Привет, меня зовут Миша. Я инженер по качеству в компании ГРАН Груп. Мы производим печатные платы, в том числе для оборудования, где один сбой стоит жизни: для кардиостимуляторов, аппаратов ИВЛ, систем управления поездами, самолётов и ракет. В статье я рассказываю, какие ошибки клиента стоят больших денег и ваших жизней, про боль госпредприятий и как мы проверяем качество платы.
ДИСКЛЕЙМЕР: я намеренно упростил описание процессов, чтобы статья была понятна всем читателям.
Мы работаем в двух странах: России и Китае. В России мы общаемся с клиентами, подготавливаем их проекты к производству, выбираем производственную площадку. У нас есть надёжные партнёры среди производств в Китае. Каждое производство специализируется на определённых типах электроники. Это помогает нам выбрать лучшее производство для каждого проекта. Например, серверные платы мы делаем на производствах, которые специализируются на серверном оборудовании. Автомобильную электронику производим там, где есть нужные сертификаты. Мы вовлечены во все этапы производства: от контроля качества до логистики.
В Китае у нас есть еще один отдел качества. Там тоже работают наши люди, но местные. Раньше производством и отделом качества управлял россиянин, но из-за языка и культурных различий все решалось медленно. Особенно срочные вопросы, например, если груз застрял на таможне или нужно срочно сделать партию. Сейчас же контроль на нашем сотруднике-китайце: достаточно пары фраз с коллегами на своем языке — и дело сделано.

Мы не проектируем платы с нуля — к нам приходят клиенты уже с готовым проектом. Но мы умеем реализовывать эти проекты в односторонние, двусторонние и многослойные платы, гибкие, полугибкие, гибко-жёсткие и прочие.
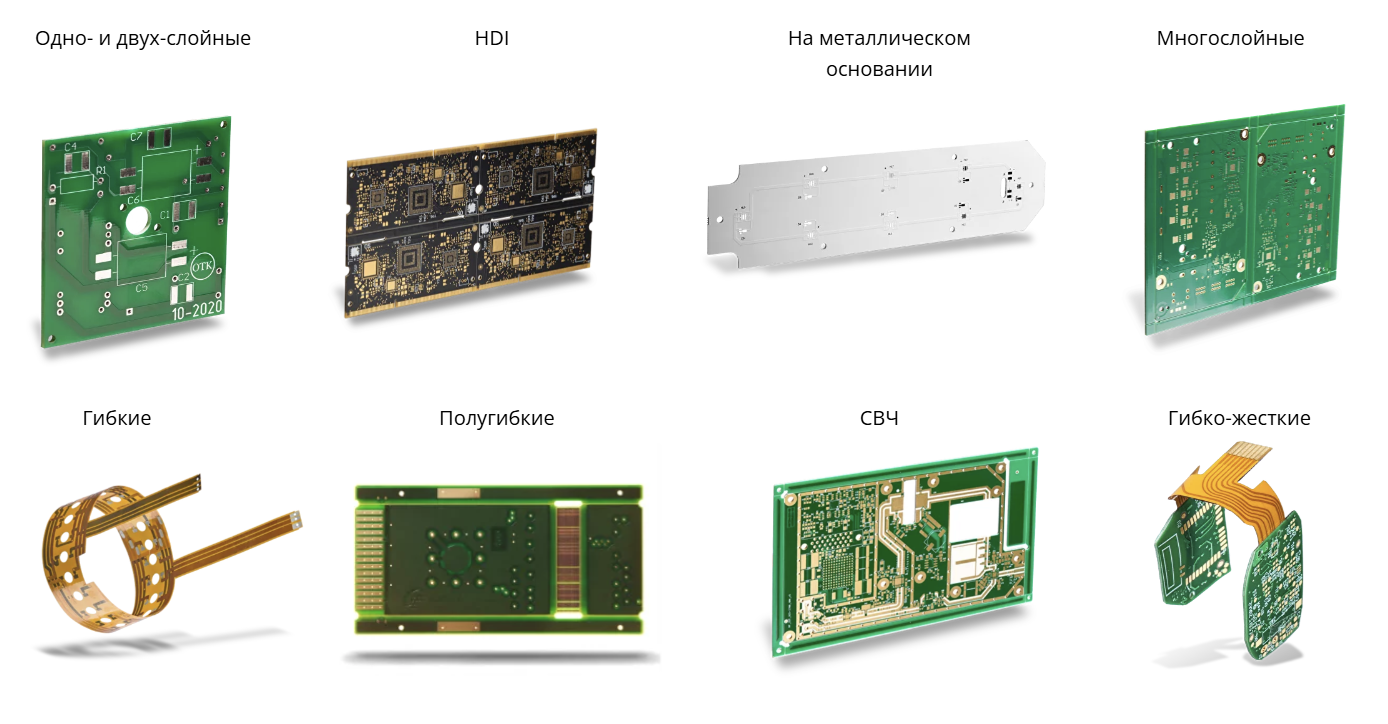
Недавно у нас выходила статья, как мы изготавливаем платы. Поэтому на производстве останавливаться я не буду. Но я расскажу, как мы контролируем процесс до, во время и после производства.
Контроль проекта печатной платы до производства
В большинстве случаев стоимость платы составляет всего 2% от стоимости всего устройства, но именно плата играет большую роль в работоспособности устройства.
Это как с фундаментом дома: на него уходит мало денег, но от него зависит прочность всего здания.
Брак на готовой плате сложно заметить сразу. Потому что такая плата может работать без сбоев какое-то время, а потом подвести в самый важный момент. Например, ракета успешно пройдёт все проверки на Земле, но как только она окажется в космосе — она выйдет из строя. Поэтому мы внимательно проверяем все проекты еще до производства, выполняя технологическую подготовку.
Сначала клиент нам присылает бланк заказа и Gerber-файлы. В бланке он указывает параметры платы: тип, используемые материалы, размеры, толщину, стандарты и другие параметры. Gerber — это универсальный файловый формат передачи данных в нашей сфере. В таких файлах разработчик печатной платы указывает расположение и размеры всех элементов платы на каждом слое.

