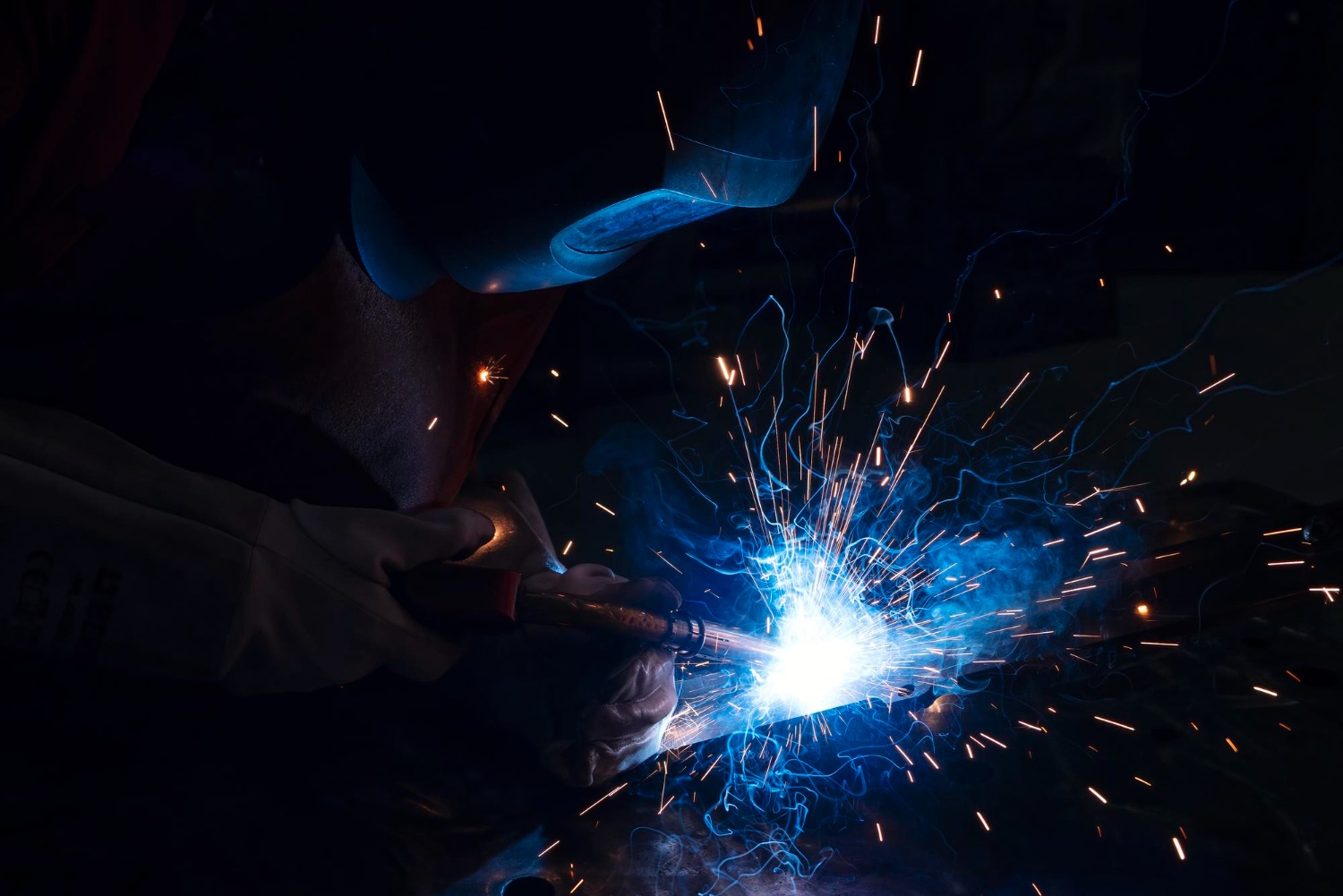
Сварка является одним из уникальных способов соединения металлических деталей. В мировых масштабах объём сварочных работ и получение с их помощью производных изделий растёт быстрее, чем увеличивается производство металла на заводах.
Маленький спойлер: далее речь пойдёт только об инверторных сварочных аппаратах для сварки электродом. Иные виды сварки затрагивать не будем.
Причиной этого является высокая прочность получаемого соединения, которое по своим физическим свойствам практически не уступает изначальному металлу: при соблюдении требований к конкретному техпроцессу прочность соединения может достигать порядка 90% от изначального металла, а при применении специальных приёмов — вплоть до 100%.
