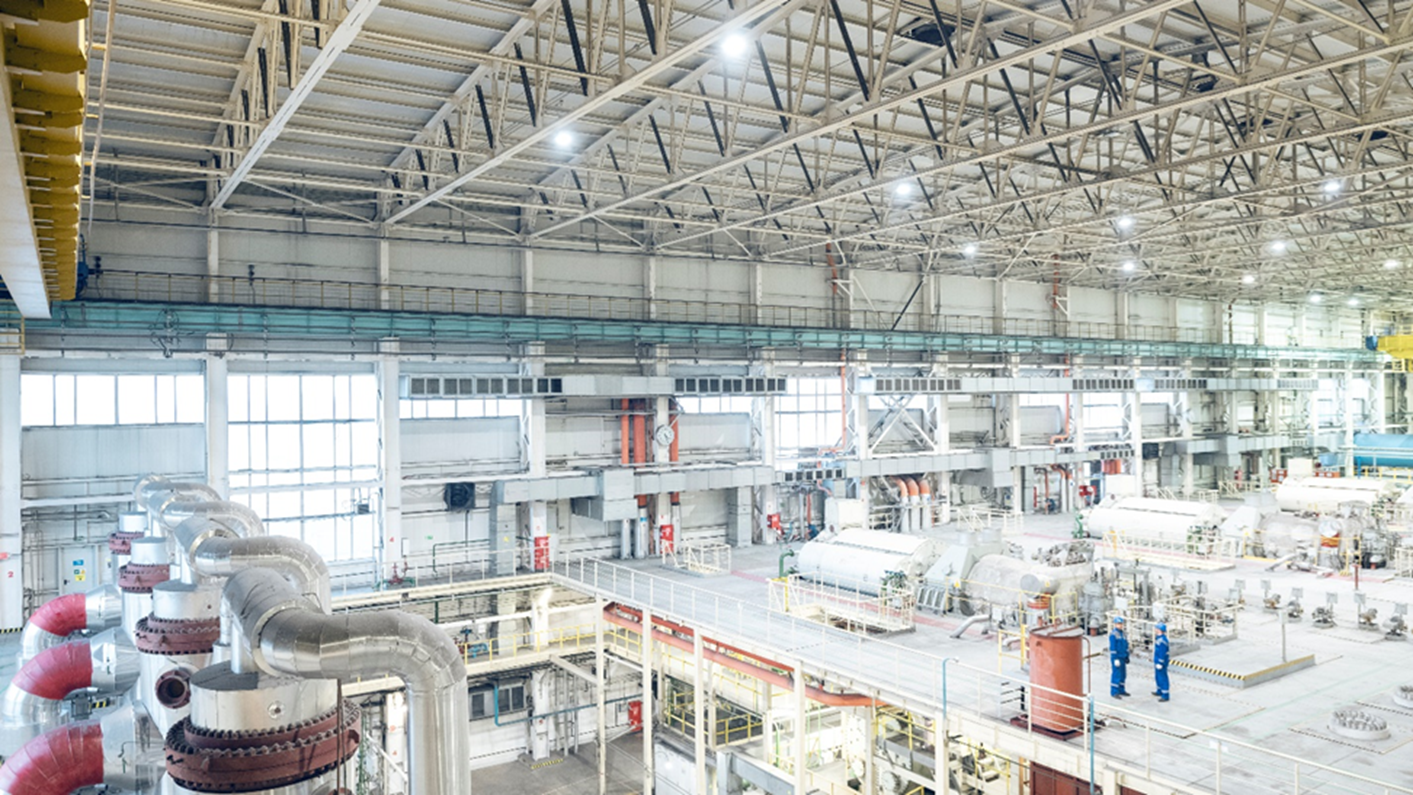
Я пришёл в ИТ с ТЭЦ. На самой теплоэлектроцентрали Новолипецкого металлургического комбината (НЛМК) работал сначала оператором котлов, потом инженером производственно-технического отдела (ПТО). В период работы в ПТО мы активно решали задачи по своевременности остановок турбогенераторов на чистку, а на ТЭЦ уже стали разрабатывать первые цифровые советчики, пока ещё в котельном отделении. Мне тут же пришла в голову идея сделать цифровой помощник, который бы оценивал состояние конденсатора турбины и рекомендовал, когда же выгодно останавливать турбогенератор на чистку. В «Цифре» у нас есть команда людей, которая ищет способы делать что-то эффективнее, и, если кто-то высказывает перспективную идею, около него сразу появляются разработчики. Мой случай создания цифрового продукта был необычен тем, что я одновременно выполнял роль и эксперта, и разработчика. Второе получалось сложнее, но коллеги-цифровизаторы активно помогали мне набить руку в этом деле. В итоге сначала я высказал идею, потом стал экспертом, потом посчитал матмодель, а затем неожиданно для себя оказался в роли разработчика в цифровой команде энергетиков.