Мы проверяем эти файлы еще в России и часто находим в них ошибки. Например, в бланке заказа клиент просит гибко-жесткую плату, а в Gerber-файлах указывает гибкую плату с усилением. Такая ошибка влияет на конечную стоимость.
Еще пример частой ошибки: разработчик располагает дорожки слишком близко к краю платы. А это может привести к оголению меди, ее задирам и нарушению целостности проводников при обработке контура. В итоге печатная плата уйдет в брак.

Когда в проекте есть ошибки, мы связываемся с клиентом. Объясняем ему какие изменения нужны и почему, согласовываем каждую правку.
Уточняем стандарты
Мы делаем платы по двум стандартам: IPC и нашему внутреннему. IPC — это стандарт, по которому работает весь мир. В нём есть чёткие требования к материалам, процессам проектирования и производства и контролю качества печатных плат.
Наш стандарт — это 20 дополнительных требований, которых нет в IPC. Например, в IPC не прописана толщина паяльной маски. А это очень важно. Тонкая маска может отслаиваться от платы, возрастает риск при сборке, толстая — препятствовать пайке. Поэтому в нашем стандарте мы пишем: "На углу проводника маска должна быть не менее 5 микрон". Этот стандарт мы отправляем всем заводам, которые делают наши печатные платы. Или средняя толщина металлизации стенок переходных отверстий: везде она 20 мкм, у нас – 25 мкм.


Но некоторые российские госпредприятия обязаны проектировать платы по третьему стандарту — ГОСТам. А в России есть два типа ГОСТов: советские и современные. Если разработчик печатной платы использует требования советских ГОСТов для отправки напрямую в Китай, то у компании возникают проблемы. Потому что китайские производства уже давно не принимают заказы с такими требованиями и работают только по IPC.
Например, советский ГОСТ предлагает деление на четыре класса жесткости. Эти классы соответствуют “жесткости” условий эксплуатации. Современный российский ГОСТ, как и международный стандарт IPC, предлагает классификацию по требованиям к надежности изделий: класс 1 – электроника бытового назначения, класс 2 – промышленная электроника и класс 3 – электроника высокого уровня надежности.
Современные российские ГОСТы близки к IPC. Тем не менее для производства нужно определять все параметры в соответствии со стандартами IPC. Мы помогаем это сделать.

Технологическая подготовка помогает нам сразу назвать точную цену и срок, а заказчику — получить именно ту плату, которая нужна для его устройства. Когда всё выяснили, файлы идут в производство.
Как мы проверяем платы на производстве
Одни виды проверок мы проводим еще на этапе заготовок, когда сама плата еще не готова, другие делаем на тестовых образцах всей партии. Начнем с проверки заготовок.
Проверяем «голый» медный рисунок на каждом слое
Немного о производстве: вначале мы делаем заготовку — слои для платы. Мы забираем материал со своего склада, нарезаем его и проводим базовые операции: наносим фоторезист, экспонируем через фотошаблон и стравливаем медь. В итоге на каждом слое будущей платы получается медный рисунок.