Однако получение такого соединения является достаточно сложной технической задачей, так как требуется в маленьком объёме быстро и существенно увеличить температуру до расплавления соединяемых деталей и образования так называемой сварочной ванны. Дело осложняется ещё и тем, что металл обладает высокой теплопроводностью, и из зоны нагрева тепло активно перераспределяется по всему объёму соединяемых деталей.
Для такой сварочной работы используются специальные устройства, способные преобразовывать высокое сетевое напряжение питания в пониженное, применяемое для сварки, и, кроме того, обеспечивающие достаточно высокую силу тока для успешного течения этого процесса.
В последние приблизительно 20 лет (по памяти автора статьи, несмотря на то, что производятся они приблизительно с 80-х годов прошлого века) всё более широкое распространение получили так называемые «сварочные инверторы», представляющие собой лёгкий и компактный аппарат (размером примерно как лист А4 и весом порядка 2,5-3,5 кг), выгодно отличающиеся от предыдущего поколения сварочных преобразователей, представленных трансформаторными аппаратами.
Многие, а особенно из старшего поколения, наверное, помнят огромные и тяжеленные «сундуки» размером чуть ли не до пояса и весом килограмм 40-60, которые ещё совсем недавно любители собирали самостоятельно ввиду отсутствия подобных систем в продаже. Они хранились в гаражах чуть ли не у каждого второго автолюбителя.
Горение питающей электропроводки и мигание света у всех соседей в округе в момент сварки были частыми спутниками подобных устройств.
В противовес им современные инверторные аппараты могут легко и непринуждённо работать даже от домашней электросети (например, как у автора этой статьи), при этом никакого мигания света и горения электропроводки даже и близко не наблюдается.
Конечно, это сильно зависит ещё и от того, на какой силе тока осуществляется сварка. Например, я, когда мне нужно осуществлять сварочные дела, варю, используя электрод — так называемую «двоечку» сечением 2 мм.
При этом выходная сила тока выставляется на 70А (т. е. из расчёта 35А на каждый миллиметр сечения). Насколько мне удалось выяснить (тут могу ошибаться), подобные инверторы имеют коэффициент преобразования по току примерно 4,5 и, соответственно, в моём случае потребление от сети составит примерно 70/4,5 = 16,7А.
Хотя по опыту, если рука уже «поставлена» и чувствуешь процесс, то силу тока можно даже несколько уменьшить, чтобы сократить и разбрызгивание расплавленного металла — так даже аккуратней получается, шов более ровный (а можно ещё и полярность переключить на обратную, чтобы меньше разбрызгивалось – об этом ниже).
Принцип действия сварочных инверторов основан на том, что сетевое питающее напряжение, поступая в аппарат, сначала выпрямляется, и далее этот выпрямленный ток поступает на транзисторы, обладающие высокой скоростью переключений (вплоть до 100 кГц), где, благодаря этим переключениям разбивается на отрезки, то есть по сути начинает представлять собой прямоугольную форму, и далее этот прерывистый ток подаётся на трансформатор, после которого преобразуется в переменный импульсный ток также прямоугольной формы.
После чего этот ток сглаживается с помощью дросселя, а высокая частота тока позволяет использовать трансформатор меньшего размера — например, для получения сварочного тока в 160 А инверторному аппарату требуется всего лишь трансформатор весом в 250 г, в то время как в обычных аппаратах для этого потребовался бы трансформатор весом в 18 кг, а если говорить в общем, то можно сказать, что в среднем на каждый 1А тока у инверторного аппарата приходится примерно от 0,022 кг веса (или же 3,52 кг на те же 160А, что весьма привлекательно).
Кстати, ещё о токе. Несмотря на преобладание инверторных аппаратов постоянного тока, существует ещё и подвид с переменным током, способный выдавать такой ток синусоидальной и прямоугольной формы.
У таких аппаратов есть целый ряд преимуществ, одним из которых является более стабильная температура дуги, что в результате даёт более высокое качество сварного соединения. Также благодаря высокой частоте возникает эффект замедления движения заряженных частиц в дуге, они дольше находятся в разрядном промежутке, что в целом, благодаря инициации ими ионизации, ещё больше стабилизирует весь процесс.
