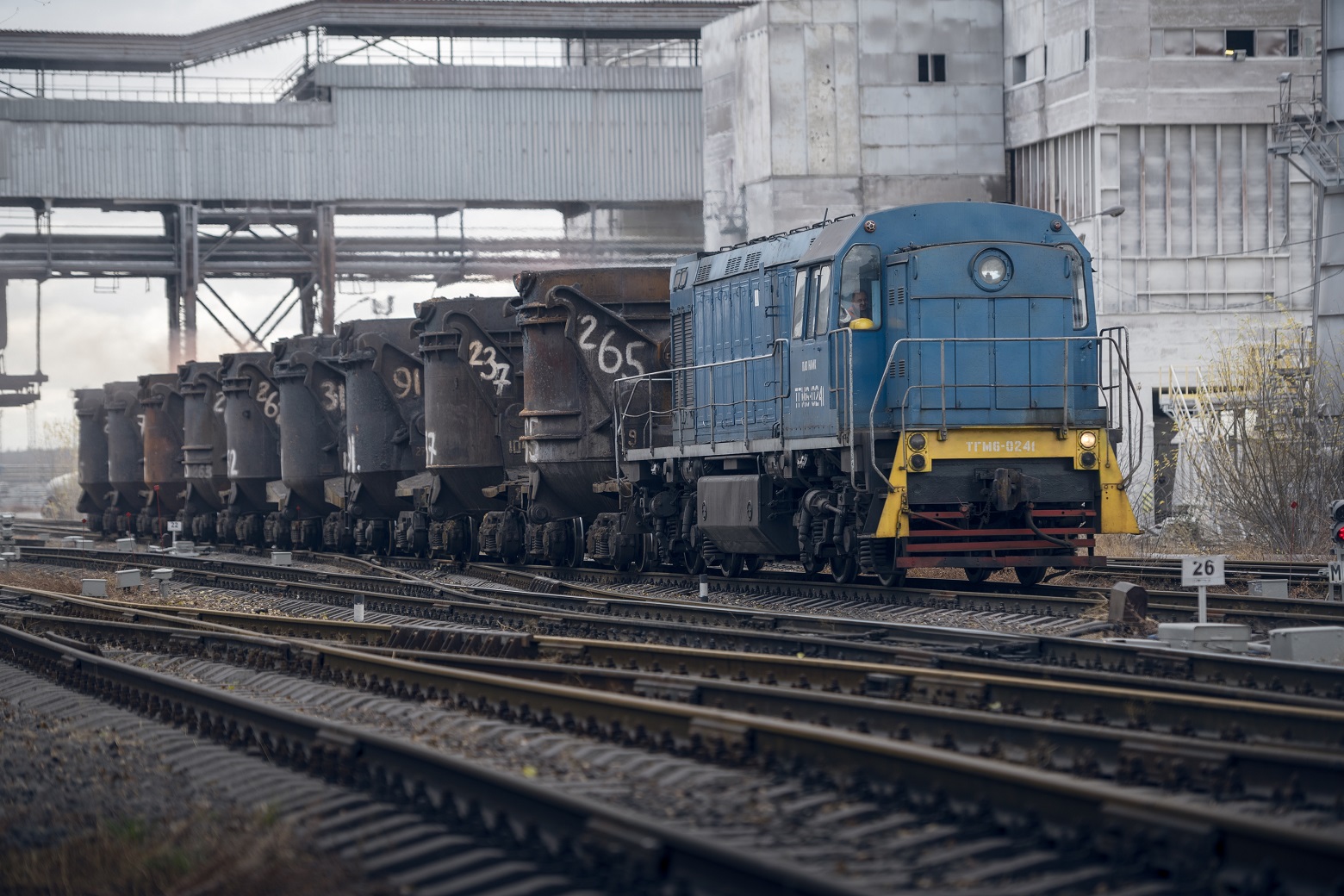
Чугун — сплав железа с углеродом, в котором содержание углерода более 2,14%. Так звучит точное определение для металлургов. А для обывателей слово «чугун» ассоциируется с бабушкиной сковородкой или радиатором с закосом под старину. Это прежде всего металл, который затем становится сталью. Однако на качество сплава напрямую влияет время промежуточных операций с расплавленным чугуном. Чем быстрее мы довезем его от доменной печи до конвертерного цеха, тем лучше получится сталь, меньше потратится ресурсов на ее производство и лучше сохранится ковш, в котором едет чугун.
