Привет!
Хочу поделиться опытом и рассказать о том, как я создавал испытательную установку, начиная от проработки механики и принципа действия электроники и заканчивая изготовлением готовой лабораторной машины. Фишка установки в том, что управляется она любительской электроникой и находится на стыке DIY-прибора и промышленного образца.
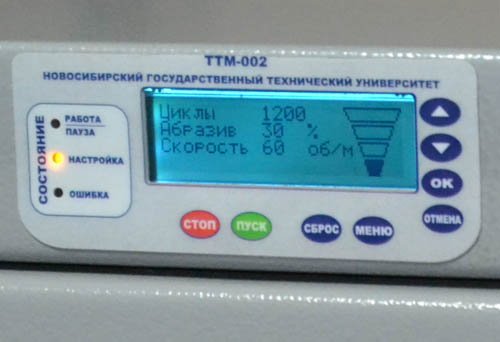
Я учился на кафедре Материаловедения в машиностроении, где ведутся разработки новых материалов и покрытий. Как известно, одним из важных показателей материала является его износостойкость. Существует ряд ГОСТов на различные виды испытаний износостойкости материалов. Один из таких ГОСТов (ГОСТ 23.208-79) предусматривает испытания материалов о нежестко закрепленные абразивные частицы. Да вот беда: стандарт есть, а установок таких никто не выпускает. Моей задачей было создать установку, способную проводить испытания согласно ГОСТу плюс ускоренные испытания в условиях вечного «мне нужно вчера». О создании такой машины я и хочу вам рассказать…
Анализ функционала и техническая проработка родили на свет следующую схему работы устройства.
С помощью зажима испытуемый образец закрепляется в рычаге. Перемещая компенсатор веса по винту, рычаг выставляется в равновесное состояние. Устанавливая откалиброванную гирю в одно из отверстий рычага, мы прижимаем образец к ролику с известной силой. При вращении шнека песок поступает в зону контакта ролика и образца. Ролик начинает вращаться и истирает образец. По окончанию испытаний замеряется потеря массы образца. По потере массы можно судить, на сколько материал стойкий к абразивному износу. Подробно процедура испытания описана в ГОСТ 23.208-79.
Управляющая электроника
Задача, с точки зрения электроники, довольно проста – необходимо управлять 2-мя приводами, держать постоянную скорость вращения привода ролика ±2 об/мин, считать количество оборотов ролика. По завершению заданного количества циклов (оборотов ролика) остановить испытание. Также было бы неплохо контролировать уровень песка в баке. Со стороны руководителей было предложено много различных вариантов реализации управления установкой. Все они сводились примерно к такому виду:
Изображение взято с сайта http://electronics-lab.ru
Мне же хотелось сделать панель оператора на современном уровне, с дисплеем, меню, различными режимами работы и прочими вкусностями. Проблема была лишь в том, что я никогда не работал с микроконтроллерами, а на разработку системы на стороне кафедра деньги, естественно, не выделила бы. В поиске простых и недорогих решений я наткнулся на отечественный проект Master KIT (к настоящему времени компания деактивировала свой профиль с Хабра) с множеством готовых решений, уроков, примеров, драйверов и кодов – всем тем, что так необходимо новичку. Стоит отметить, что тогда я еще не знал про Ардуино, в противном случае выбрал бы именно его, как еще более простое и еще более дешевое решение.
Основная программа по управлению системой будет храниться в модуле управления BM9300H от Master KIT. Этот модуль имеет на борту интерпретатор BASIC PIC, что дает возможность нубам, вроде меня, запрограммировать систему на интуитивно понятном Бэйсике. Взаимодействие с системой будет осуществляться через панель оператора BM9321. Панель имеет дисплей и 8 кнопок и общается с управляющим модулем по RS485. Вращать шнек будет шаговый моторчик, а управлять моторчиком, в свою очередь, будет модуль управления ШД BM9310. Для объединения модулей нужна плата расширения BM9399.
