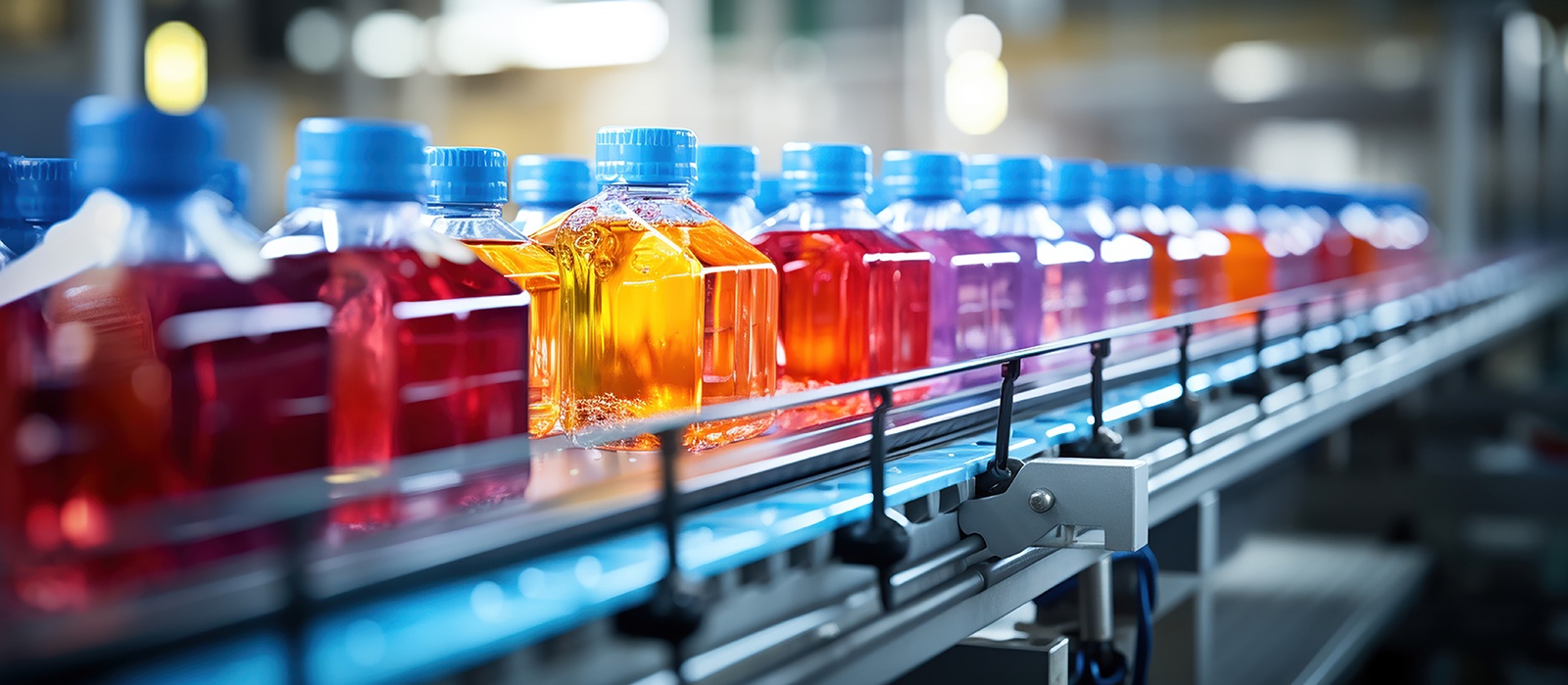
Картинка Maniacvector, Freepik
В жизни нас со всех сторон окружает интересная субстанция, которую в обиходе называют «пластиком», представляющую собой составы разного типа.
Пластики распространились по той причине, что им удобно придавать требуемую форму, в том числе с большой скоростью, что весьма важно в условиях современного серийного производства.
Кроме того, различные их типы устойчивы к разным вариантам агрессивных сред, что весьма важно для создания разнообразных компонентов устройств, которые могут выполнять полезные функции в условиях такой среды (например, полиэтилен для бутылок ацетона, который не разрушается им).
Но мне тут стало интересно, а насколько реально самому создать пластик?
Потому что обычно он у нас ассоциируется с «высокими материями» из области органической химии, далёкими от «простого смертного».
Тем не менее, как оказалось, это более чем реально и, мало того, весьма просто! Об этом и будет весь следующий рассказ...
▍ Пластик из молока
Да-да, именно так, из обычного молока можно создать пластик!
Дело в том, что в обычном молоке содержится большое количество белка, называемого «казеиногеном», доля которого может доходить вплоть до 85% от объёма.
Этот белок можно выделить из молока, для чего необходимо, чтобы оно свернулось. В этих целях в нагретое до 48-50 °C молоко добавляют несколько ложек обычного столового уксуса, при постоянном помешивании.
При этом, насколько удалось выяснить, происходит следующий процесс: содержащийся в молоке казеин освобождается от кальция, а относительно высокая температура приводит к выпадению его в осадок.