Почему для отслеживания ковшей с расплавленным чугуном мы выбрали технологию RFID и почему наши метки не горят — расскажу в этой статье.
Сохраняя градусы
Температура чугуна на выходе из печи составляет примерно 1500℃. На пути от доменной печи к конвертерному цеху он охлаждается. Наша задача — потерять как можно меньше градусов и довезти его максимально горячим. Для этого ковши необходимо отслеживать на всем пути их следования.
Раньше этот процесс был исключительно аналоговым. Вся информация — между диспетчерами, железнодорожниками, машинистами — передавалась по телефону или рации. Данный способ имеет более низкую скорость передачи информации в отличие от цифрового способа.
Например, диспетчер неправильно оценил обстановку — ждал чугун с одной печи, а налили быстрее на другой. Пока тепловоз перегнали к нужной точке, миксерное отделение осталось без чугуна. График сорван.
Или произошла задержка в транспортировке — из-за поломки тепловоза или долгого осмотра ковша. Ковша нет, и мастер не может открыть выпуск. Приходится предпринимать какие-то корректировки, чтобы снизить потери производства.
Чтобы ковши не «терялись» или простаивали, нужно знать, где именно находится каждый из них в конкретную минуту. Можно отслеживать сам тепловоз (кстати, мы так тоже делали), но точной информации — куда он едет, с полными ковшами или пустыми — это тоже не дает.
DEM + RFID = наглядность
Для отслеживания ковшей мы решили использовать RFID-метки. В основе решения лежит платформа «DEM — Цифровая Модель Предприятия» и аппаратная система с RFID-оборудованием (метки, считыватели, антенны), железом для его коммутации и опорно-монтажными конструкциями.
Вообще миссия DEM — это внедрение комплексной цифровой прослеживаемости товарных, производственных логистических потоков с применением технологий «цифрового двойника», машинного зрения и RFID.
Вот за что мы любим это решение:
-
полная цифровизация и автоматизация операций считывания данных о бизнес-процессах;
-
есть интерфейс агрегации всех данных на удобной цифровой модели предприятия;
-
считывание идентификаторов происходит без участия человека — человеческий фактор полностью исключен;
-
может считывать сотни идентификаторов в секунду;
-
пользовательское ПО не требует установки на компьютер — это веб-интерфейс.
В рамках контроля циклов движения ковша наиболее оптимальный вариант применения DEM — это создание полноценного цифрового двойника комплекса с выводом мнемосхем в диспетчерские:
-
диспетчерская доменного цеха (ДЦ);
-
диспетчерская конвертерного цеха (КЦ);
-
диспетчерская комбината/ситуационный центр;
-
диспетчерская управления железнодорожного транспорта (УЖДТ).