Выбор привода ролика
Резиновый ролик должен вращаться с постоянной скоростью, несмотря на динамически меняющуюся нагрузку (из-за неоднородности песка и прочих факторов). Кроме того, необходимо обеспечить широкий диапазон скоростей от 30 до 240 об/мин (для ускоренного испытания). Рассматривались следующие варианты:
- Асинхронный мотор-редуктор с частотным преобразователем.
- Коллекторный мотор-редуктор постоянного тока с управлением ШИМ и обратной связью по датчику.
- Шаговый двигатель с блоком управления.
Разберем по порядку:
- Асинхронный мотор-редуктор с частотником — штука хорошая. Частотный преобразователь может поддерживать постоянную скорость вращения с обратной связью по току без датчиков на выходе. Однако в нашем случае датчик все равно понадобится для подсчета количества оборотов. Широкий диапазон скоростей тоже не вопрос. Только сборка такая стоит недешево, один только мотор-редуктор 180 Вт обойдется около 15 000 руб.
- Мотор-редуктор постоянного тока будет стоить примерно также как асинхронник. Но здесь придется поработать с поддержкой постоянной скорости с обратной связью по датчику. Также дело осложняется обеспечением большого диапазона скоростей.
- Шаговый двигатель будет стоить дешевле из-за отсутствия редукторной части, а функции свои выполнит на 100%, избавит от проблем с контролем скорости и подсчетом оборотов. Сколько шагов задал – столько мотор повернул – easy money. Минус ШД в низком КПД, также есть проблемы с вибрацией, но их частично можно решить виброгасящими прокладками. На шаговом двигателе мы и остановимся.
Согласно расчетному моменту был подобран двигатель FL86STH80 (тогда он стоил 5 000 руб.) с драйвером OMD-88 (4 200 руб.) и блоком питания PW4873B (2 200 руб.). Формировать управляющие импульсы для OMD-88 будет, опять же, китовский модуль расширения BM9307 с загруженной на него программой управления ШД.
Датчики уровня песка
Другой интересной задачей было обеспечить оператора информацией о количестве песка в баке. Можно, конечно, сделать прозрачный бак из оргстекла и следить, чтобы песок не закончился во время испытания, но это не наш подход. Нужно процесс автоматизировать, в случае предельно низкого уровня песка, поставить испытание на паузу. В итоге получилась следующая схема:
Т.е. принцип действия предельно прост: если датчик принимает сигнал от излучателя – песка на этом уровне нет. Для управления всем этим хозяйством спаял отдельную плату – “ Модуль датчиков песка”.
Принципиальная электрическая схема
В итоге получилась вот такая схема:
А располагаться в корпусе это будет примерно вот так:
Сборка прототипа
Прототип — штука необходимая для того, чтобы выявить все возможные подводные грабли на раннем этапе. Да что уж там говорить – схема может оказаться вообще нерабочей. В общем, из алюминиевых уголков, деревянных брусков и сподручных материалов был собран прототип.
Согласен, прототип получился убогим, но свои задачи выполнил: выявил множество проблем и подарил бесценный опыт. Самое главное на данном этапе — не оставить все как есть, собраться с силами и довести дело до ума. Итак, продолжим…
Выбор типа корпуса
Корпус машины – это как тело женщины, это первое, на что обращается внимание. Поэтому корпус должен быть привлекательным и обаятельным. С помощью SolidWorks я создал 2 модели, первая рассчитанная на изготовление корпуса из пластика или стекловолокна, вторая – на гибку стального листа. Для общего представления: габариты спроектированной машины 500х500х900 мм.
Первый вариант корпуса выглядит довольно эстетично, но изготовить такие панели будет очень дорого или в случае изготовления из стекловолокна очень трудоемко. Пластиковый вариант, возможно, подойдет для серийного экземпляра, когда отобьется стоимость формы. Поэтому однозначно побеждает стальной корпус. Сейчас рынок заполнен множеством предприятий, занимающихся лазерной резкой и листовой гибкой. Причем гибку осуществляют очень точную и аккуратную, а главное недорогую (около 20 рублей за гиб в зависимости от толщины листа, серийности и жадности).
