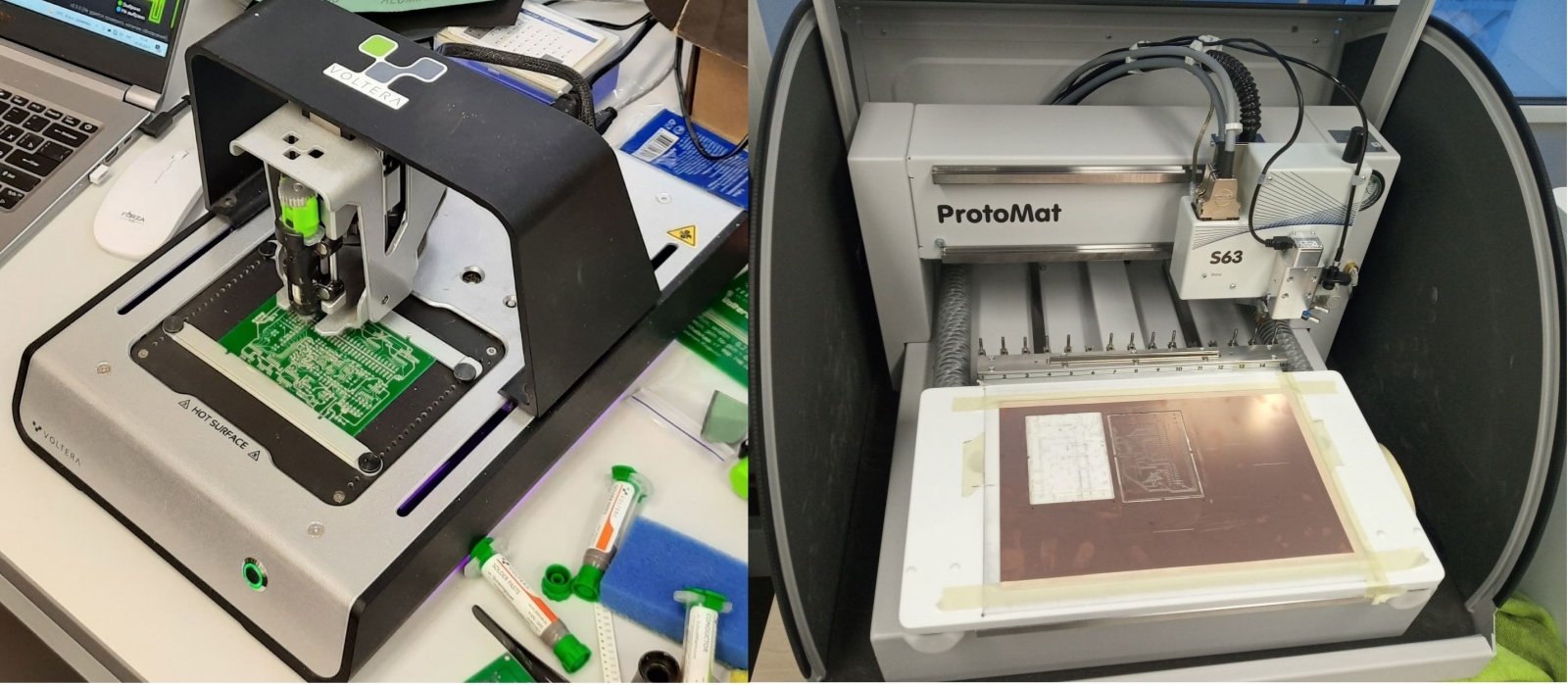
Наверняка каждый радиолюбитель сталкивался с необходимостью самостоятельно изготавливать печатную плату, ведь не всегда целесообразно оплачивать и ждать заказ из Китая. И наверняка держа в руках утюг, вы задавались вопросом: «а как-же обстоит дело с прототипированием печатных плат у профи, наверняка же у них есть какой-то волшебный прибор для этих целей?». Только представьте, нажал кнопку и без лишнего шума и пыли получил готовую печатную плату! И такие способы есть! Но в каждой бочке мёда есть своя ложка дёгтя.