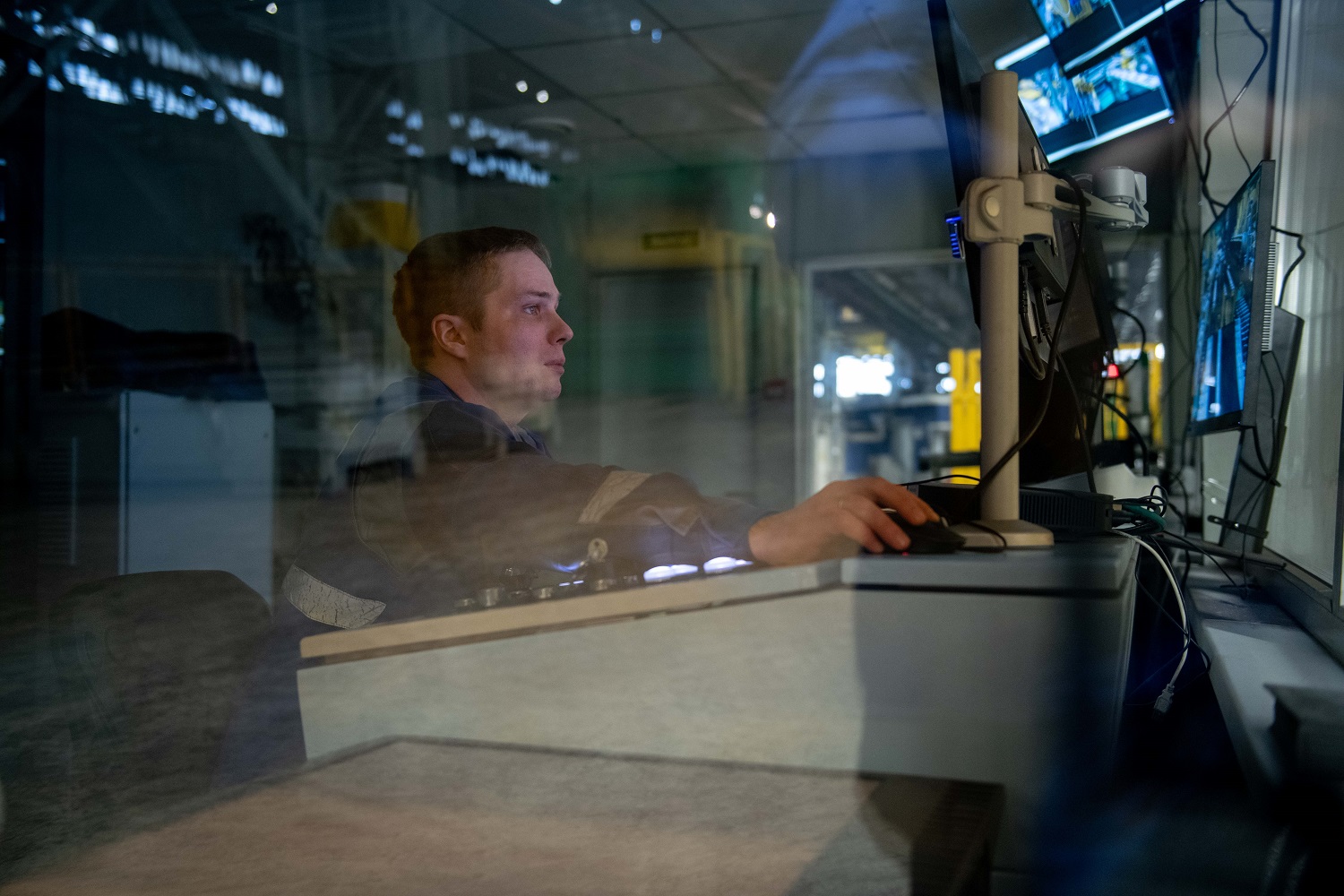
Чтобы наша DEM могла следить за транспортировкой чугуна, нужно было не только разметить сами ковши, но и установить оборудование на всем пути их следования. А точнее, на ключевых точках этого маршрута:
-
на въезде и выезде с приемно-отправочного парка;
-
на въезде в миксерное отделение;
-
на весах;
-
на въезде в депо очистки ковшей (ДОК);
-
в доменном и конвертерном цехах.
В каждой точке мы смонтировали защищенный шкаф с RFID-оборудованием и две RFID-антенны. В зависимости от индивидуальных особенностей каждой конкретной точки монтаж производился либо на несущие элементы инфраструктуры, либо на специальные кронштейны. RFID-антенны, расположенные в «горячих» цехах, оснастили дополнительными защитными кожухами.
