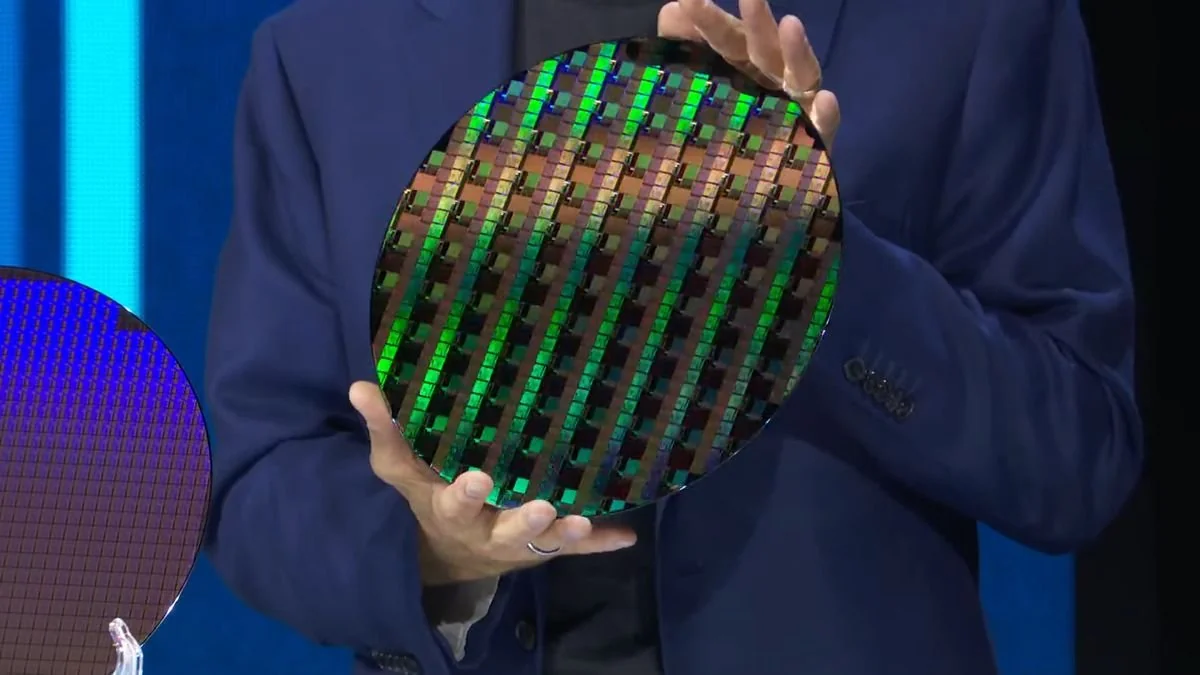
В Intel отказались от выпуска микросхем на базе узла 20A, решив перейти сразу к 18А.
И было очень много разговоров на тему, почему компания так поступила. Некоторые говорят, что Intel для исправления проблем с 18A требуется весь инженерный ресурс. Другие считают, что этот ход фактически сэкономит компании деньги, которые она сможет вложить в разработку узла 14А.
Что же касается самой Intel, то её вице-президент по технологическому развитию, Бен Селл, в своём заявлении сказал, что они полноценно освоили техпроцесс 20А, и поскольку для 18А уже удаётся получить хороший выход, компания может применить полученные знания сразу на нём.
И хотя меня в какой-то степени интересуют последствия этого решения для бизнеса, за новостями на эту тему я слежу исключительно из любопытства. Тем не менее моё внимание привлекла ключевая метрика, которую в Intel использовали для оправдания этого перехода: плотность дефектов.
Вот что сказал по этому поводу Селл (выделение сделано мной):
Когда мы решили перейти на Intel 20A, то предполагали, что знания, полученные в отношении качества выхода при использовании этого техпроцесса, станут частью перехода на Intel 18A. Но в свете того, что текущий показатель плотности дефектов для 18А уже составляет D0 < 0.40, из соображений экономической целесообразности переход нужно совершать сейчас.
