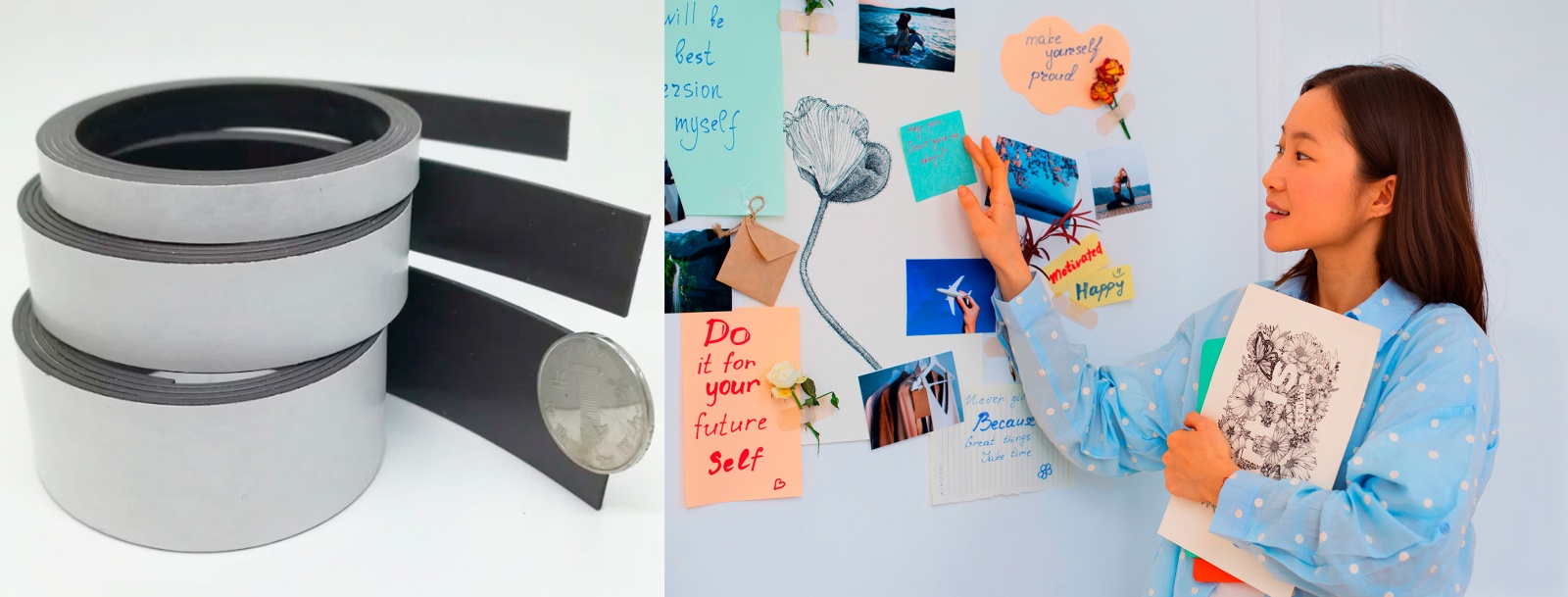
Картинка Aliexpress, Freepik
Все мы хорошо знакомы с гибкими магнитами — кто-то клеит их на холодильник по поводу и без, кто-то (как автор статьи) закрывает с их помощью герметичную камеру 3D-принтера, а кто-то использует в иных технических целях. Что же это такое? Будем препарировать...
▍ Введение
Для создания магнитных эластомеров (именно так их и называют) считается целесообразным применять вещества, имеющие кристаллическую и аморфную структуру, так как они могут проявлять ферромагнитные и ферримагнитные состояния.
Помимо описанного, они должны также обладать высоким электрическим сопротивлением, поэтому в качестве наполнителя для гибких магнитов получили широкое распространение ферриты, под которыми понимается целый класс оксидных магнитных материалов неметаллической природы. Кроме того, могут применяться порошки из сплавов редкоземельных металлов и не только.
В любом случае, ферриты так же, как и любые магнитные материалы, принято разделять на магнитомягкие и магнитотвёрдые, где первые можно отнести к полупроводникам, обладающим высокой магнитной и диэлектрической проницаемостью, причём эта проницаемость уменьшается с ростом частоты; а из магнитотвёрдых изготавливают постоянные магниты.