Вот так выглядит шкаф с RFID-оборудованием:
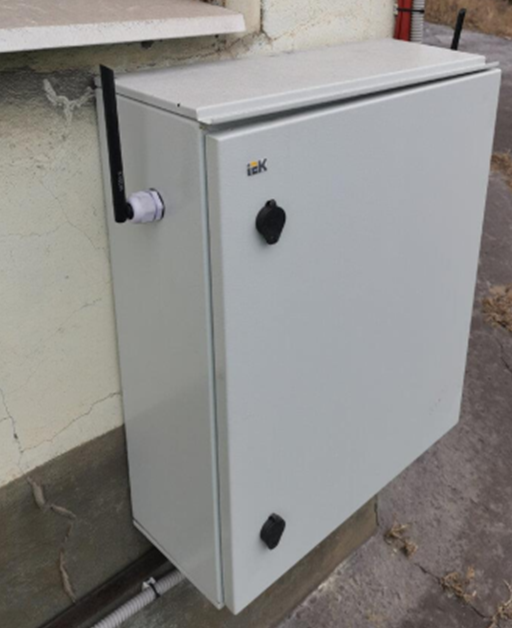
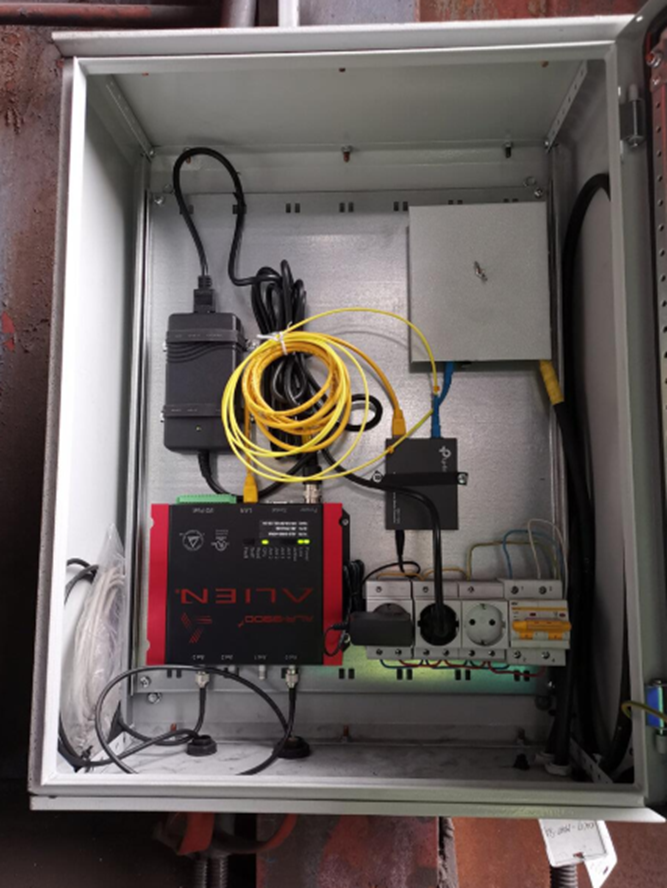
На все чугуновозные ковши мы установили RFID-метки, по две на каждый (6 меток, 4 со стороны слива в МО и 2 со стороны слива на разливочные машины) — с двух сторон. Температура ковша снаружи довольно высокая — около 150-200 градусов, поэтому метки использовали жаростойкие.