Плотность дефектов ниже 0,4 означает, что более 67% производимых микросхем будут работать. А поскольку технология всё больше уходит в сторону массового производства, плотность дефектов, заявленная ведущими фабриками, опускается до 0,1, то есть полезный выход составляет уже более 90%.
В текущей статье мы разберём, как производители полупроводников вычисляют плотность дефектов и соответствующий выход годных кристаллов.
Содержание
- Полезный выход кристаллов, дефекты и стерильные цеха.
- Модели оценки полезного выхода:
- Доступный для скачивания калькулятор выхода кристаллов/плотности дефектов в формате Google Sheet
Полезный выход кристаллов, дефекты и стерильные цеха
Производители полупроводников, как и большинство других, не могут добиться работоспособности каждой микросхемы ввиду варьирующихся допусков, ошибок и физических ограничений, накладываемых реальным контекстом. Производители вроде Intel, Samsung или TSMC вкладывают значительные средства и усилия в повышение полезного выхода кристаллов, который зачастую должен быть больше 90%. Учитывая огромный объём создаваемых на фабриках микросхем, выход кристаллов является критическим критерием прибыльности, который привлекает особое внимание.
Потери в выходе связаны с недочётами, возникающими в процессе производства полупроводниковых пластин. Любой недочёт в физической структуре кристалла, который ведёт к сбою работы цепи, является дефектом. При этом аномалии могут принимать множество форм, включая короткие замыкания и разрывы, загрязнение микрочастицами, брызги, отслоения, царапины и прочее.
Чтобы сократить потери при выходе, вызванные инородными частицами, на фабриках для производства пластин создают особо чистые пространства, разделяя их по разным «классам» в зависимости от размера и количества частиц в одном кубометре воздуха.
Источник: Me-Cart Cleanrooms
Важно понимать, что столь низкий уровень количества частиц необходимо удерживать на площади примерно в миллион квадратных футов фабрики. Реализуется это при помощи масштабных ОВКВ-систем (HVAC, отопление, вентиляция и кондиционирование воздуха) и тщательной HEPA-фильтрации. Для понимания, насколько чистыми должны быть эти помещения, отметим, что чистота операционной зоны хирурга должна соответствовать Классу 100000.
Можно представить, насколько сложно построить в столь крупных пространствах стерильный цех с чистотой Класса 1. Вместо этого на фабриках для хранения и перевозки полупроводниковых пластин создают небольшие унифицированные контейнеры (FOUP, Front Opening Unified Pods), степень внутренней чистоты которых соответствует Классу 0.1. И вот в этих контейнерах, размер которых сравним с размером мусорной корзины, различные полупроводниковые элементы перемещают по фабрике. Всё это делается для снижения плотности дефектов. Если вам интересно, советую почитать книгу Брайана Поттера «How to Build a $20 Billion Semiconductor Fab», где автор очень увлекательно рассказывает о создании современной фабрики полупроводников.
Но не все потери при выходе кристаллов обусловлены дефектами. Поскольку процесс осаждения дополнительных материалов на периферии круглой пластины менее контролируем, страдает точность обработки, что ведёт к потере крайних кристаллов. И хотя производства стремятся снизить эти потери, они неизбежны, и их отслеживают путём параметрического тестирования, исключая такие кристаллы из дальнейшей обработки.
Потери выхода вследствие дефектов являются критическим фактором, который определяет готовность технологии к выводу в масштабное производство. Поскольку дефекты оказываются случайными1, выход кристаллов, обозначаемый как DY, определяется вероятностными расчётами, предполагающими произвольные распределения дефектов. Далее мы рассмотрим несколько традиционных моделей вычисления выхода.