Строго говоря, выпавший остаток не является чистым казеином, а содержит ещё жиры и другие компоненты.
Такой процесс как раз и показан в видео ниже:
Далее необходимо из него отжать влагу, просушить, и в полностью сухом состоянии казеин представляет собой белый порошок без запаха и вкуса.
Сушка казеина производится при температуре в 40 °C, которую постепенно поднимают до 60 °C. Во время такой сушки казеин теряет около 50% своего веса.
Считается, что казеин достаточно просушен, когда его относительно крупные комки не мнутся, а раскалываются с хрустом.
При этом, в отличие от обычных пластиков, так как по своей сути он является белком, казеин также боится высоких температур, как и обычные белки разрушается при них.
Тем не менее, он является более стойким, чем многие белки, и его сворачивание происходит во время длительной выдержки при температуре в 130 °С:
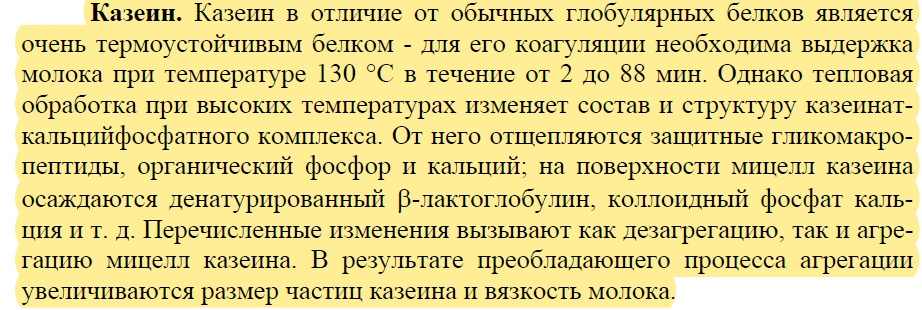
Картинка: О. В. Богатова, Н. Г. Догарева — «Химия и физика молока»
Технология, как мы видим, весьма похожа на технологию производства сыра, — собственно говоря, она и является одной из его технологий, так как и само слово «казеин» происходит от латинского «caseus», то есть «сыр».
В качестве ремарки, несколько отступая от темы: когда я ранее разбирался в технологиях производства сыров, я там для себя отметил любопытный момент, что сыроделы восстанавливают кальций в молоке, который свернулся во время пастеризации, добавляя в последующем в молоко хлористый кальций.
Например, по такой технологии можно сделать один из видов мягкого сыра, как я и описывал в одной из прошлых статей.
Таким образом, получается, что казеину нельзя придать жидкую форму, используя для этого нагревание, как у обычных пластиков. Как же тогда сделать его жидким?
Его можно растворить (то бишь, читай «разжижить») следующими способами: с помощью растворения в молоке, в воде, разбавленных щелочах, сильных кислотах; в слабых кислотах казеин не растворяется и выпадает в осадок (возможно, существуют и другие способы, и этот список не полный).
Кстати, раз уж заговорили о кислотах — для получения казеина не обязательно использовать только уксусную кислоту — для этого в промышленности вполне успешно применяют сворачивание молока с использованием серной и соляных кислот.
Например, для сворачивания с помощью серной кислоты молоко нагревается до 50 °C, после чего в него вливают тонкой струёй разбавленную в 8-10 раз серную кислоту, что даёт сильное нагревание раствора и выпадение казеина, а добавление кислоты прекращают, после того как водный раствор стал прозрачным (т. е. весь казеин выпал).
Далее казеин промывается в двух-трёх водах, при этом стараются использовать мягкую воду, так как жёсткая вода заставляет его разбухать и делает более мягким.
Технология производства с помощью соляной кислоты примерно одинакова с сернокислотной.
Кроме того, можно получать казеин с помощью простого сбраживания молока или добавления к нему кислой сыворотки (я так понимаю, от прежней партии).
Любопытный момент заключается в том, что описанный опыт с получением казеина не является «развлечением гика, которому совсем нечем заняться» — казеин широко представлен в промышленности, где он используется во множестве применений, например, для производства бумаги, красок, бетона, кожевенной промышленности, для производства пластмассовых изделий и даже шин автомобилей!
При этом, исторически казеиновая «пластмасса» предшествовала известным нам, из нефтепродуктов, и берёт своё начало ещё из XIX века, когда она называлась «молочным камнем» — галалитом, из которого делали пуговицы, письменные перьевые ручки.
При этом, такая пластмасса начинает обладать большой прочностью, если её затвердевание происходит под давлением, а при определённых условиях, прочность может быть настолько большой, что такая пластмасса без проблем держит даже попадание пистолетных пуль!
Именно этот способ рассмотрен далее.
Для создания особо высокопрочной пластмассы (как заявляет сам автор следующего видео —
«прочнее стали»), нужно сделать небольшое отступление, так как в этом процессе используется графен, что занятно, приготовленный на дому!
Итак, если вкратце, что для этого нужно: обычное молоко и пластинчатый графит взбиваются кухонным миксером, где, после выключения миксера, в его ёмкости образуется плотный слой пены, а основная масса графита выпадает в осадок. Вот эта пена и содержит, собственно, графен.