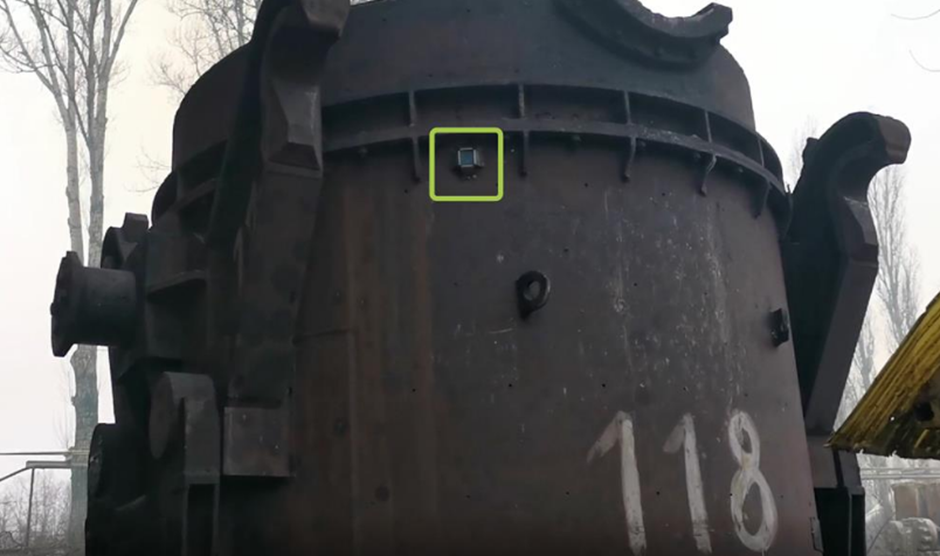
На этом этапе мы столкнулись с определенными сложностями.
Несмотря на то, что футеровка ковша хорошо удерживает температуру, метку нельзя смонтировать прямо на корпус. И не только потому что очень горячо — из-за конструктивных особенностей ее просто невозможно там надежно закрепить.
Поэтому каждую метку мы поместили в стальной корпус особой конструкции и залили теплоизоляционным и жаропрочным материалом, который исключает прямой кондуктивный теплообмен метки с ковшом и собственным корпусом, а также конвективный теплообмен с окружающей средой.
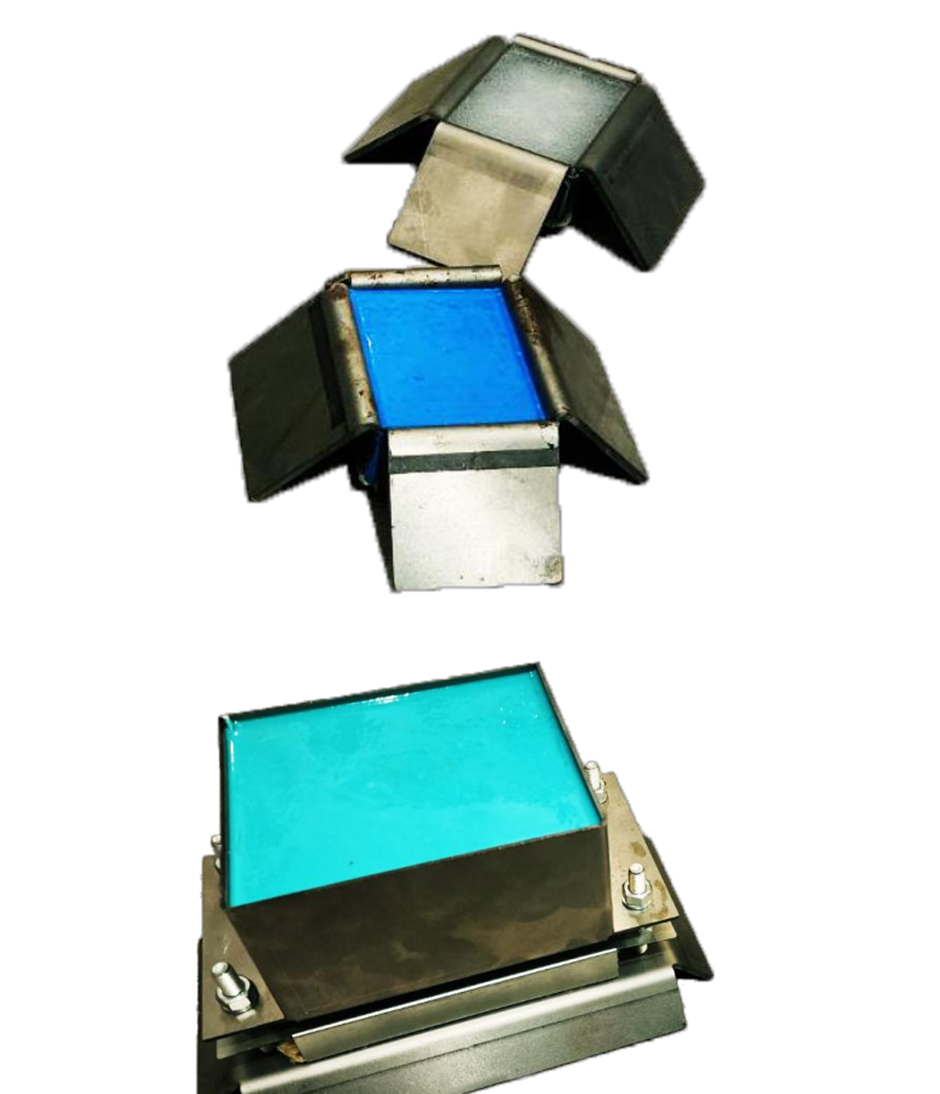
Такая конструкция, помимо всего прочего, защищает метку от разного рода механических и климатических воздействий. Для монтажа корпуса метки на стенку ковша использовали старую добрую сварку — она обеспечивает надежную и долговечную фиксацию в суровых условиях металлургического комплекса.