Этот рисунок мы проверяем ещё до того, как прессуем слои и наносим защитную маску, — если есть дефект, то обнаружим его сразу.
Оператор загружает в машину заготовку. Машина сканирует медный рисунок и сравнивает его с эталоном нужного слоя.

Система показывает все отклонения на экране оператора: неправильно протравленную медь, замыкания, обрывы, нарушения в ширине дорожек и зазоров между ними.
Некоторые дефекты мы можем исправить. Если медь неправильно стравилась или есть замыкания, мы механически подрезаем её. Но только до нанесения паяльной маски.
А вот если мы находим обрыв проводника — это сразу брак. Хотя стандарт IPC в некоторых случаях разрешает ремонт таких мест, мы этого никогда не делаем. У нас более строгие внутренние требования, потому что от наших плат может зависеть жизнь людей. А подобный ремонт изменяет сопротивление проводника, из-за чего нарушается целостность сигнала и оборудование может дать сбой.


Затем из тех заготовок, что прошли проверку, мы собираем плату: прессуем слои, сверлим отверстия, наращиваем медь и формируем внешние слои. В конце мы наносим паяльную маску, финишное покрытие и шелкографию. После этого мы отправляем готовую плату на электроконтроль.

Проверяем целостность цепей
Когда печатная плата готова, мы её отправляем на электроконтроль. Здесь мы проверяем, нет ли в цепях замыканий или обрывов.
Небольшую партию мы проверяем по методу "летающих щупов". Два автоматических манипулятора с иголками проверяют каждую цепь по очереди, пропуская через нее ток. Это занимает от 1 до 5 мин, в зависимости от количества цепей и слоев платы, но зато не требует сложной подготовки.

Для больших партий мы сначала вручную делаем два адаптера — металлические пластины с иглами. Иголки мы размещаем там, где нужно проверить сигналы на плате.

Потом мы крепим адаптеры на робота. Робот зажимает между ними плату, и все иголки одновременно касаются нужных точек. Проверка получается быстрая — 1-2 секунд на проверку всех цепей у одной платы.

Если есть брак — робот передаёт эту информацию человеку, где он анализируют причину, а потом отправляет плату на переработку.
Стресс-тесты и измерения плат в лаборатории
На этом этапе мы выбираем несколько образцов из партии и отправляем их в лабораторию.
Погружаем плату в припой 288 градусов
Наш заказчик будет выполнять пайку электронных компонентов. А значит, нам важно убедиться в хорошей смачиваемости покрытия.
Смачивание – это тот процесс в пайке, когда припой входит в прямой контакт с финишным покрытием, образуя единое соединение сплава металлов.
Для этого оператор помещает плату на 2 секунды в ванну с припоем. Система измеряет силу смачивания и показывает её на графике — чем выше линия, тем лучше будет проходить процесс пайки. После этого оператор под микроскопом проверяет, полностью ли припой покрыл контактные площадки.

Резко нагреваем
При монтаже компонентов печатная плата испытает сильный термоудар — быстро нагреется почти до 300 градусов. Если процессы металлизации и прессования были выполнены с отклонениями от технологии, то риск потери платой структурной целостности (появление расслоений, разрывов стенок переходных отверстий и т.п.) очень высок.
Чтобы убедиться, что этого не случится, мы проводим термостресс-тест. Оператор погружает плату в ту же ванну с припоем, что и при проверке паяемости. Но теперь он делает так 3 раза по 10 секунд. Это очень жёсткие условия. Если печатная плата расслоилась, появились микротрещины или отошли медные проводники — это говорит о нарушениях в процессе металлизации или прессования. Такая плата не выдержит пайку компонентов.

Обклеиваем плату клейкой лентой
Паяльная маска должна прочно держаться на плате. Поэтому мы проверяем её на прочность.
Оператор наклеивает клейкую ленту на паяльную маску и резко отрывает под углом 90 градусов. Если маска осталась на месте и не повредилась — значит, она надёжно защитит плату от влаги, пыли и механических повреждений.

Царапаем плату карандашом
Паяльная маска должна быть достаточно твёрдой, чтобы защищать плату. Твердость мы проверяем с помощью обычных карандашей.
Оператор берёт карандаши разной твёрдости и чертит ими по маске. Он начинает с мягких и постепенно берёт всё более твёрдые, пока не появится царапина. По нашим требованиям, только карандаш твёрже 5H может оставить след на маске.