Далее пена собирается любым способом, например, простым зачерпыванием чашкой.
Затем этот массив пены высушивается, при этом, высушенный порошок представляет собой графен, который не может слипнуться обратно, так как его частицы покрывает тонкий белковый слой.
Видео этого процесса показано ниже:
Далее необходимо изготовить казеин, уже известным вам способом, с помощью осаждения его из молока, с использованием уксуса. Полученный казеин просушивается на решётке и размалывается в порошок.
Далее, к нему добавляется графен, полученный способом, описанным выше, в количестве 0,5% от объёма казеина.
Далее эта смесь загружается в форму, нагревается до 135 °C и выдерживается под прессом, при давлении в 20 тонн (период времени, к сожалению, не указан).
В качестве идеи: можно попробовать в качестве такого пресса использовать обычный гидравлический домкрат для автомобиля.
Полученный таким образом пластик обладает очень большой прочностью, которая позволяет ему выдерживать как удары ножом (см. с 2:20), так и выстрелы из 9 мм пистолета (по утверждению автора видео):
DIY-бронежилет из молока и графита? Хмм… ;-)
Насколько я понимаю происходящие здесь процессы, и как было описано выше, при 130 °C происходит преобразование частиц казеина, что приводит к их увеличению в размерах, а при выдерживании во время этого нагревания под прессом, — плотное сцепление частиц между собой.
Кроме того, так как в состав был добавлен графен, то его мелкие пластинки ещё больше способствуют взаимозацеплению и, кроме того, не знаю, как правильно это сказать, возникает своеобразный «эффект фанеры» — когда клееный бутерброд намного прочнее, чем цельная доска. Собственно, именно поэтому FDM 3D печать и даёт очень прочные детали, так как каждая деталь составлена из множества слоёв. Думаю, нечто подобное наблюдается и здесь.
Причём, у меня есть большое подозрение, что для создания высокопрочного пластика не обязательно использовать, собственно, графен, а достаточно будет всего лишь обычного пластинчатого графита, так как его пластинки уже помогут созданию структуры «фанеры»…
Таким образом, насколько я понимаю, на выходе получается достаточно вязкая структура, которая упруго сопротивляется разрушающим нагрузкам, где сам казеин служит для создания вязкой основы, а графеновые пластинки — придают прочность всей структуре.
▍ Пластик из картофеля и не только
Но это, что касается «жёсткого и очень жёсткого» пластика. А можно ли сделать самодельный мягкий пластик?
Нет ничего проще: нужно всего лишь взять крахмал, смешать его с уксусом и добавить глицерин. Далее «варить до готовности» — и это не шутка.
В результате получится гибкий и прозрачный пластик, примерно такой, который используется для биоразлагаемых пакетов из вашего любимого продуктового магазина.
Видео получения такого пластика можно посмотреть, например, ниже, только они пошли более трудным путём — вместо готового крахмала они решили его сначала выделить из картофеля, но тем не менее, всё получилось:
А вот тут, можно посмотреть способ, с использованием именно чистого крахмала:
Причём, что интересно в видео выше, там есть целая серия идей, как сделать альтернативные любопытные пластики:
- c 2:45 можно посмотреть, как был сделан армированный пластик, а именно: уже известным нам прозрачным пластиком на основе крахмала была залита обычная марля. Как говорит сам автор, получилось нечто похожее на стеклопластик, только гибкое,
- с 3:36 — что будет, если в пластик добавить какие-либо зёрнышки :-). В результате получится биоразлагаемый пластик, который при выбрасывании в природу, быстро разложится, а на месте его падения вырастут растения! Любопытная концепция и довольно достойная, на мой взгляд — особо радеющие за сохранение природы, могут даже сами изготавливать для себя пластиковые пакеты и «мусорить» ими везде и всюду,
- с 4:09 — что будет, если в пластик добавить желатин (получится особо гибкий пластик, высокой прозрачности).
Ещё больше рецептов биоразлагаемых пластиков можно посмотреть вот здесь, а некоторые подходы по их получению — здесь.
А что насчёт самого известного пластика среди DIY-щиков — PLA (полилактида)? Насколько мне удалось понять, технология его производства, по крайней мере, если следовать классическим промышленным путём, не сказать чтобы совсем проста для самодельщика, но желающие могут ознакомиться с ней здесь или здесь.
А особо дерзкие могут даже попробовать повторить, тем более есть довольно забавное видео, где парни буквально «на пальцах» объясняют её и довольно доходчиво (подсказка — я смотрел в одном из браузеров, с синхронным голосовым переводом; рекламировать браузер не буду — поэтому не называю, думаю, многие в курсе):
Итак, завершая этот рассказ, можно сказать, что создание своего собственного пластика, как мы видим, не является невыполнимой задачей и вполне по силам практически каждому.
Может быть, недалёк тот день, когда и 3D принтеры станут заправлять самодельным PLA-пластиком или его аналогом?
© 2024 ООО «МТ ФИНАНС»
Автор: DAN_SEA