Чтобы вся эта система — метки на ковшах, оборудование в полях и программная платформа, начали работать вместе, DEM нужно было настроить. Вот как это было.
-
Создали цифровую копию комплекса в виде мнемосхемы.
-
Отметили точки контроля и идентификации ковшей в соответствии с физическим расположением оборудования.
-
Интегрировали DEM с существующей ERP-системой.
-
Внесли метки в систему.
-
Разработали сценарии работы во встроенном в DEM редакторе.
-
Создали учетные записи для диспетчеров. (Мы создали сервисные УЗ для Горновых при входе на «банкоматы», а так все входят под своими УЗ).
Платформа готова к работе! Даже если в будущем комплекс или оборудования как-то изменяться, все эти изменения можно будет отразить в DEM, просто отредактировав, добавив или убрав соответствующие элементы.
Как это работает сейчас
Метка на ковше попадает в область сканирования антенн в какой-либо из точек, после чего информация мгновенно отображается в системе и на мнемосхемах. В диспетчерских ДЦ, КЦ и УЖДТ выводятся мнемосхемы в соответствии с их зонами ответственности, в диспетчерской комбината — мнемосхема всех зон в виде единой карты (все видят одинаково и могут любой участок открыть).
К каждой метке привязан уникальный ID ковша. По нему можно узнать много полезного — температуру, номер выпуска, химический состав, маршрут движения.
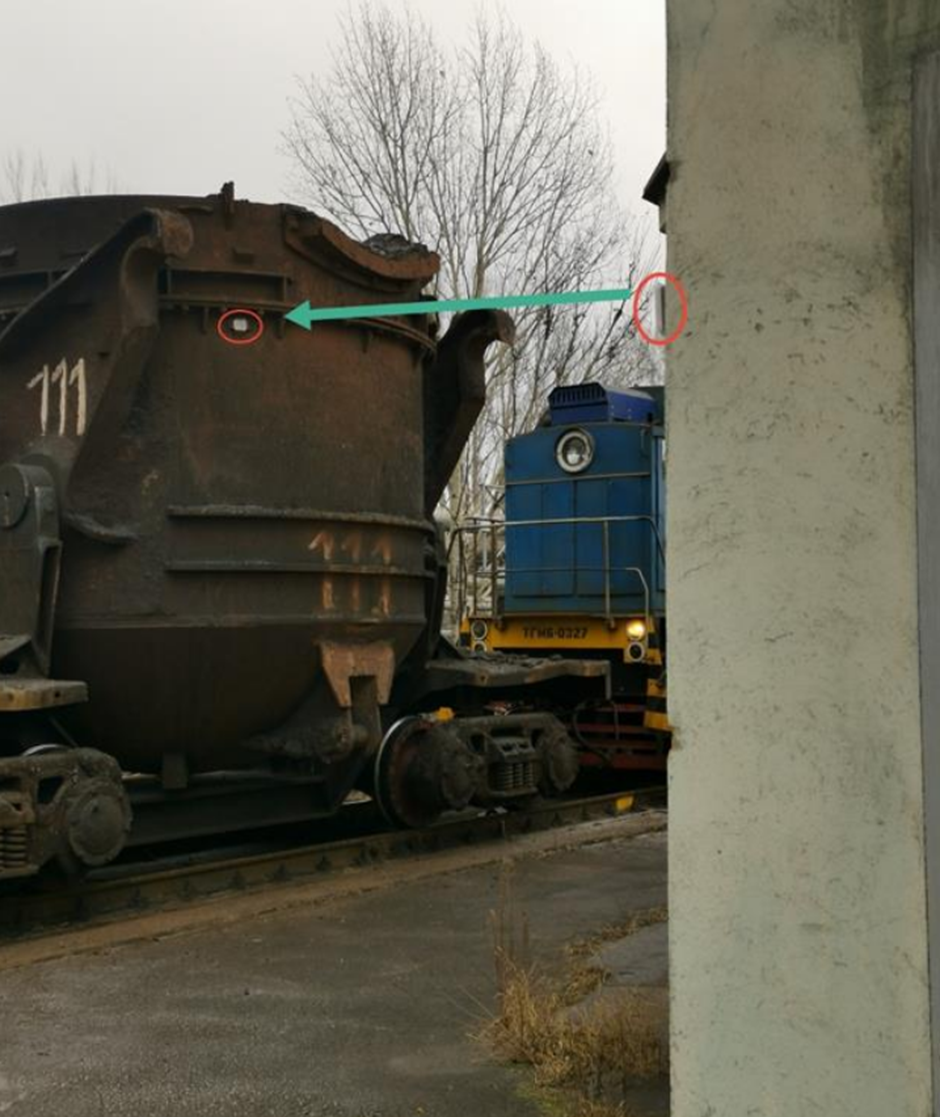
Благодаря мнемосхеме диспетчер (и не только, например горновые, газовщики, мастера и пр.) всегда знает, где находится каждый конкретный ковш, и может отследить весь его жизненный цикл, включая:
-
время закрытия выпуска;
-
время прохождения весов;
-
время возврата на весы;
-