В этой статье не будет переводов или информации из рекламных проспектов, будет только мой личный опыт изготовления печатных плат для прототипирования электроники на 3х осевом ЧПУ LPKF ProtoMat S63 и специализированном принтере Voltera V-One.
Введение
Как вы знаете, существует два основных метода изготовления печатных плат: аддитивный и субтрактивный.
Субтрактивный метод предполагает формирование токопроводящего рисунка путем удаление лишней меди с пробельных мест. Этот способ наиболее знаком радиолюбителям. С помощью «лазерного утюга» или пленочного фоторезиста наносится защитный рисунок, затем травим плату в хлорном железе или чем-то подобном. Также возможно удаление лишней фольги путем фрезерования. Для этих целей радиолюбители с помощью бубна используют обычные чпу.
Аддитивные методы не предполагают использование медной фольги, токопроводящий рисунок как правило, наращивается электрохимическими методами. В радиолюбительской практике встречались попытки с токопроводящим клеем, но реально рабочей технологии я лично не встречал.
Для реализации обоих методов существует специализированное оборудование, о представителях которого далее и пойдёт речь.
Voltera V-One
Voltera V-One позиционируется как 3D принтер для полного цикла создания двухсторонних печатных плат и их сборки.
Технология очень заманчивая. Тем более, на тестовом образце все выглядит ну очень нарядно. В работе принтер выглядит просто завораживающе!
Изготовление платы включает в себя следующие этапы.
1. С помощью специализированного ПО обрабатываем гербер файлы печатной платы для управления принтером. ПО, к слову сказать, очень неплохое, ни чего общего не имеет с колдовством в ArtCAM и MACH3, если вы понимаете о чем я…
2. Устанавливаем в принтер заготовку из стеклотекстолита или иную подложку, заранее ее обезжирив и придав шероховатость с помощью мелкой наждачки. Подложка не имеет фольгированного слоя, т.к. проводники будут распечатаны. Производим калибровку принтера.
3. На принтер устанавливается шпиндель со сверлом, и он сам сверлит отверстия. Очень удобная опция, сверлить текстолит я не очень люблю.
4. Устанавливаем головку для печати с тюбиком спец пасты. И принтер распечатывает токопроводящий рисунок. Переворачиваем плату, калибруем принтер, и печатаем вторую сторону. Затем паста оплавляется нижним подогревом принтера. Получаем готовые печатные проводники в металле.
5. Меняем тюбик на паяльную пасту. Принтер наносит пасту на контактные площадки. Расставляем электронные компоненты. Включаем подогрев, паста оплавляется, компоненты припаиваются.
6. С помощью специальной оснастки запрессовываем медные гильзы в переходные отверстия. И собственно плата полностью готова. Остается только руками распаять выводные компоненты.
Согласитесь, идеальный план, это просто мечта для любого электронщика! Но а как же обстоит на деле?! А вот тут начинается просто бочка дегтя. На фотографии показан лучший результат, который смогли получить за день танцев с бубном.
Нормально откалибровать сопло экструдера так и не получилось, что только не делали. Добиться достаточной подачи пасты тоже не получилось, этот параметр настраивается и определяется скоростью выдавливания. Также оказалось достаточно сложно совместить отверстия с рисунком проводников. На следующем фото видно, что отверстия немного гуляют, где-то более-менее попадают по центру, а где-то совсем не попадают.
Про идею с гильзами для переходных отверстий я, пожалуй, просто не буду комментировать. Сами все видите. Только скажу, что каждый переход надо обязательно прозванивать.
Еще одна проблема связана с самим секретным составом печатных проводников. Как видно на картинках, паяльная паста при оплавлении не дает достаточного протекания. Замечу, что все расходные материалы были из одной коробки с принтером. Припаять что-то к плате паяльником практически не реально. Особенно если плата какое-то время полежала на воздухе, припой ни в какую к ней не берется.
Может быть нужно было проявить больше упорства и еще пару дней поколдовать с настройками, а может быть что-то с руками не то. Но в итоге я от этой затеи отказался. Дальше выводы делайте сами.
