Речь пойдет про портативную электростанцию, которая в перспективе сможет потреблять любое органическое топливо, от природного газа до коньяка, и перерабатывать его в электричество без сжигания. Цель всей затеи — заменить всевозможные дизель-генераторы на что-то более экологичное и изящное, не требующее постоянного внимания. Например, вы привезли на какой-то удаленный объект баллон топлива и забыли про обслуживание мини-электростанции на целый год. Она работает и работает.
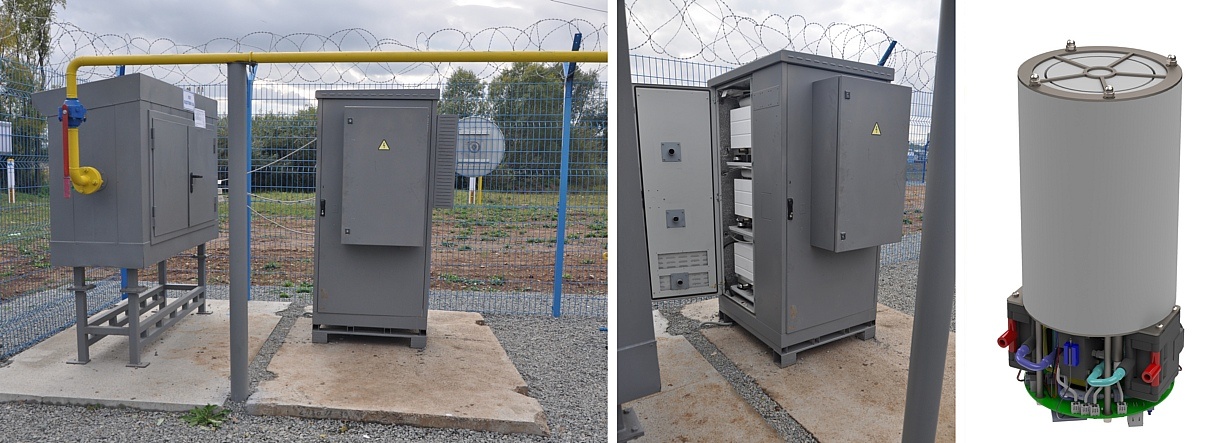
Причем эта самая электростанция может масштабироваться от 100 ватт и до практически неограниченной мощности. На фото выше в шкафу установлена система мощностью чуть больше одного киловатта, состоящая из трех планарных элементов. Справа — рендер микротрубчатого элемента — ноу-хау. Под катом есть фото одного из прототипов размером с компактную кофеварку.
В целом идея не нова, но тут удалось снизить стоимость производства сложного электрохимического топливного элемента, сделав его компактным и коммерчески интересным, причем начиная с самых малых мощностей.
Вкратце о топливных элементах
Прежде чем переходить к ноу-хау «Топаза» (так называется серия этих самых мобильных энергоустановок от InEnergy), несколько слов об общей теории электрохимических генераторов.
В основе любого электрохимического топливного элемента три базовых слоя — анод, катод и расположенный между ними электролит. Анод и катод изначально электрически нейтральны, но на их поверхности протекают разные химические процессы, за счет чего электроды обмениваются зарядами — ионы проходят через электролит, а электроны через внешнюю цепь. Обычная батарейка работает как раз по такому принципу, преобразуя химическую энергию в электричество.
В генераторах «Топаз» используют твердооксидные топливные элементы, в которых в электричество преобразуется энергия органического топлива. Например, реакция с метаном выглядит так:
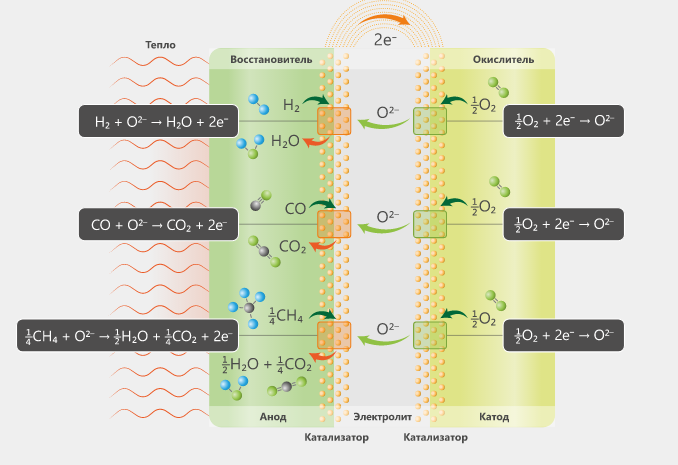
Вместо метана можно использовать любое другое энергоемкое органическое топливо.