В настоящий момент известно большое количество ферромагнитных сплавов, которые отличаются достаточной простотой получения — методом закалки расплава, а полученное аморфное состояние может быть стабильным вплоть до нескольких сотен градусов.
Например, можно назвать следующие двухкомпонентные (хотя существуют и двух, и трёх, и более компонентные) ферромагнитные сплавы на базе:
- Только переходных металлов: Fe-Ni, Fe-Cu, Ni-Cr.
- Переходного металла и нормального металла: Fe/Ni/Co — Au, Co/Ni — Ag, Fe/Ni — Pd, Fe/Ni — Pt.
- Переходного металла и амортизатора: Co/Fe/Ni — B/P/C/So/Ge.
- Переходного металла и редкоземельного металла: Co/Fe/Ni — Gd/Tb/Er/Ho/Nd/Pt/Sm/Y/Dy/Lu/Tm/Yb.

Картинка: А. Г. Алексеев, А. Е. Корнев – «Магнитные эластомеры»
Если необходимо изготовить изделие из ферромагнетика в виде тонкой плёнки, обладающее высокой коэрцитивной силой, то для этого применяют отжиг в магнитном поле, в частности, такое делается для сплавов Gd-Co, где причиной роста такой силы является частичная кристаллизация сплава, то есть с помощью применения термомагнитной обработки происходит фиксация промежуточного состояния, между аморфным и кристаллическим. Например, хорошие результаты достигнуты с помощью такого метода и для сплава .
Ещё одним достаточно полезным в качестве наполнителя для эластичных материалов является соединение , так как оно характеризуется высокой остаточной магнитной индукцией и высокой стойкостью к размагничиванию.
Порошки из таких материалов делают с помощью размалывания шаровыми мельницами, однако они, как правило, отличаются высокой окисляемостью кислородом воздуха, поэтому размалывание происходит в атмосфере инертных газов.
Высокие требования к стабильности магнитов во времени, где допускается изменение их магнитных свойств лишь на несколько процентов в течение 10 лет, вызывает определённые сложности, так как порошки редкоземельных металлов активно окисляются кислородом воздуха, и даже если размалывание происходило в инертной атмосфере, то всё равно они успевают вобрать в себя некоторое количество паров воды и соприкоснуться с кислородом во время переходных процессов по добавлению их в эластичное связующее.
Одним из способов борьбы с таким окислением является покрытие порошков из редкоземельных металлов техническим углеродом и полимерами прямо в инертной атмосфере. Также может производиться и гальваническое покрытие.
Очевидными плюсами гибких магнитов на основе редкоземельных металлов являются их высокая коэрцитивная сила и низкая стоимость по сравнению со спечёнными магнитами, так как полезный объём делят между собой не только частицы из магнитного материала, но и частицы эластичного связующего. Из этого последнего факта проистекает и третье преимущество — такой комбинированный материал обладает высоким электрическим сопротивлением, что является весьма полезным для уменьшения вихревых токов, например, при движении магнита относительно другого магнита.
Большинство широко распространённых гибких магнитов остаются работоспособными приблизительно до 60°С, а будучи изготовленными на основе каучуков, сохраняют прочность даже при больших в процентном соотношении порошковых заполнениях, но необходимо оставаться в рамках когезионной прочности, то есть чтобы материал не стал рассыпаться при слишком большом заполнении. Кроме того, большой процент заполнения усложняет формирование готового изделия.
В целом можно сказать, что гибкие магниты обладают слабомагнитными свойствами только за счёт наполнителей с магнитными свойствами, а получение гибких магнитов без наполнителей невозможно.
▍ Полимерная основа
Обычно содержание полимерного компонента в гибком магните колеблется в пределах 5-50% и зависит от типа полимера, назначения магнита и множества других факторов.
Как было уже сказано ранее, кроме магнитного компонента, важнейшим компонентом является также и эластичное связующее, так называемый эластомер, в качестве которого могут выступать каучуки, термоэластопласты, полиуретан и ряд других компонентов.
Так как натуральный каучук является достаточно дорогим, в качестве его заменителей могут использоваться аналоги, например, изопреновый, хлоропреновые, бутилкаучук, бутадиен-нитрильные, бутадиен-стирольные, этилен-пропиленовые и т. д.
