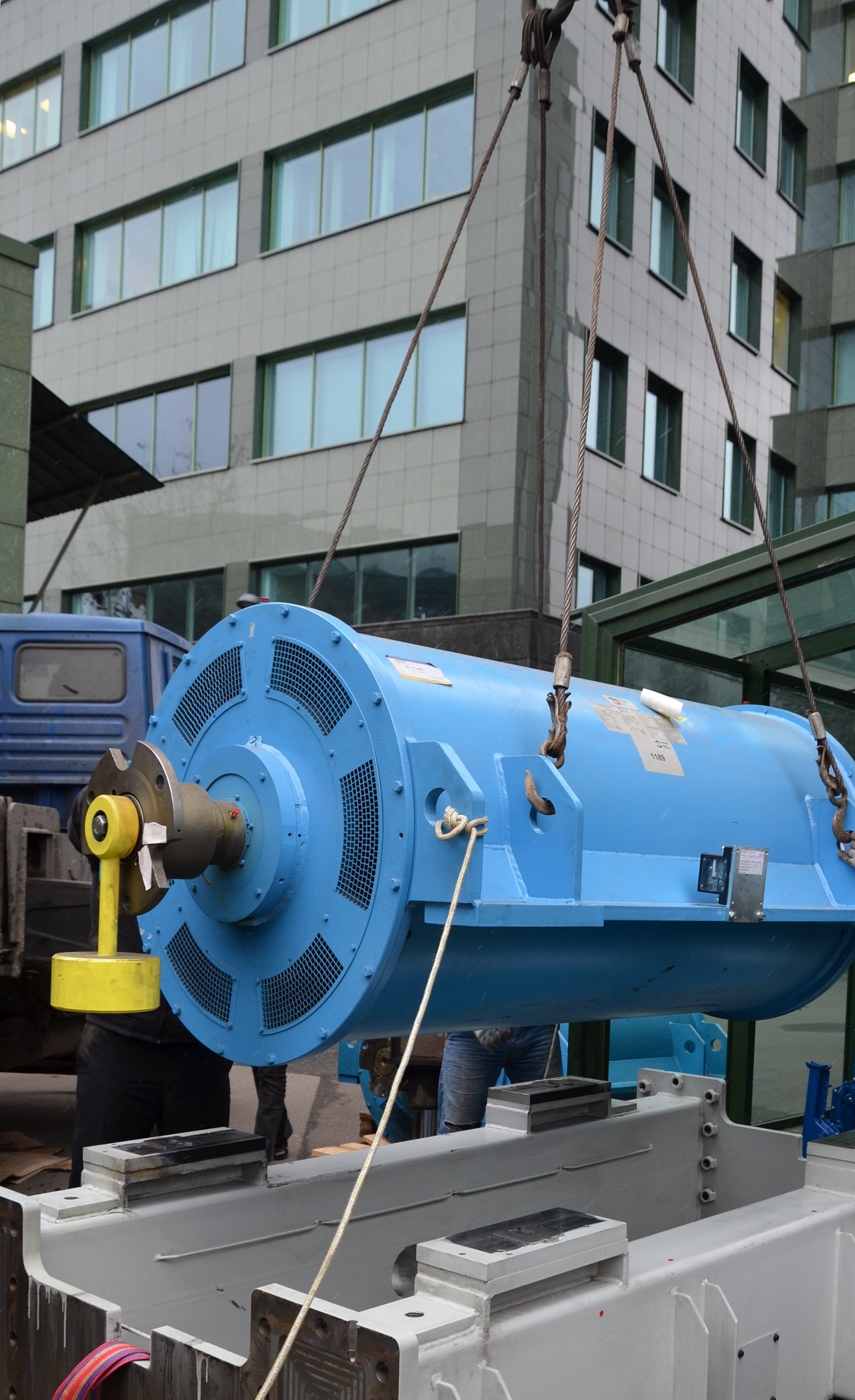
Это такой здоровенный волчок-ротор, стоящий в разрыве электрической цепи на входе в дата-центр. Он постоянно крутится. Если отключают питание, то он по инерции обеспечивает беспрерывность питания до запуска дизеля. Питание без переключения снова восстанавливается. У нас там выработались подшипники, и мы решили их немного поменять.