Кроме того, благодаря постоянной смене полярности происходит уменьшение размера расплавленных металлических капель, переносящихся на материал с электрода, как бы их своеобразное «распыление», что в результате после застывания позволяет добиваться более высокого качества сварного шва из-за более равномерного размера зёрен металла.
Ещё интересный момент о полярности: сварка может осуществляться как в прямой полярности, так и в обратной (это особенно касается бытовых инверторных сварочных аппаратов постоянной полярности).
Это означает, что при прямой полярности сварочный электрод подключён к минусу, а свариваемый металл к плюсу. Такой способ позволяет нагревать металл гораздо больше, чем электрод, и он остаётся более холодным. Такой способ даёт большую глубину плавления металла, а дуга гораздо более стабильна, что позволяет получать хороший шов. Минусом такого способа является повышенный риск проплавления тонких деталей.
В противовес описанному выше, при обратной полярности электрод подключается к плюсу, а металл к минусу. При таком подходе электрод плавится гораздо быстрее, а металл проплавляется меньше, сам шов получается более широким и менее глубоким, и дуга в целом менее стабильна.

Картинка: pnevmoteh.by
Ещё немаловажной особенностью инверторных аппаратов является то, что они по своим габаритам меньше аппаратов постоянного тока, так как в их устройстве исключается выходной выпрямитель, а в целом, можно сказать, что их производительность превышает аппараты постоянного тока.
Работа всей системы инверторов любого типа контролируется электронной схемой, которая в динамическом режиме корректирует показатели, если они отклоняются от заданных, причём корректировка осуществляется быстро, в течение миллисекунд, обеспечивая оперативное выполнение относительно сложных алгоритмов.
Например, практически в каждом инверторе есть функция «горячего старта», когда подаётся максимальный ток; «антизалипание» — когда ток снижается до минимального, при касании электродом детали, чтобы избежать прилипания электрода; «форсирование дуги» — позволяет избежать залипания, когда электрод погружается в сварочную ванну (то есть расплавленный жидкий металл), при этом сила тока кратковременно увеличивается, чтобы не дать электроду прилипнуть и облегчить перенос металла с него — в уже расплавленную массу.
Для надёжного зажигания дуги в сварочных инверторных аппаратах могут прибегать к различным подходам, основная суть которых заключается в начальной ионизации разрядного промежутка. Для этого используют: повышение напряжения холостого хода; в начальный период, для инициации дуги — пробой разрядного промежутка высоковольтными импульсами от специального генератора; и даже инициацию с помощью слабого лазерного луча.
Регулировка тока осуществляется с помощью длительности и частоты следования импульсов (т. е. применяется ШИМ-управление).
Инверторы отличаются низкими пульсациями сварочного тока, так как эти высокочастотные пульсации легко отфильтровываются с применением дросселя и конденсатора, в противовес низкочастотным пульсациям стандартного трансформаторного сварочного аппарата.
Последние поколения сварочных инверторов выполняются с применением IGBT-транзисторов, представляющих собой биполярный транзистор с изолированным затвором, который работает как мощное переключающее устройство, в котором полевой транзистор на входе управляет мощным биполярным транзистором, в свою очередь, управляющим нагрузкой.
С точки зрения схемотехники сварочные инверторы выполняются по трём основным схемам:
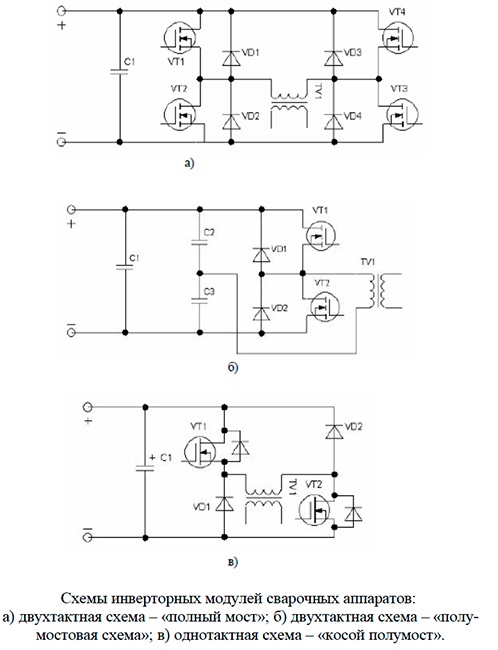
Картинка: Е.М. Таусенев, В.В. Иванайский, А.С. Шайхудинов – «Инверторные сварочные аппараты»
КПД инверторных аппаратов достигает 90% против 75-80% у обычного типа, а вес у них меньше в 4-6 раз, чем у стандартных (т. е. трансформаторных, с диодными выпрямителями).