Материалы анода и катода, а также электролит подбирают таким образом, чтобы обеспечить транспорт ионов к месту реакции.
Это значит, что электролит должен пропускать ионы кислорода из воздуха к аноду, но в то же время не допускать смешивания воздуха и газообразного топлива.
И такие вещества существуют. Но свои свойства они проявляют в особых условиях. Например, диоксид циркония является кислородопроводящим при очень высоких температурах — от 750 градусов по Цельсию и выше.
Чтобы генератор работал непрерывно, топливо на анод и окислитель (кислород из воздуха) на катод подают извне. В теории такой элемент может окислять любое топливо, но скорость реакции будет тем меньше, чем тяжелее это топливо. Поэтому, чтобы реакция шла с достаточной скоростью, топливо надо расщеплять на простые компоненты. Для этого необходим так называемый реформер — блок предварительной подготовки сложного органического топлива. Реформер так же работает при высоких температурах — от 600 градусов по Цельсию.
В чем ноу-хау «Топаза»
Технология высокотемпературных топливных элементов известна довольно давно — как минимум пару десятков лет ее пытаются применить различные научные группы по всему миру. В США даже создан альянс Solid State Energy Conversion (SECA), который занимается ускорением промышленной интеграции подобных технологий.
Однако до сих пор основной сферой применения такой конструкции были стационарные установки мощностью от 1 кВт. Стоимость установок получалась довольно внушительной, так что продукт не получалось сделать массовым.
Создателям Топаза удалось существенно удешевить производство высокотемпературных топливных элементов и сделать их применимыми в мобильных кейсах.
Вместо так называемой планарной (плоской) топологии элемента они использовали трубчатую систему и значительно сократили размер этих трубок.
Основа — анод — имеет цилиндрическую форму. Его диаметр 3 мм, а оптимальная длина — 10 см. Трубка покрыта несколькими разными слоями керамики, которые обеспечивают ее работоспособность в качестве топливного элемента. Толщина стенки трубки (включая все слои) — около 0,5 мм.
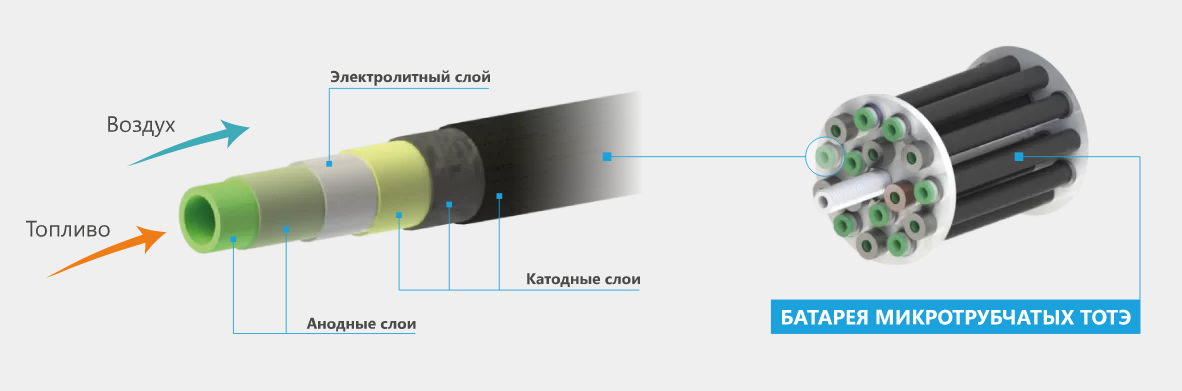
К такой форме трубок пришли не сразу. Этому предшествовала целая серия экспериментов с экзотическими формами и поверхностями. Пробовали, например, форму трилистника (трубку, поперечное сечение которой напоминает трилистник). Но стоимость нанесения равнотолщинного газоплотного слоя электролита на трубку экзотической формы в разы выше — для этого необходимо использовать дорогое оборудование, чистые комнаты или специальные атмосферы. И даже несмотря на такую подготовку, в производстве остается много брака, что делает итоговый результат еще дороже.