Современная практика такова, что здания строятся с учётом того, что там будет резерв в части энергоснабжения, в нашем случае это ДДИБП. Здание подземного дата-центра у нас уже было, и поэтому замена проходила очень увлекательно.
Вот, например, задача на знание физики.
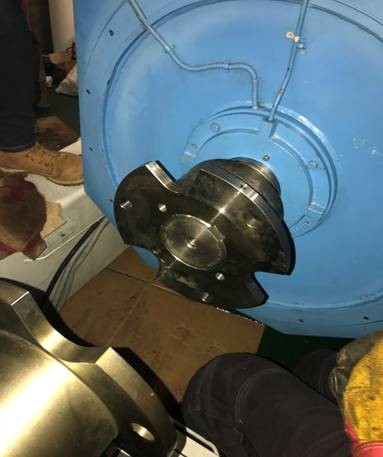
Здесь на вал посажена соединительная муфта. Она прилегает к валу настолько плотно, что снять его нет никакой возможности.
Мы позвали специального мужика с чёрным поясом по сварке, задача которого была ОЧЕНЬ БЫСТРО разогреть эту муфту. Было важно, чтобы муфта нагрелась как можно сильнее, при этом вал оставался холодным, и поэтому для лучшего контроля мы наблюдали за этим процессом через тепловизор. Параллельно тепловым работам между валом и муфтой прикладывалось усилие гидравлическим 10-тонным прессом, и в какой-то момент у нас получилось «сдернуть» и впоследствии снять эту муфту. Обратно ставить муфту было гораздо проще. Мы постепенно её разогрели до 200 °С и надели на вал.
В общем, лучше я расскажу сначала про работу людей, обслуживающих эти ваши хрупкие процессоры в дата-центрах.
Сначала общий вид установки:
История началась просто: проводилось стандартное техобслуживание, в рамках которого проводился вибротест в контрольных точках. Поняли, что вибрация превышает нормы. По рекомендации Хайтека решили менять модуль накопителя на одной из установок. Для нас это важно и критично — мы даже обучили бойцов кое-чему и закупили дополнительное оборудование. Мы мерили всё. Видели, как машина приближается к тому уровню, когда надо менять подшипники.
Вибрации сигнализируют, что основной расходник (подшипники) изнашивается. Видим, что подшипники скоро надо будет менять, и инициируем эти работы. Пошли разговаривать к Хайтеку. Вендор говорит: мужики, кто-то что-то не так понял, но поменять подшипники на месте технически невозможно. Для этого нужны космические технологии. Связано это всё с разбором ротора. Нужна точная подъёмная штука — надо ротор продвинуть по узкому каналу, ничего не задев. Делается такое только на заводе. Говорят, единственный вариант пройти замену — это целиком поменять модуль.
Мы очень обрадовались.
Если у нас и были ночные кошмары в обслуживании дата-центра, то замена центрального модуля ДДИБП стояла на втором месте. На первом было землетрясение с последующим засыпанием машзала землёй. Землетрясений в Москве обычно нет.
Дело в том, что модуль стоит посередине. Вся машина в сумме 20 тонн. Из них 2 модуля по краям примерно по 7 тонн (дизель и генератор). В центре — накопитель. В накопителе — подшипники. Его нужно вытащить, как морковку из грядки, и поставить другой такой же. Условия стеснённые — не то слово. Как я говорил, обычно здания строят под такие машины, а мы затаскивали в уже имеющееся.
Проектировщики ещё тогда сказали, что обслуживание в теории возможно.
Тогда мы услышали только «возможно», но не «в теории». Теперь нам предстояло устранить вот этот маленький разрыв между реальностью и абстракцией.
Итог — надо жонглировать железяками по 5 и 7 тонн. И не поломать их и стены. Если будет выбор, что ломать, стену или железку, — лучше стену. Подъёмные механизмы не помещаются никак. Вот наша штуковина со схемой, где видно части:
Процесс по шагам:
1. Демонтаж двух установок накопителя и генератора.