Модели вычисления полезного выхода
Нет универсальной модели для прогнозирования выхода годных кристаллов из полупроводниковой пластины на основе количества дефектов в её конкретной области. Выбор модели зависит от того, как дефекты распределены по пластине (равномерно, по краям, кластерами и так далее), и размера кристалла. И даже эти два фактора имеют тонкую связь: вероятность дефектов при более мелких кристаллах снижается, но повышается для более узких элементов.
▍ Биномиальная модель и модель распределения Пуассона
Распределение Пуассона, традиционно используемое для описания радиоактивного распада, показывает вероятность того, что в кристалле могут одновременно проявиться k дефектов, если их среднее число в нём равно λ0. Вот соответствующая формула:
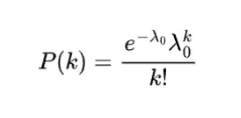
Предположим, что D0 — это количество дефектов на квадратный сантиметр, а A — это площадь кристалла в см2. Таким образом, мы получаем λ0 = D0⨉A. Для того чтобы кристалл работал, дефектов быть не должно, то есть значение DY будет P(k=0), и получаться оно будет при помощи простой экспоненциальной функции.
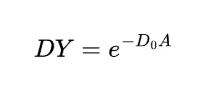
При размере микросхемы 1 см2 и плотности дефектов D0 = 0.4/cm2 выход кристаллов составит 67%. При D0 = 0.1 он будет равен 90%. Если инженеры на фабрике решат измерить выход кристаллов из пластины, то могут вычислить плотность дефектов так:
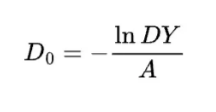
Модель Пуассона обычно хорошо подходит, когда размер кристаллов невелик в сравнении с диаметром пластины, и когда дефекты распределены по ней достаточно равномерно.
Разновидностью этой модели, но более обобщённой для площади, является биномиальная модель. Вместо вычисления плотности дефектов по их среднему количеству на единицу площади, в ней используется общее число дефектов на пластину, на основе которого рассчитывается вероятность присутствия дефекта на любом отдельном кристалле в соответствии с биномиальным распределением. Если площадь пластины значительно превосходит площадь кристалла, как это обычно бывает в 12” пластинах, то вычисления производятся по модели Пуассона. Мы не будем углубляться в подробности, поскольку модель Пуассона в любом случае является более популярной.
▍ Модели Мёрфи, Сидса и Бозе-Эйнштейна
Модель Пуассона и биномиальная модель предполагают, что дефекты распределены по пластине случайным образом. Но во многих случаях дефекты склонны концентрироваться рядом друг с другом, и как только на микросхеме появляется один, она отбраковывается, и другие дефекты на ней уже становятся неактуальны. При более крупных размерах на одной микросхеме может кластеризоваться больше дефектов, в случае чего вычисления по модели Пуассона склонны давать заниженный результат по объёму выхода.
В более обобщённом виде плотность дефектов (D) можно выразить как распределение f(D) со средним значением D0. Исходя из этого, Б. Т. Мёрфи из Bell Labs предложил вычислять выход кристаллов так:
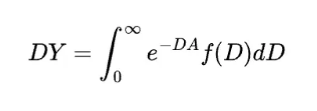
На рисунке ниже показано несколько форм, которые f(D) может принимать в зависимости от того, как дефекты распределены по пластине.
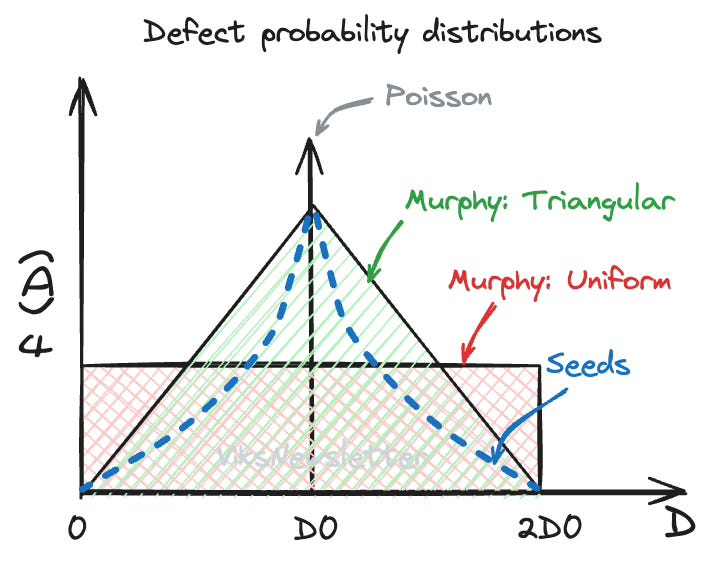
- Если f(D) — это дельта-функция со средним D0, вычисление выхода кристаллов будет производиться по модели Пуассона.