А с цилиндрической формой все проще. В ходе производства основу просто окунают в условные ведра с разными суспензиями прямо на воздухе, нанося до шести слоев разных материалов, а потом одновременно спекают их все в печи. Используемые суспензии — это керамические порошки с растворителем. Они подобраны по составу таким образом, чтобы с учетом вязкости и смачивания поверхности после запекания и выжигания растворителя образовывать слои нужной толщины. При этом часть слоев остаются рыхлыми, а один из них — газоплотным, чтобы предотвращать смешивание топлива и воздуха.
Конечно, в гараже на коленках такое не соберешь — нужны лабораторные условия. Например, «ведра» с суспензиями керамических порошков, в которые окунают трубки, герметичны, чтобы минимизировать попадание пыли. Плюс рецепты суспензий, как и топология установки, — ноу-хау. Топливные элементы чувствительны к дефектам поверхности. Но за счет рецептуры и толщины пленки ее качество повысили, чтобы снизить долю производственного брака, который нельзя отследить простыми средствами.
С одной небольшой трубки можно снять не такую уж большую мощность — всего около 1 Вт. Но их можно соединить параллельно и создать топливный элемент много большей мощности.
Как оказалось, маленькие трубки имеют целый ряд преимуществ. Они не требуют подготовки к работе и длительного разогрева, обеспечивают большую удельную мощность с единицы поверхности. И они механически прочные — настолько, что генератор можно использовать в носимых устройствах и на мобильном транспорте, например в электросамокатах.