Однако инверторные сварочные аппараты обладают и недостатками, где одним из главных является высокая сложность устройства, что, соответственно, приводит к снижению ремонтопригодности.
Кроме того, сварочные инверторы дороже трансформаторных сварочных аппаратов, а высокая частота работы приводит к возникновению специфического писка. Насчёт последнего следует отметить, что с этим успешно борются, повышая частоту и выводя её за пределы диапазона слышимости, то есть выше 20 кГц.
Кстати говоря, с этим моментом приходилось сталкиваться лично при создании проекта радиоуправляемых машинок: ШИМ-питание тяговых двигателей издавало достаточно громкий писк, который сразу «ушёл» при повышении частоты выше 20 кГц.
Отвечу на главный вопрос, который, наверное, мучает читателей на протяжении всей статьи: а зачем, собственно говоря, в городской квартире сварочный аппарат, если ты не работаешь сварщиком?
Легко отвечу: в первую очередь, он хорош для людей, которые «дружат» с руками и любят что-то делать самостоятельно, то есть для самодельщиков.
Например, раньше, когда надо было что-то собрать, я поступал так же, как и многие: шёл в хозмаг, покупал какие-либо алюминиевые балки, трубки, пытался всё это добро прикручивать к друг другу болтами, предварительно высверливая отверстия с помощью дрели.
В ходе этого процесса обычно сильно нашумишься, намучаешься, и в итоге получишь конструкцию, которая довольно спорна: из-за естественной мягкости металла (алюминия) всё это, как правило, плохо держит физические нагрузки, естественным образом со временем разбалтывается, расшатывается.
В общем, и время потратил, и деньги, и в итоге получил непонятно что…
И, совсем другое дело, когда используешь сварочный аппарат: металл для него дешевле, прочность и самого металла, и получаемого соединения даже несравнима с предыдущим вариантом. Достаточно «пару раз ткнуть» и получается «на века». Люблю такое:-)
Работы можно проводить даже дома. Например, если в ванной комнате есть кафельная плитка на полу, положить на него металлический тазик и делать всё прямо в нём, так как подавляющее большинство домашних работ как раз и требует применения сварки в очень небольших объёмах.
И вполне неплохо получается, ничего вокруг не портится, дым только сварочный, но это ладно, терпимо… :-) Кстати, он довольно быстро выветривается и по запаху похож на горящие бенгальские огни.
Ниже будет немного фото моего аппарата — внутренности сначала сфотографировал, но потом передумал выкладывать, дабы не обижать фирму-производителя. Так что не обессудьте. Вместо этого предлагаю посмотреть вот это видео:
На фотографиях рядом с аппаратом поставил лист А4 для понимания размеров аппарата (кликабельно):
Но всё-таки вы спросите: а для чего его можно применить дома? Перечислю те случаи, с которыми мне приходилось сталкиваться:
Случай 1: Мама как-то давно купила тренажёр для пресса, где в качестве силовых элементов выступали небольшие резиновые ленты по бокам, которые надо было растягивать («рукалицо» просто — насчёт того, какое инженерное решение).
Ну, и естественно, через очень короткое время эти ленты порвались, и тренажёр простаивал. Я взял и на двух сторонах этого тренажёра приварил по болту с накрученными на них резьбовыми втулками, куда, в свою очередь, прикрепил штатные крепления газонаполненных амортизаторов от автомобиля, купленных в магазине автозапчастей (ну, знаете, такие чёрные газовые амортизирующие трубки, которые помогают открывать багажник).
Получилось весьма недурно: теперь нужно сжимать и разжимать эти амортизаторы, что даёт весьма существенную и приятную нагрузку для пресса. Долговечность у такой конструкции, конечно, тоже на голову превосходит несчастную резиновую ленту :-) К сожалению, фотографии нет, показать не могу. Отмечу только, что этой конструкции уже порядка лет семи, и она верой и правдой служит каждый день, и ломаться даже не думает (равно как и расшатываться):
Случай 2: Купил раковину в ванную, и надо было её повесить, а производитель до конца не додумал, и для подвешивания раковины приложил резьбовые шпильки, у которых отсутствует какое-либо приспособление для их вкручивания в стену — то есть с одной стороны есть шурупоподобная резьба, а с другой — резьба как у болта. Чем крутить — не предусмотрено :-)))
Я просто на эту болтовую резьбу накрутил гайку, пару раз «тыкнул» сваркой — получился вполне себе удобный болт, который далее без каких-либо проблем я смог закрутить в стену (с помощью соответствующего дюбеля и т. д.).