Погружаем плату в воду
При производстве печатная плата проходит через разные химические растворы. Хотя мы её и отмываем, на поверхности всё равно остаются ионные загрязнения. Это опасно: загрязнения могут привести к коррозии проводников, потере сопротивления изоляции и помешать пайке компонентов.
Поэтому мы делаем отмывку и проверяем чистоту платы. Оператор помещает плату в ванну с дистиллированной водой на 15 минут. За это время загрязнения растворяются в воде.
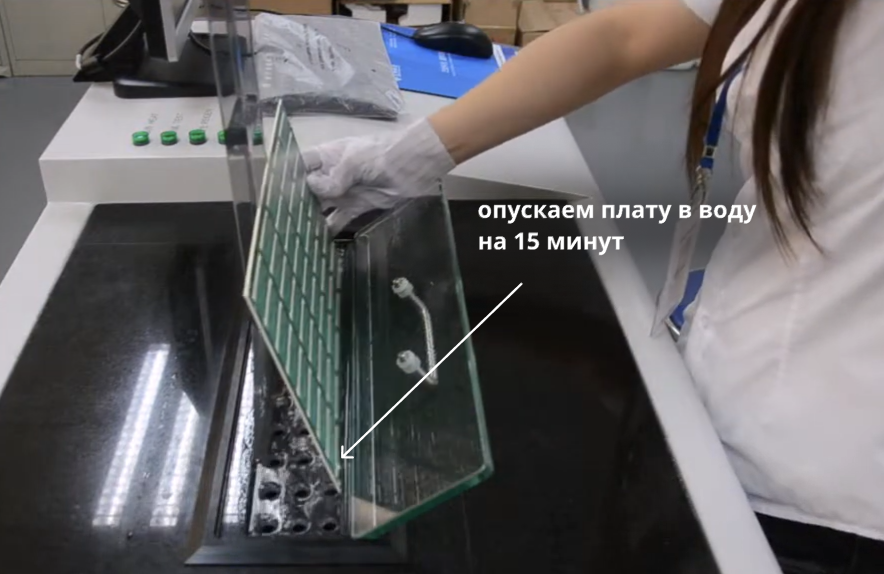
Затем оператор измеряет проводимость воды. Если проводимость меньше 0,8 микрограмм на квадратный сантиметр — печатная плата считается чистой, и мы продолжаем тесты. Если проводимость больше, то мы отправляем партию плат на отмывку.
Контролируем импеданс дорожек
Иногда заказчик просит измерить импеданс — волновое сопротивление проводников. Это важно для плат с дифференциальными парами.

Напрямую на плате импеданс измерить сложно: мешают искажения от соседних проводников и компонентов. Их электрические поля влияют на результат измерения. Поэтому мы используем специальный тест-купон.

Оператор подключает специальные щупы к тест-купонам и измеряет импеданс. Результаты он сразу видит на экране прибора и записывает в протокол испытаний.

Делаем микрошлиф и смотрим его под микроскопом
Чтобы убедиться, что внутри платы тоже нет дефектов, мы рассматриваем плату под микроскопом в разрезе.

Под микроскопом на микрошлифе мы проверяем 42 пункта, например:
-
целостность платы после термоудара;
-
качество заполнения переходных отверстий;
-
толщину паяльной маски: над проводниками, на уголке, над поверхностью базового материала;
-
толщину металлизации в отверстиях (не меньше чем 25 микрон);
-
толщину меди на внешних и внутренних слоях;
-
расстояние между слоями;
-
отсутствие расслоений.