Удлинение или увеличение толщины трубки ведет к ухудшению механических свойств, поэтому до сих пор технологию не пытались применять к портативным устройствам.
А еще на длинных трубках появляется проблема эффективности снятия тока с элемента — чем она длиннее, тем больше потери на транспорте зарядов вдоль ее оси.
Маленькие трубки можно соединять параллельно, тем самым увеличивая мощность установки. Правда, оказалось довольно сложно закрепить трубки внутри топливного модуля герметично, но так, чтобы они не ломались. В отличие от существующих на рынке разработок, для «Топаза» решили не использовать специальный клей, а проработали технологию закрепления и герметизации трубок «насухую», которая также позволяет снимать с них ток. На ее разработку ушло почти два года.
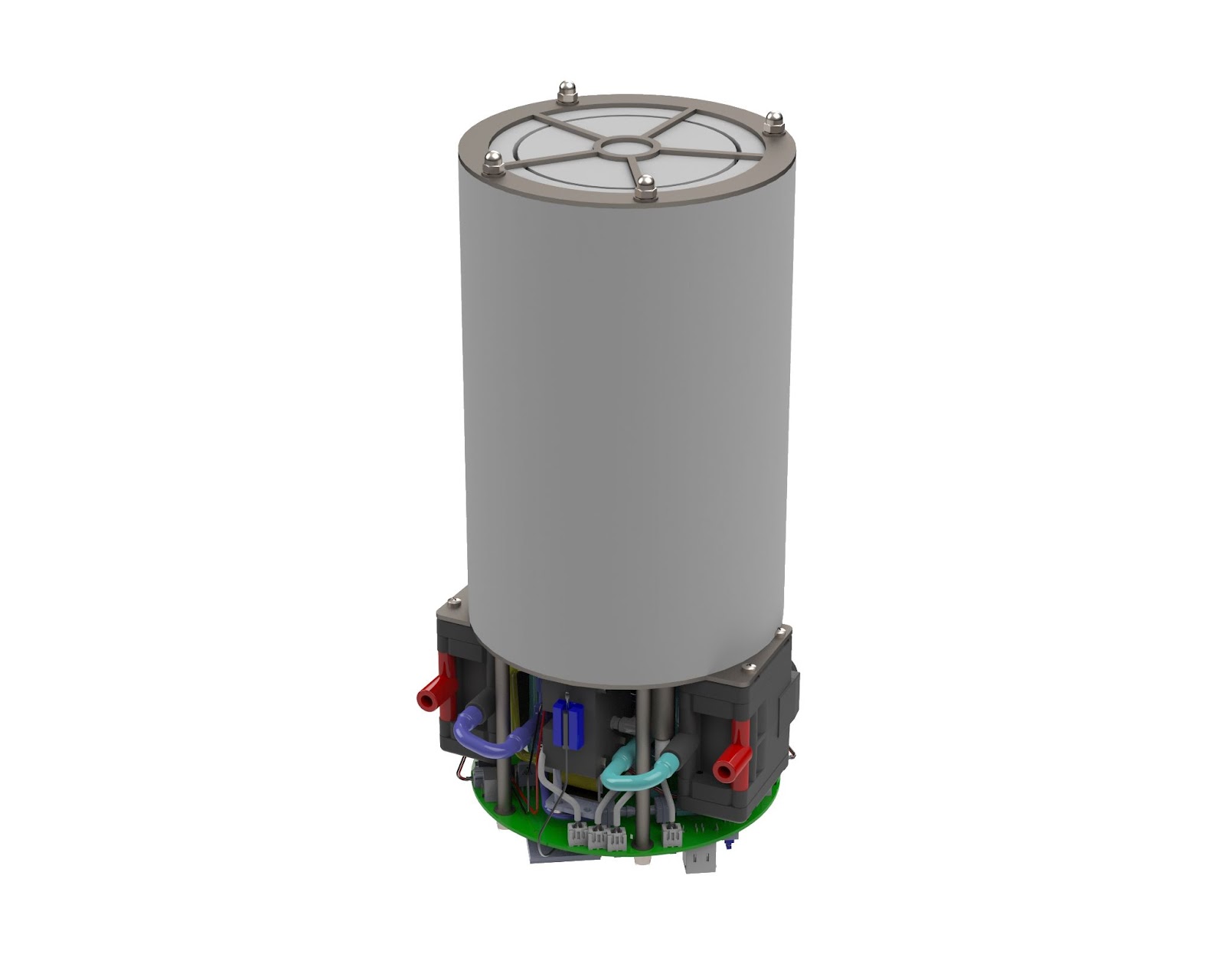
В итоге одна батарея представляет собой набор трубок, соединенных параллельно, дополненный реформером и другими блоками. Во время работы подготовленное топливо подают внутрь батареи — в трубки, а снаружи сборку обдувают воздухом при помощи вентилятора — так вырабатывается электрический ток.
Протекающая химическая реакция определяет напряжение, а площадь поверхности трубки — силу тока, который она вырабатывает. Всем этим управляет блок электроники, которая следит за поддержанием постоянной температуры работы установки и дозирует топливо.
