаимодействует с человеком (или люди его одеждой могут задевать, например), то красить его нежелательно.
Однако ты можешь красить в массе: в полиуретан подмешают краситель, и корпус будет нужного оттенка.
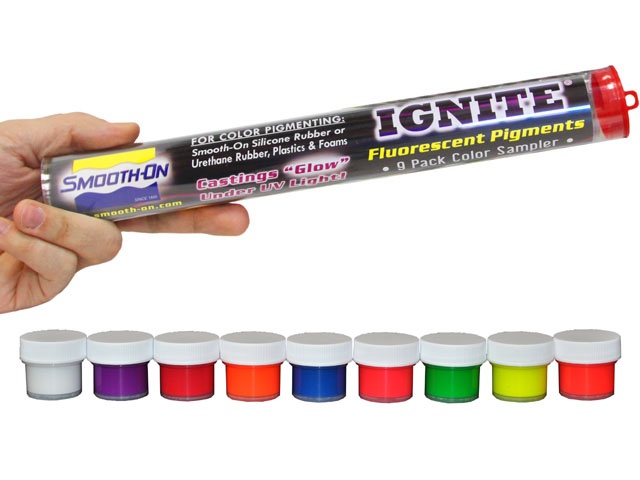
Существуют и другие добавки — например, для защиты от УФ-излучения, чтобы корпус не выгорал на солнце.
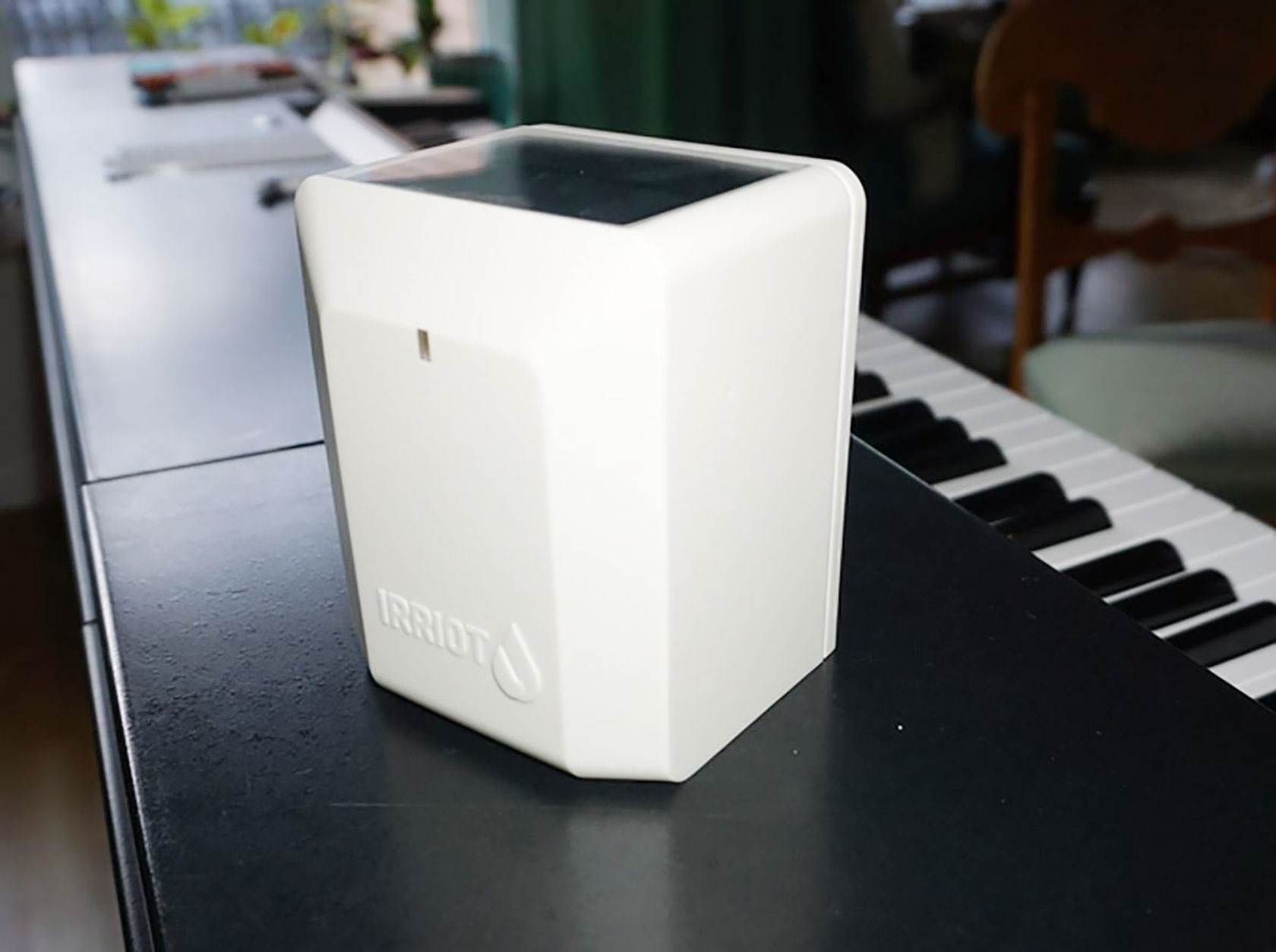
Ты можешь также — условно — управлять шагренью.
Но в целом возможности, которые дают серийные технологии, здесь ограничены. Естественно, никакого Soft Touch — ты не можешь нанести на корпус такое покрытие. Никакого двукомпонентного литья; только клеевое соединение.
Кроме того, при литье в силикон сложно добиться качественного глянца.
Размеры корпуса: есть некоторые ограничения по габаритам. Максимально доступные размеры корпуса у наших подрядчиков, например, 1500х750х500 мм.
Итого
Теперь вы прекрасно знаете, что происходит на каждом этапе производства корпусов по технологии литья в силиконовые формы. Полностью видео есть на нашем канале на Youtube. Cнимали на производстве одного из партнеров. Если что-то (скорее, нет, чем да, но вдруг) упустили, поправьте в комментариях.
На заметку: когда будете искать подрядчика на производство корпусов, между делом попроситесь на экскурсию по производству. Хороший точно не откажет. Начинает мяться и искать отговорки — смело шлите лесом.
Да что тут говорить, о том, как мы фильтруем подрядчиков на производство и сколько по-настоящему хороших фабрик сумели обнаружить за 10+ лет поисков, читайте в одной из следующих статей. Сдадим всех.
Об этом и о другом в сфере производства и разработки корпусов стали писать в новомодные телеги, велкам, присоединяйтесь.
За материалы спасибо компании МСП.
Автор: Андрей Востриков