Вместе с партией мы отправляем заказчику микрошлиф и отчёт по нему, как подтверждение качества.
Сверяем реальные размеры с эталонными
Оператор с помощью сканера проверяет размеры пазов, контактных площадок, проводников и зазоров между ними.
Диаметры отверстий под пресс-фиты измеряем автоматически — их размер должен быть выдержан с точностью до микрон. Оператор закрепляет плату на специальной установке (hole measuring machine), и она проверяет каждое отверстие.
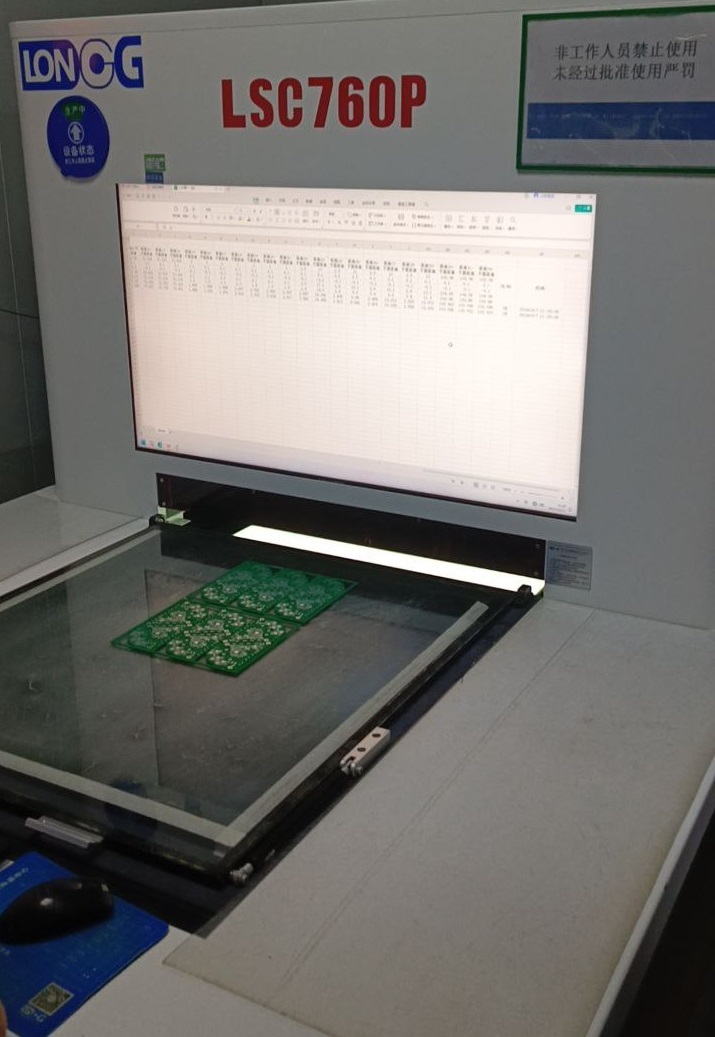
Кроме этого, мы обязательно измеряем изгиб и кручение платы. Такие деформации могут появиться из-за разных причин: нарушения баланса меди на слоях, отклонений при прессовании или несимметричной структуры. Важно, чтобы отклонения, если они есть, не выходили за пределы нормы.

Сравниваем готовую плату с золотым образцом
Когда образцы прошли все тесты, мы пересчитываем платы в партии и проверяем их на видимые дефекты: проблемы с маской, покрытием, маркировкой, царапины и повреждения.
Контролёр проверяет маленькие партии вручную под микроскопом. Для больших партий он использует систему автоматической визуальной инспекции (AVI).

Результат проверки контролёр видит на экране.

Если система находит дефект, она показывает их оператору на экране и откладывает платы на проверку. Оператор передаёт эти платы с данными в отдел качества, где уже более опытные сотрудники будут решать, что делать с платой дальше, — утилизировать или оставить.

Как мы следим за готовой платой, чтобы она не испортилась
Затем упаковщик кладёт платы на герметичную плёнку и отправляет в термоусадочную машину. Она создаёт мягкий вакуум и запаивает плёнку. Получается упаковка из 16 стопок.

Упаковщик разрезает упаковку на отдельные стопки, каждую помещает во влагозащитный пакет и клеит этикетку с информацией о плате.

Затем он укладывает стопки в картонную коробку и отправляет на склад.

К каждой партии мы прикладываем отчет — Сертификат соответствия (CoC – Certificate of compliance). В нем мы указываем все результаты проверок, числовые показатели и графики. Независимо от того производства, где платы были произведены, форма такого сертификата всегда едина.

В Россию мы отправляем грузы железной дорогой или самолётом. ЖД дешевле, но это для клиентов, которые планируют производство за 3 месяца вперед.
Спасибо, что прочитали. Если вы интересуетесь электроникой, то подписывайтесь на наш блог на Хабр. Мы любим своё дело и с удовольствием будем делиться любопытными внутренними процессами. А если вам нужны печатные платы, которые не выходят из строя, отправляйте нам свои проекты.
А ещё мы с коллегами ведём телеграм-канал. Там мы рассказываем все о производстве печатных плат, проверке качества и особенностях логистики из Китая в Россию, делаем анонсы онлайн и офлайн мероприятий и многое другое. Подписывайтесь, будет интересно.
Автор: shvedov_grangroup