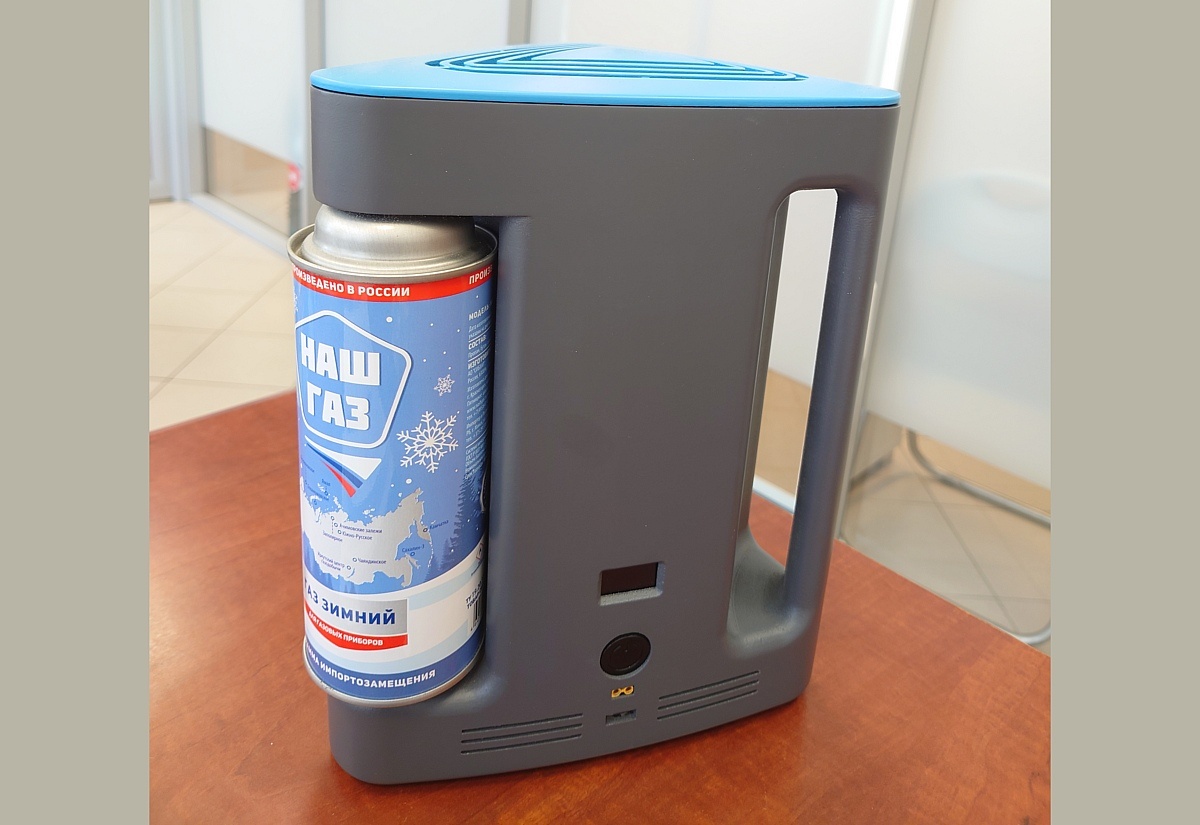
С газами все как бы просто, а вот возможность работы на жидком топливе пока отрабатывают — тут нужна несколько иная работа реформера. А еще под каждый вид топлива необходимо менять настройки: варьировать сочетание объема газа, подаваемого внутрь трубки, и воздуха, который обдувает трубку снаружи — банально разное количество молекул кислорода необходимо для окисления одной молекулы топлива. Сейчас замену вида топлива делают перепрошивкой электроники, но в перспективе можно заложить варианты в профили настроек и дать пользователю возможность переключаться между ними.
Выхлоп, повышение КПД и стоимость выработанной энергии
Трубка имеет небольшую длину, поэтому все молекулы топлива окислиться не успевают. Не прореагировавшее топливо выходит из трубки в блок дожигателя, где утилизируется. В этом блоке также происходит окисление без открытого пламени, но уже без выработки электрического тока.
Вся энергия остатков топлива уходит в тепло, которое используется для подогрева реформера и самих топливных трубок.
Чтобы эффективнее использовать это тепло, а заодно защищать потребителя от воздействия высоких температур, вокруг корпуса топливного элемента укладывают специальную теплоизоляцию.
Остаточного тепла, которое вместе с выхлопом поступает в атмосферу, совсем немного. Состав этого выхлопа — водяной пар и CO2. Для установки мощностью 100 Вт содержание CO2 в выхлопе соизмеримо с долей углекислого газа в воздухе, выдыхаемом одним человеком (примерно 4,5%). В теории для повышения КПД установки в больших модульных установках тепло этого выхлопа можно использовать для вращения дополнительной турбины или обогрева других объектов, например домов или отдельных помещений.
Учитывая невысокую стоимость производства генератора, стоимость энергии (кВт·ч), выработанной им, в основном определяется стоимостью самого топлива. В отдельных кейсах ее можно приблизить к стоимости кВт·ч из розетки. Например, гипотетическая установка мощностью 250 кВт, работающая на природном газе из газопровода, с учетом амортизации в течение 10 лет обеспечит стоимость кВт·ч на уровне 5 руб. Это на порядок меньше, чем стоимость энергии, выработанной при помощи дизель-генератора.