Производство
Для изготовления установки были сделаны чертежи всех деталей и сборок в SolidWorks. Чертежи ассоциативны c 3D моделью, что значительно упрощает жизнь, т.е. когда вносятся корректировки в модель, а в процессе разработки они вносятся очень часто, то чертежи перестраиваются автоматически, ну или с минимальными доработками. Производство установки можно условно разделить на следующие этапы:
- Изготовление рамы. Рама была сделана из стальных квадратных труб, сваренных между собой. Собрать раму из труб довольно просто, но недооценивать этот этап не стоит. В случае неточных размеров рамы или ее формы кожух может не налезть, дверь не закрыться, ящик не заехать и другие интересные сюрпризы обязательно вылезут при сборке. Поэтому трубы были отрезаны с припуском, а затем отфрезерованы по торцам в нужный размер в допуске ±0.5 мм с обеспечением перпендикулярности относительно стенки.
- Токарные и фрезерные детали (стойка двигателя, стойка рычага, корпус шнека, вал, муфта и гири) были изготовлены на нашей же кафедре. Для подобных вещей у университета есть все необходимое оборудование. Современные станки и люди с руками дают на выходе детали отличного качества без необходимости применения напильника.
- Листовые детали (корпус, двери, бак, ящик для отработанного песка, рычаг и разная мелочевка типа кронштейнов, пластин и т.д.) вырезаны лазером и согнуты под заказ. Вместе с материалом эти детали обошлись примерно в 5 000 руб. Правда, дизайнерские финты в виде закруглений с большим радиусом пришлось гнуть самому вручную. Но дело это не сложное, стальной лист толщиной 1 мм довольно податлив.
- Окно из оргстекла. Оргстекло нужно было согнуть по радиусу, чтобы его форма совпала с формой двери. Оргстекло оказалось тоже очень податливым материалом, как только на помощь пришел промышленный фен.
- Фальшпанель представляет собой наклейку с прозрачными окнами под дисплей и светодиоды. Наклейку сделали также под заказ, для этого нужно было ее нарисовать в векторе и заплатить 3 200 руб. за 6 наклеек. Хотя наклейка нужна была всего одна, 6 штук – минимальный заказ (видимо, по размеру листа).
Итог
После всех сварочных работ, сборки, шлифовки и доводки, установка была разобрана до винтика и все детали отданы на полимерную покраску. После чего, естественно, опять собрана. В результате получилась вот такая установка с умным названием триботехническая машина ТТМ-002. Два — потому что вторая после прототипа.
Чтобы не листать наверх, выкладываю фото панели оператора еще раз. Перед началом работы оператор настраивает количество циклов в испытании, скорость вращения ролика и скорость подачи песка в процентах от максимального значения. В правой части дисплея индикация уровня песка. В меню можно выбрать различные режимы работы и поменять настройки. Например, режим «Без подачи песка» может понадобиться для приработки ролика или режим «Без вращения ролика» — для быстрого ссыпания содержимого бака.

Всего на установку было потрачено примерно 45 000 руб., конечно, не считая мой труд и труд моих коллег, которые мне помогали с ее изготовлением. А сил было вложено немало. Весь процесс от идеи до готовой установки занял 2 года (2010-2012), но это было с большими перерывами по несколько месяцев, плюс последний год я работал на заводе, а установкой занимался после работы и по выходным. Стоит отметить, что каждая покупка комплектующих это целая эпопея, которая занимает массу времени и доставляет много головной боли (кто занимался покупками через университет, несомненно, меня поймет). Дело в том, что госучреждения с e-bay не сотрудничают работают по 30% предоплате, на что даже российская не каждая компания пойдет. Есть, конечно, левые схемы варианты оплаты с как бы произведенной отгрузкой, но не будем об этом. В настоящее время установка работает на кафедре Материаловедения в машиностроении Новосибирского государственного технического университета, испытывает наноматериалы, в общем, служит на благо отечественной науки.
Чтобы не превращать статью в трехтомник, я не стал подробно описывать многие вещи. Однако буду рад ответить на ваши вопросы и добавить деталей.
Автор: INevzorov