По своим механическим свойствам они не уступают натуральному каучуку и, кроме того, имеют ряд дополнительных положительных свойств, например, этилен-пропиленовые каучуки успешно сопротивляются воздействию агрессивных сред при относительно высокой температуре 100-150°С, а силоксановые более термостойки и могут длительно выдерживать высокую температуру порядка 100-200°С, в то время как бутадиен-нитрильные и хлоропреновые могут успешно сопротивляться воздействию масел и растворителей.
Выбор конкретного типа эластомера диктуется теми условиями, в которых будет эксплуатироваться в дальнейшем гибкое магнитное изделие.
▍ Технология получения магнитных материалов
Как было уже сказано выше, в производстве гибких магнитных материалов широко используются ферриты, поговорим о них более подробно.
В основном их получают керамическим способом, а также выращиванием в виде монокристаллов (незначительную часть). Основными компонентами при производстве ферритов выступают оксиды, гидроксиды и соли металлов.
Самым простым объяснением способа производства ферритов будет синтезирование из оксидов, являющихся продуктом термического разложения солей и гидроксидов.
Ферритовые материалы в основном получают тремя промышленными способами:
- с использованием механической смеси оксидов или карбонатов;
- с помощью термического разложения солей, которые были получены с помощью выпаривания из раствора;
- с использованием совместно осаждённых гидроксидов, оксалатов.
При этом первый процесс протекает достаточно медленно, так как определяется скоростью диффузии. Низкая скорость объясняется более совершенной кристаллической решёткой у твёрдых частиц, в то время как для ускорения спекаемости необходимо, чтобы в кристаллической решётке присутствовали дефекты.
В противовес первому способу, второй и третий протекают гораздо быстрее, так как перемешивание компонентов производится на молекулярном уровне.
При втором способе, когда происходит термическое разложение, предварительно компоненты смешивают в воде, которую потом нагревают до 70°С, что позволяет солям полностью раствориться и получить насыщенный раствор солей в воде. Далее этот раствор выпаривают, что приводит к его выкипанию и дальнейшему прокаливанию осадка, в свою очередь, ведущему к активному образованию ферритов.
При третьем способе, как и при предыдущем, получают водный раствор солей, однако далее из этого раствора, применяя водный раствор аммиака или щелочей, стимулируют выпадение осадка. Этот способ особенно хорош тем, что при этом происходит очень тонкое перемешивание компонентов, его дегидратация и образование феррита протекает при комнатной температуре.
Но всё же самым простым способом является производство ферритовых материалов, заключающееся в смешивании порошкообразных исходных компонентов, представленных оксидами и карбонатами металлов; после чего смесь сушится, прессуется, проходит предварительный обжиг, ещё один помол и прессовку, а затем окончательно спекается.
Но это то, что касается классической технологии производства ферритов, а как же обстоят дела при производстве наполнителя для эластомеров?
Общую схему производства наполнителей можно описать следующим образом: тонкий помол исходных химически чистых оксидов, их перемешивание, обжиг, гранулирование порошка.
Минусом такого способа является плохая повторяемость результатов, так как, для того чтобы добиться нужного качества, процедуры обжига и размельчения могут повторяться и результаты в отдельных партиях могут отличаться друг от друга.
Для борьбы с этим может использоваться другой способ — осаждение гидроксидов из водных растворов соответствующих солей металлов, после чего осадок прокаливается. Стабильный результат в этом случае достигается тем, что осаждение происходит при всегда одном и том же pH раствора, так же как и прокаливание при одной и той же температуре (1220-1250°С) и охлаждение с одной и той же скоростью (60-70°C/час).
Выше уже говорилось о помоле полученных ферритовых материалов и, следует отметить, что при переходе от монолитного магнитного материала к порошку свойства магнитного материала меняются в зависимости от размера частиц порошка.
При таком переходе магнитомягкие материалы снижают свою магнитную проницаемость и увеличивают коэрцитивную силу, пропорционально уменьшению размера частиц.
Причиной этого является то, что магнитная проницаемость у частиц представлена в виде градиента и растёт по мере продвижения от центра к периметру частицы, и чем частица меньше, тем у неё больше плотность поверхностного слоя и выше коэрцитивная сила и меньше магнитная проницаемость. Тем не менее, нельзя уменьшать частицы до бесконечности: если размер частицы приближается к нижнему пределу существования ферромагнетизма, то у неё начинает уменьшаться и коэрцитивная сила.