Мощность и ее масштабирование
Взяв больше трубок, можно добиться нужной мощности. Для этого трубки собирают в модули по несколько десятков штук.
Количество модулей при необходимости можно наращивать практически неограниченно.
При этом модули подключают независимо друг от друга, так что и менять их можно без остановки всей электростанции.
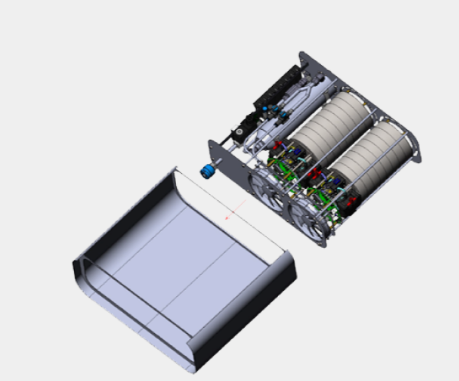
Масштабирование установки поднимает вопрос о способе плотной упаковки трубок внутри модуля. Сейчас в сборке трубки не касаются друг друга — это помогает при обдуве кислородом использовать всю площадь поверхности катода. Возможно, в больших установках будет эффективнее укладывать трубки в ряды, оставляя зазор только между рядами (трубочно-планарная геометрия). Это несколько сократит мощность, снимаемую с каждой трубки, зато позволит разместить больше трубок в том же объеме.
А вот сокращать мощность установки ниже определенного предела нерентабельно.
Парни из InEnergy говорят, что использовать меньше 40 трубок неэффективно — тепла, вырабатываемого в дожигателе, просто не хватит на то, чтобы поддерживать температуру внутри реформера и на самих топливных трубках. На подогрев придется тратить дополнительную энергию (забирать часть выработанного электричества), что снизит общий КПД.
Холодный пуск и ресурс
Чтобы выйти на основной режим работы, после старта топливный элемент с помощью специальных катализаторов разогревается самостоятельно, а дальше электроника помогает поддерживать эту температуру, используя энергию из дожигателя. Особенность этих процессов такова, что количество перезапусков устройства ограничено. Каков ресурс — пока до конца не понятно, поскольку испытания еще не закончены. В версии, которая будет выпущена на рынок, инженеры ориентируются на 1000 перезапусков и более, иначе устройство потеряет свою коммерческую привлекательность.
Ограничение на количество перезапусков связано с ресурсом катализаторов и никак не влияет на длительность непрерывной работы. Этот срок довольно большой, но какой точно — до конца испытаний тоже неизвестно. Аналогичные разработки в Японии имеют гарантийный срок эксплуатации 90 тыс. часов — это 12 лет непрерывной работы. Сколько времени установка с тонкими трубками будет работать в разных условиях, в том числе в мобильном исполнении или в суровом климате Крайнего Севера, предстоит выяснить. Пока в реальной длительной эксплуатации находится только одна установка, ее наработка уже порядка 5 тыс. часов.
Чем все закончится…
Года через два InEnergy планирует запустить опытное производство с тиражом несколько тысяч изделий в год. Но это как бы их декларируемые планы. Нюанс в том, что для перехода от стадии НИОКРа и пяти прототипов к массовому производству нужно очень много денег. Это как если бы у вас был на руках фантастический рецепт идеальной «Колы» и оставалось «лишь» построить цеха, установить дорогое разливочное оборудование, нанять людей и запустить все производственные процессы. Сущие «мелочи».
Скорее всего, этот проект будет наполовину профинансирован через НТИ. Он оказался в шорт-листе среди прочих, которые подавались на Архипелаг (это такой проектно-образовательный интенсив). В этом же шорт-листе много всего интересного, и есть пара компаний, о которых мы уже рассказывали: то были интервью с Robbo и iPavlov. В этот раз ребята из Robbo начали создавать многофункциональную образовательную платформу, а iPavlov готовит широкое внедрение разговорного AI везде где только можно. Мне лично тема кажется актуальной, уже начала вытаскивать подробности из их разработчиков. Надеюсь, будет интересно не только мне.
Автор: Светлана Болгова