Расскажу про основные технологические процессы на ТЭЦ. На котельных агрегатах мы сжигаем природный, доменный и коксовый газ, получая тепло. Этим теплом нагреваем воду и превращаем её в энергетический пар среднего (32 ата) и высокого (100 ата) давления. Потом этот пар заставляет вращаться различные агрегаты: компрессоры, турбовоздуходувки, турбогенераторы (ТГ). В этой статье нас больше всего интересуют ТГ. Данные агрегаты вырабатывают электроэнергию, а отдавший практически всю свою потенциальную и тепловую энергию пар направляется в конденсатор — теплообменник, служащий для превращения пара в воду. Пар необходимо превратить в воду, чтобы его было легче сжать и отправить обратно в котлы, начиная паросиловой цикл заново.
Наша ТЭЦ снаружи
Наша ТЭЦ изнутри
Конденсатор
Конденсатор ТГ — это примерно 5 тысяч тонких металлических трубок в коробке размером с автомобиль, внутри которых течёт холодная вода циркуляционного контура, а между ними охлаждается пар, превращаясь в конденсат.
Трубный пучок конденсатора
Повторим, между трубками проходит пар, который, охлаждаясь, конденсируется, превращаясь в воду, называемую основной конденсат. Внутри же трубок, наоборот, происходит нагрев циркуляционной воды. А кто же охладит эту воду, спросите вы? На ТЭЦ для это есть свой циркуляционный контур, в котором охлаждение нагретой после конденсаторов воды происходит в градирнях при помощи воздуха. Основная задача конденсатора — превратить весь подаваемый в него пар в конденсат. Превращение пара в конденсат сопровождается его сжатием, т. е. уменьшением объёма.
Напомним, что конденсатор — это закрытый сосуд, не сообщающийся с воздухом. Поэтому при уменьшении объёма пара в этом сосуде создаётся разрежение, т.е. давление меньше атмосферного, его называют вакуум. Чем больше разница между давлением в конденсаторе и атмосферным давлением, тем больше вакуум.
А как выгодно работать для турбины, чтобы вакуум был больше или меньше? Ответ: для более эффективной работы турбины нужно иметь больший вакуум. А как получить больший вакуум? Ответ: нужно обеспечить большую скорость превращения пара в конденсат. Соответственно, вопрос, как это сделать. Ответ: нужно либо подавать меньше пара, чтобы он успевал конденсироваться, либо обеспечить оптимальные условия охлаждения. А что за условия охлаждения? Это максимальный расход охлаждающей воды и чистый конденсатор. А от этого зависит и эффективность турбины, и количество электроэнергии, которую она сможет выработать.
Т. е. поддерживать конденсатор в чистоте выгодно. Но сделать это, особенно летом, нелегко, ведь для чистки нужна остановка или разгрузка ТГ, а это всегда потеря в выработке электроэнергии.
При этом по ходу движения пара внутри турбины его отбирают на различные нужды (производственные и отопительные). На производственные его отбирают ещё с большим потенциалом, когда он прошёл только треть турбины. А вот на отопление пар отбирают практически перед конденсатором. В таком случае с этого пара и электроэнергии можем почти столько же получить и конденсатор не загрузить. Однако здесь есть несостыковка. Такой манёвр актуален для лета, когда охлаждать циркуляционную воду в градирнях тяжело. А летом, как известно, отопление никому не нужно. Вот и получается, что универсальным способом одновременного увеличения выработки ЭЭ на турбине и повышения её эффективности является поддержание чистоты трубок конденсатора.
Конденсатор загрязняется самыми разными вещами: чаще всего это песок, ил, ракушки. Попадают эти объекты в цикл через окна градирен и с подпиточной водой.
Примерно один раз в четыре месяца конденсатор нужно чистить. Есть два варианта чистки: с остановкой турбины и без. Вариант с остановкой применяется при плановых ремонтах или сильной степени загрязнения. После останова производится механическая очистка. Более нестандартным вариантом очистки конденсатора является его очистка «на ходу». Для этого мы останавливаем его половину, разбираем и моем каждую трубку. Затем собираем всё обратно, подаём воду в очищенную часть, проделываем всё то же самое со второй половиной. Такой способ позволяет меньше терять выработку.
Чистки
На графике описан процесс получения прибыли от работы турбогенератора. После проведения чистки конденсатор линейно ухудшает свои показатели, а, соответственно, себестоимость генерации растёт.