- Если f(D) равномерно распределено между 0 и 2D0, выход кристаллов после интеграции вычисляется так:
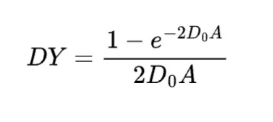
- Если f(D) приблизительно равно гауссову распределению с функцией треугольника, выход кристалла вычисляется так:
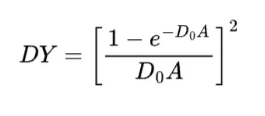
Использование треугольного распределения для вычисления выхода кристаллов называется моделью Мёрфи.
- Если f(D) принимает форму экспоненциального распределения, то выход кристаллов после интеграции вычисляется так:
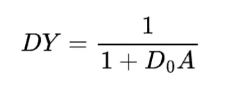
Это модель Сидса.
Расширенной версией модели Сидса является модель Бозе-Эйнштейна, в которой учитывается, что каждый из «n» критических слоёв при обработке пластины имеет собственную плотность дефектов. Вычисление выхода кристаллов в этой модели производится по следующей формуле (где DD представляет плотность дефектов на слой):
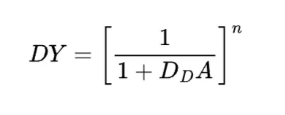
В вычислении по модели Бозе-Эйнштейна присутствует небольшое отличие, которое объясняется несколько иным значением плотности дефектов. Во всех остальных моделях вычислений с присутствием D(0) единицей измерения выступает число дефектов на квадратный сантиметр. Но на большинстве фабрик показатель DD в модели Бозе-Эйнштейна выражается в виде количества дефектов на дюйм2 слоя. Вы можете выполнять преобразование между D0 и DD, используя онлайн-калькулятор или мой бесплатный калькулятор в Google Sheets.
Ещё один подвох в том, что при вычислении выхода кристаллов по модели Бозе-Эйнштейна плотность дефектов не обязательно будет одинаковой в каждом критическом слое. Если эти показатели отличаются, то вместо возведения в степень «n» показатели выхода для отдельных слоёв можно перемножать.
Другие модели
При больших размерах кристаллов и использовании более гибкой модели для вычисления выхода в качестве f(D) выбирается гамма-распределение. Такой подход называется моделью отрицательного биномиального распределения, в котором выход кристаллов вычисляется так:
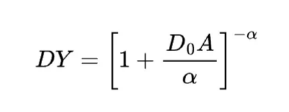
Это уравнение требует приблизительного значения для 𝛼, называемого параметром кластера, который определяется средним и стандартным отклонениями количества дефектов на кристалле. Причём в зависимости от величины 𝛼 отрицательное биномиальное распределение можно использовать для эмуляции других моделей: Пуассона (𝛼 > 10), Мёрфи (𝛼 = 5), и Сидса (𝛼 = 1).
В 1970 году Горден Мур в своей работе «What level of LSI is best for you?» предложил модель вычисления выхода, которая лишь немного отличается от модели Пуассона и используется редко.