время постановки под печь;
-
время нахождения ковша в КЦ;
-
время нахождения на участке разливки;
-
время заездов в ДОК;
-
точное время любых ожиданий на путях или под печью/при сливах ковша.
Теперь движение ковшей — максимально наглядный и прозрачный процесс. Их перемещения отображаются в режиме реального времени на мнемосхеме в диспетчерской (у всех, ЦПУ печей, банкоматы, ДОК, РМ, и множество прочих мест). В системе видны все ковши и их статус — груженые они или нет, где они находятся. Также информация выводится на сенсорную панель, с которой работают горновые. Они отмечают, какие ковши налиты, какие наливаются, уровень налива (уровень передается с уровнемеров).
Благодаря внедрению решения мы сократили время простоя ковшей и снизили теплопотери расплавленного чугуна при транспортировке. Прозрачность процессов значительно возросла: теперь мы точно знаем, насколько хватает ресурса ковшей, что позволяет эффективно планировать работу, избегать хаоса и действовать организованно.
А еще стало легче проводить плановое техническое обслуживание. Мы видим историю всех ковшей — и те, кто пережил более 450 наливов, подвергаются более тщательному осмотру и при необходимости отправляются на ремонт. За это отвечает наш сервис тепловизионного контроля — он отслеживает наружную температуру ковшей и выделяет зоны горячее 190 С. Ковши с превышением подвергаются более тщательному осмотру.
Вообще связку DEM + RFID можно без проблем масштабировать за пределы ковшей с чугуном. Например, теперь с помощью меток мы отслеживаем транспортировку лома и хотим реализовать еще один проект по отслеживанию сырья в стационарных бункерах.
Автор: ivankn1984