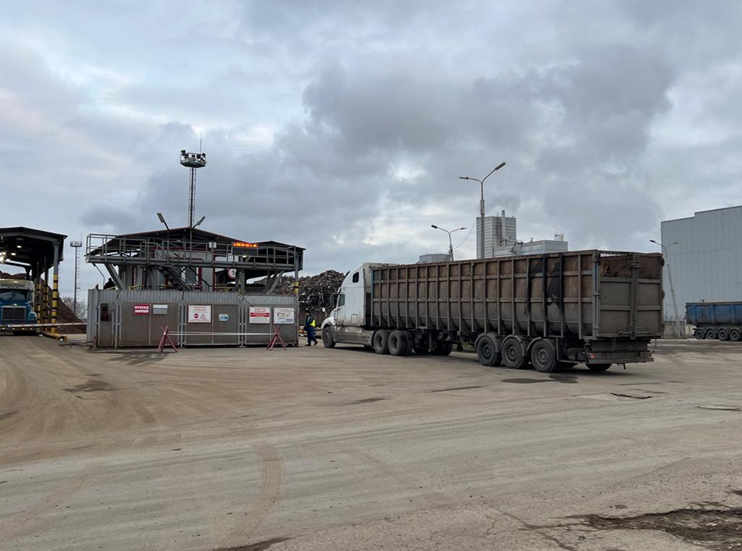
На сегодняшний момент металлолом — наше всё. Нам его надо ОЧЕНЬ много, и мы его закупаем.
Лом нам везут ломовозами с площадок сбора металлолома.
Бывало, колонна под сотню ломовозов выстраивалась в очередь на пункт выгрузки, что доставляло немало проблем. Водители могли простоять полдня в такой очереди. Она при этом двигалась, то есть водитель не мог отъехать поесть или поспать. Периодически возникали естественные ситуации, характерные для любой очереди:
— Я только спросить.
— А за меня друг занимал.
— Мне срочно — я беременный.
— Вас здесь не стояло.
Всё это вносило море хаоса.
Этот откровенный бардак не устраивал никого: ни водителей, ни операторов КПП, ни приёмщиков лома. Даже в ближайшем МФЦ уже внедрили электронную очередь! А мы чем хуже?
Нужно взять проблему, сутевую часть имеющегося решения, придать решению инженерную огранку, немного обточить модными технологиями, развернуть в контуре, запустить в работу и шедевр готов.
На словах просто, на деле — как обычно. Читать полностью »