В практическом смысле это означает, что если в качестве наполнителя для эластомера используются молотые магнитотвёрдые материалы, то размер частицы таких материалов должен быть порядка 1 мкм, а если магнитомягкие материалы, то 50-250 мкм.
Выше уже говорилось о делении эластомеров — на изготовленные с применением наполнителя из магнитомягких материалов и магнитотвёрдых материалов.
Магнитомягкие материалы используются для изготовления эластичных магнитопроводов, а также электромагнитных экранов. Таким образом, при изготовлении магнитомягких эластомеров основным является получение такого конечного продукта, который отличается высокой магнитной проницаемостью, небольшой коэрцитивной силой и варьирующегося по своей электропроводности.
В противовес первым, магнитотвёрдые материалы используются для производства гибких постоянных магнитов, где способы создания подразделяются на использующие обычные ферритовые наполнители и редкоземельные магниты.
Необходимым элементом технологического процесса получения постоянных гибких магнитов является намагничивание, и для этого используется магнитное поле определённой структуры и напряжённости, а так как магнитотвёрдые материалы обладают большой коэрцитивной силой, то для их намагничивания используются магнитные поля с напряжённостью, которая превышает их коэрцитивную силу в 5-7 раз.
Для их создания используется мощная магнитная установка, в которой эти поля возникают импульсно, вследствие разряда батареи конденсаторов через намагничивающее устройство.
Такой импульсный способ является достаточно привлекательным, так как достаточно прост технологически, может быть легко автоматизирован и встроен в поточную линию, позволяет успешно бороться со скин-эффектом у обрабатываемого материала, так как магнитотвёрдые материалы обладают большим сопротивлением.
Ниже показаны три способа намагничивания:
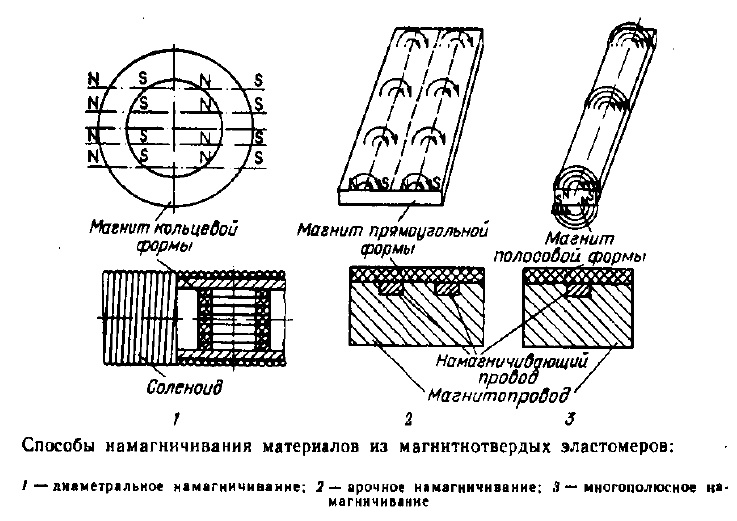
Картинка: А. Г. Алексеев, А. Е. Корнев – «Магнитные эластомеры»
Экспериментально было выявлено, что наиболее простым способом является показанный на рисунке выше способ 2 — арочное намагничивание. В ходе такого процесса намагничивающий провод, представленный изолированным проводником, располагается прямо под обрабатываемым изделием, на равном расстоянии от краёв и от друг друга (если проводов несколько) и по нему пропускается импульс тока от конденсаторной батареи. При таком способе намагничивания на поверхности изделия образуются два магнитных полюса (показаны на рисунке выше).
Подытоживая, можно сказать, что в быту, как мы можем наблюдать вокруг, магниты последнего типа широко распространены и используются как в декоративных целях (те же самые «магнитики на холодильник»), так и для технических целей в качестве разнообразных реле, отклоняющих электромагнитных систем и даже в качестве постоянных магнитов для генераторов тока.
▍ Список использованных источников
- А. Г. Алексеев, А. Е. Корнев – «Магнитные эластомеры»
- М. Ф. Бухина – «Техническая физика эластомеров»
Автор:
DAN_SEA