Случай 3: Приобрёл 3D-принтер, вся электроника которого располагалась прямо под нагревательным столом и перегревалась с соответствующим вылетом по перегреву. Пришлось её переносить наверх принтера, для чего я быстро изготовил соответствующую крепёжную конструкцию из стальной трубы прямоугольного сечения. Всё это было проделано ещё в 2017 году, и, как можно подозревать, ничего нигде не расшаталось, не разболталось, не развалилась за столько лет (хотя я постоянно перетаскиваю принтер с места хранения на балкон, где он у меня и печатает). То есть я один раз потратил время и забыл навсегда об этом вопросе:
Примечание, несколько отступая от темы: если кому интересно, за счёт чего у меня держится вентилятор, обдувающий матплату 3D-принтера на фото выше — просто на стопку О-образных неодимовых магнитов его прилепил и всё. Получилось хорошо и минимальными усилиями.
Случай 4: Как-то, у меня сломалась стальная пластина прямо под компьютерным креслом (ну да, я люблю покачаться в кресле, мой грех). Пара касаний сварки — и кресло стало таким, как будто вчера выпущено с завода :-)
На самом деле, таких случаев было достаточно много, я назвал только некоторые из них.
Варить я научился достаточно быстро, а с приходом опыта научился варить даже тонкие листы металла и стальные трубки — а то раньше прожигал их насквозь, слишком долго удерживая дугу на одном месте (тогда, когда я варил эти вещи, я ещё не знал про возможность смены полярности, век живи – век учись).
Для удобства сварки ещё потребуется маска, например, я взял себе так называемую «маску-хамелеон», где защитное стекло является постоянно прозрачным и моментально темнеет при появлении яркого света (можно регулировать скорость срабатывания затемнения).
Питается такое стекло от двух источников: встроенного аккумулятора, который постоянно подзаряжается от фотоэлемента (хотел написать «солнечной батареи», но почему-то засомневался, так как здесь это будет странновато звучать), находящегося прямо на лицевой части маски — довольно оригинальное техническое решение, когда фотоэлемент заряжает аккумулятор от света горячей дуги.
Теперь, после многих лет обладания сварочным аппаратом, я могу однозначно сказать — это мастхев, даже если ты не сварщик. Мы же не удивляемся присутствию паяльника в городской квартире, а это, по сути, тот же самый паяльник просто «на максималках» :-)
Сейчас ещё полуавтоматический сварочный аппарат хочу (который на проволоке). Плюсы: зона сварки обдувается CO2 — соответственно, флюс (обмазка электродов) не нужен, шов получается чистый и не надо его отбивать потом, а что ещё важнее — сразу видно шов без отбивки флюса. Соответственно, можешь сразу визуально контролировать качество своей работы. Кроме того, тонкий диаметр сварочной проволоки делает место сварки очень локальным, не перегревая всю деталь, и, что тоже интересно, полуавтоматом варить проще, так как с ним легче научиться не прожигать тонкие листы (поэтому в автосервисах проржавевшие автомобили только им и заваривают). Одна беда — нужен баллон СО2. А хранить его в квартире или на балконе — малость перебор. Вот и не соберусь всё… Но внутри меня идёт сильная борьба и однажды… :-)))
Хотя есть и лайфхак — использовать не огромный, в рост человека баллон с CO2, а компактный, — от углекислотного огнетушителя, так что есть варианты, если подумать.
Если кто-то более подробно хотел бы изучить особенности схемотехники и конструкционных элементов, то рекомендую для этого ознакомиться с книгой: В. Я. Володин — «Как отремонтировать сварочные аппараты своими руками».
P. S. На картинке в шапке статьи изображена сварка полуавтоматом, я знаю. Просто фото красивое — не мог пройти мимо ;-)
▍ Список использованных источников
- Е.М. Таусенев, В.В. Иванайский, А.С. Шайхудинов – «Инверторные сварочные аппараты».
- С.Л. Корякин-Черняк – «Справочник сварщика: для любителей и не только».
Автор:
DAN_SEA