LPKF ProtoMat S63
LPKF ProtoMat S63 позиционируется как машина для изготовления моделей печатных плат. Думаю, что подробно описывать процесс фрезерования плат не имеет смысла, как работают ЧПУ вы и так знаете. Но на некоторых особенностях заострим внимание.
Я проработал с ним уже больше трех лет. И не смотря на ряд конструктивных недочетов и глюков, очень доволен этим станком. Удобное программное обеспечение. Отлично совмещает стороны. Сам подбирает подходящие фрезы и в процессе резки сам их меняет. Позволяет стабильно получать платы по третьему классу. При определенной сноровке можно добиться четвертого класса точности.
К стати, если дооснастить станок специальной оснасткой, то он тоже сможет наносить паяльную пасту. Вот только выпечку сам не сможет.
Если вам будет интересно, про этот станок с его капризами я расскажу отдельно.
Заключение
Конечно «профессиональные методы» — это громко сказано. Ни один из рассмотренных станков не является профессиональным. Но и любительскими их назвать язык не поворачивается.
Voltera V-One очень интересная и привлекательная игрушка. Требует очень сложной настройки. Размер печатной платы совсем небольшой. Проводимость печатных проводников сильно отличается от меди, делать на нем что-то прецизионное или аналоговое можно даже не пытаться, печатная плата будет сильно искажать работу схемы. Мне кажется, что эта технология еще очень сырая, в своей работе я не готов этим пользоваться. Может быть такой принтер неплохо показал бы себя где-то в школьном кружке, чтобы собирать какие-нибудь небольшие шилды к ардуино. Я думаю, что приловчиться к нему и изготавливать небольшие односторонние платы вполне возможно. Обычно цифровые устройства не так требовательны к проводимости печатных проводников. И здорово, что он сам может сразу припаять электронные компоненты… наверное может…
Фрезеровка печатных плат на LPKF ProtoMat S63 — это отличный инструмент для прототипирования. Но тоже требует определенной сноровки. В отличии от обычных ЧПУ, этот станок неплохо оптимизирован под печатные платы. Также программная обработка герберов не занимает времени. У меня изготовление двухсторонней печатной платы с хорошей плотностью до дециметра площадью занимает до двух часов. Это позволяет оттрассировать, изготовить и собрать прототип печатной платы в пределах одного рабочего дня.
Оба этих устройства обладают идентичными недостатками. Стоимость оборудования просто космос. Подходят только оригинальные расходные материалы, которые тоже совсем недешевые. Итоговая стоимость печатной платы выходит дороже, чем заказать на производстве. Но потенциально это все прилично экономит время на проектирование. А как известно, дорога ложка к обеду.
Еще одна особенность прототипирования печатных плат в том, что чертежи требуют серьезной адаптации под технологию изготовления. Самое очевидное — это размеры переходных отверстий. Либо они делаются под гильзу, либо под пайку проволочной перемычки. Это сильно увеличивает наружный диаметр переходного отверстия. И тут либо размер платы придётся увеличивать, либо полностью все перетрассировывать для финальной версии.
Почему не стоит связываться с обычными трех осевыми ЧПУ для изготовления прототипов печатных плат? Ответ прост: при прототипировании мне необходима печатная плата, а не плясать с бубном над станком. Для меня этот вопрос был закрыт больше 15 лет назад, я пытался адаптировать ЧПУ для этих нужд, плюнул и перешел на пленочный фоторезист.
Почему бы не делать печатные платы, как и все нормальные радиолюбители, утюгом или фоторезистом? Тут тоже все просто. На предприятии даже из-за припоев и флюсов с санитарными службами могут возникнуть проблемы. А представьте теперь, что у вас появляется достаточно токсичная химия, которая требует специальных условий работы и утилизации. Это дома можно вылить остатки хлорного железа в унитаз, а юр лицо за это может схлопотать приличный штраф.
Текст вышел достаточно объемный. Если я что-то упустил, задавайте вопросы в комментариях, может быть на какие-то я смогу ответить. Спасибо за внимание!
Автор:
OldFashionedEngineer