2. Вывоз, такелаж, погрузка старого.
3. Такелаж нового на новое посадочное.
4. Соединение с двигателем, установка муфты, центровка вала, подключение к генератору и то же самое.
Ну, поехали
Вот мы с интересом таскаем старый накопитель. Положили его в специально сконструированную «колыбель», начали возить как машинку на верёвочке. Пока двигали по горизонтали, всё шло хорошо. Была проблема вот с этим углом, там повозились знатно:
Дальше подъём 15%. Тащили лебёдкой, усилие на лебёдке — 1 тонна:
Дальше приехал грузовик, мы с помощью крана погрузили модуль в него:
Потом приехал новый. Его надо было поставить на ту же «колыбель» и закрепить. Закрепить важно: нам нельзя уже будет его крутить в помещении, поэтому нужно было попасть точно так, как надо. Смотрите, как мы весело попадали краном:
6-тонной хреновиной надо попасть точно в отверстие в площадке. Резьба ровно под винт, никаких плюс-минус миллиметр. Это потому, что нужна довольно высокая точность уже внизу, в момент соединения.
Если вы думаете, что в век роботов и больших данных очень легко решить такую задачу, то глубоко ошибаетесь. Крановщик не робот, а махание 6-тонным грузом на длинном подвесе никак не автоматизируется. В общем, с помощью физической силы и какой-то матери мы это сделали. Не так быстро, как хотели, и не без новых длинных слов, но сделали.
Кстати, оцените, какая серьга была:
Дальше повезли всё назад:
Вот электромагнетический датчик наклона (шок-логер). Погрузка-разгрузка: максимально допустимая встряска — 8g, поэтому кран мы выбирали, чтобы был с плавным пуском:
Вот помещение без генератора и накопителя. Сюда нужно притащить модуль, поставить его точно по центру (все три модуля соединяются одним валом) и всё снова подключить:
Вот, значит, мы греем подшипник и наблюдаем за процессом через тепловизор:
До 200 градусов грели, потом в специальных перчатках ставили. На некоторое время у нас там случился ад. Пожарные стояли рядом, ждали, что всё загорится, но мы их очень разочаровали.
Вал идеально шлифованный, поэтому мы его всё время покрывали ветошью, чтобы не поцарапать. Кожух вообще-то тоже цепляется в заводских условиях, но Виталий (инженер со стороны вендора Хайтек) — такой гуру, что сделал всё голыми руками.
По сложности это как набить морду Чаку Норрису. Потому что очень сложно голыми руками правильно отцентровать 250-килограммовую деталь.
Конечно, центровка вала в итоге получилась грубая. Для работы машины нужно, чтобы она была идеальной. Поэтому после сборки другая команда (в чистой одежде, без сгоревших бровей, полная сил и довольная жизнью) при помощи ротеллинга (специнструмента) доделывала всё на пусконаладке. В итоге три части машины по соосности идеально совпали.
Подводка и расключение:
На расключении важно замерить сопротивление изоляции и убедиться в его достаточности. Сейчас 550 МОм, более чем достаточно. Пыли много, она забивается — в нашей практике в другом дата-центре было почти до пробоя на одной из машин.
А вот видно и щётки:
Тут замер сопротивления на токосъёмном механизме. Есть бесщёточное исполнение, но у нас традиционное. Машину со щётками легче диагностировать и прогнозировать. К токосъёмному кольцу прижимаются графитовые щётки, потому что графит — проводник и при этом мягкий, то есть не царапает вращающееся контактное кольцо. В работе щётка должна всей своей площадью поперечного сечения прижиматься к токосъёмному кольцу, и в дальнейшем на контактном кольце образуется тёмный слой, так называемая патина. Слой патины уменьшает трение щётки о поверхность контактного кольца, что увеличивает срок её службы.
Результат:
Вот, собственно, всё.
Ссылки
- Монтаж
- ДДИБП Хайтека нового поколения
- Моя почта: PGoryunov@croc.ru.
Автор: Pavel_Goryunov