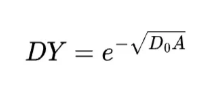
Обобщение
На графиках ниже показан выход кристаллов, вычисленный при помощи самых популярных моделей. При условии относительно небольшого размера кристалла самой используемой оказывается модель Пуассона, что объясняется её простотой. При больших кристаллах чаще используется модель Мёрфи с треугольным распределением или модель Бозе-Эйнштейна. Вне зависимости от используемой модели (за исключением Бозе-Эйнштейна) выход кристаллов при D0=0.4 дефектов/см2 составляет примерно 67-71%.
При вычислении выхода с помощью модели Бозе-Эйнштейна фабрики отражают плотность дефектов (DD) в виде количества дефектов на дюйм2 слоя. Итоговые результаты также зависят от количества присутствующих в процессе критических слоёв. Чем меньше технологический узел, тем больше критических слоёв и сложнее получить хороший показатель выхода. На графике ниже представлен коэффициент критичности 35,5, который соответствует узлу 5 нм.
Вне зависимости от метода вычисления, при плотности дефектов, равной D0 < 0.1 дефектов/см2, выход кристаллов составляет примерно 90%, что указывает на зрелый и пригодный для производства технологический узел.
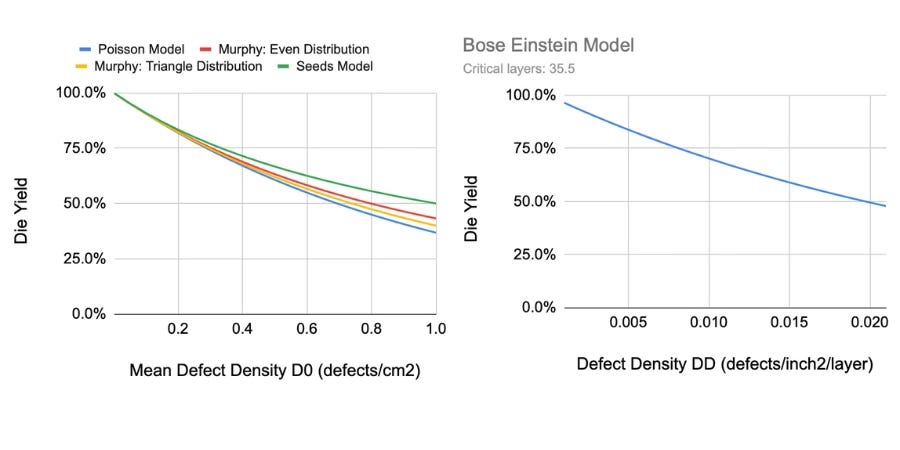
Дополнительные ресурсы
- Мой калькулятор в Google Sheets для вычисления выхода с помощью всех описанных моделей доступен здесь.
- Онлайн-калькулятор для примерного вычисления выхода кристаллов на пластину с учётом плотности дефектов при помощи модели Murphy.
- Yield Modeling and Analysis by Prof. Robert C. Leachman.
- B. T. Murphy, «Cost-size optima of monolithic integrated circuits,» Proc. IEEE, vol. 52, no. 12, pp. 1537–1545, 1964, doi: 10.1109/PROC.1964.3442.
- I. Tirkel, «Yield Learning Curve Models in Semiconductor Manufacturing», IEEE Trans. Semicond. Manufact., vol. 26, no. 4, pp. 564–571, Nov. 2013, doi: 10.1109/TSM.2013.2272017.
- N. Kumar, K. Kennedy, K. Gildersleeve, R. Abelson, C. M. Mastrangelo, and D. C. Montgomery, «A review of yield modelling techniques for semiconductor manufacturing», International Journal of Production Research, vol. 44, no. 23, pp. 5019–5036, Dec. 2006, doi: 10.1080/00207540600596874.
- J. E. Price, «A new look at yield of integrated circuits», Proc. IEEE, vol. 58, no. 8, pp. 1290–1291, 1970, doi: 10.1109/PROC.1970.7911.
Сноска
1. Они тоже могут быть систематическими, и рассматривать это нужно не просто через призму вычисления вероятностей.
Автор: Bright_Translate