В какой-то момент мы выводим его на чистку, и тогда прибыль отрицательная (мы не генерируем и платим подрядчику за чистку). Дальше нужно определить самую большую площадь под графиком и решить простую оптимизационную задачу.
Это даст нам теоретическое представление о том, когда его чистить. То есть чистить его слишком рано смысла нет, мы просто просядем по генерации на время чистки (вплоть до нуля, если речь идёт о полном останове). Чистить его слишком поздно тоже дороговато, т.к. себестоимость генерации будет слишком высока. Нужно чистить точно вовремя.
Раньше его чистили либо по графику планово-предупредительных ремонтов, которые были подвязаны под ремонт смежного оборудования, количество часов наработки оборудования и сезонность, либо при видимом ухудшении показателей. Но всё же самая главная цель цифрового подсказчика — это выбор оптимального времени для чистки конденсатора с точностью до суток. Издалека, возможно, эта задача и кажется очень простой, но на практике вышло наоборот.
Матмодель
Первое, что приходит в голову, — это ориентироваться на расход циркуляционной воды по половинам конденсатора. Чем меньше он номинального, тем больше загрязнение и забивание трубной системы. Самой большой проблемой здесь было банальное отсутствие расходомерных устройств на циркуляционных водоводах. Конструкция подводящих и отводящих трубопроводов не имеет требуемых длин прямых участков для установки этих самых шайб.
Как же можно выйти из такой ситуации? Справились с этой задачей через вычисление расхода циркуляционной воды через тепловой баланс конденсатора. Но и здесь есть свои подводные камни. Для турбогенераторов с теплофикационным и производственным отбором приходится вычислять количество пара, идущее в конденсатор, через материальный баланс турбогенератора, в котором также участвует множество точек измерения расходов различных потоков. Это неизбежно влияет на точность показаний при вычислении расхода циркуляционной воды.
Приняли решение, что пусть точность такая, какая получается, просто добавим другие индикаторы загрязнения конденсатора, которые будут вычисляться исходя из показаний различных комбинаций датчиков. Например, добавили вычисление коэффициента теплопередачи, температурного напора и нагрева в конденсаторе, а также величину вакуума. Затем добавили в список индикаторов такой, можно сказать, макропараметр, как удельный расход тепла на выработку электрической энергии турбогенератора (сколько пара нужно на выработку киловатт-часа).
Естественно, для каждого индикатора подбирался свой ориентир. Если для расхода циркуляционной воды это был номинал, то, например, для коэффициента теплопередачи это был теоретический коэффициент, а для удельного расхода тепла на выработку — величина этого показателя после чистки. В итоге сейчас мы используем формулу, в которой привязываем расход пара к себестоимости, дифференцируем зависимость, приравниваем к нулю, получаем экстремум, чистим в нём.
Остальные индикаторы служат для подтверждения вердикта основной формулы. Например, видим снижение коэффициента теплопередачи — подтверждение загрязнения поверхности теплообмена, видим снижение расхода охлаждающей воды — подтверждение засорения трубной системы конденсатора по циркуляционной воде.
Теперь коротко про то, почему не могли решить до этого. К нам приезжали разные интеграторы, даже было предложение от одного института. Однако при ведении дел с ними не покидало такое чувство, что они ни разу не видели конденсатор вживую. Первые несколько предложений были уровня «давайте возьмём теоретическую модель физических процессов и будем сравнивать с ней» или «давайте на режимные карты наложим факт и попробуем понять разницу».
Все эти методы подходили, но отличались сложностью создания и поддержания моделей при их низкой точности в условиях нашего набора измерительных устройств: скорее всего, мы бы их положили в стол, потому что, даже если бы там было обучение (или численное приближение по мере накопления данных), «дотачивание» заняло бы пару лет.
А я как раз занимался в бакалавриате и магистратуре оптимизацией котлов, а на должность инженера вышел как инженер ТЭЦ по эффективному использованию энергоресурсов. Первую модель котла я считал в Excel с макросами, но его не хватало. Вторую делал уже в Mathcad, а потом понадобилось кое-что доуточнить. Там я уже начал учить Java (сейчас понимаю, что это был путь немного не туда), но задачу выполнил. Здесь получилось посчитать всё нужное — и сейчас уже в ИТ-команде я моделирую с помощью Python.
Так что я тут оказался последовательно в двух ролях: сначала производственником, не доверяющим офисным айтишникам, потому что они никогда живого агрегата не видели, а затем уже айтишником, но уже понимающим ограничения системы, накладываемые реальным миром. Да чего уж там «понимающим» — можно сказать, самым что ни на есть испытавшим на своём проекте сложности производственных условий.
Автор: sigaev_kirill