Всем привет.
Странная идея владения собственным станком для раскроя листового материала пришла мне в голову довольно давно - когда я оказался на производстве во г.Владимире. В то время, да и сейчас, я провожу большую часть времени в офисе, и конкретно для меня это объективно эффективнее с финансовой точки зрения. Вместе с тем, однажды увидев магию, которая превращает материал в полезные вещи, от такой мысли отделаться я уже не мог.
Изучая конструкции фрезерных станков, я понял, что они достаточно разнообразны, в аспекте количества осей, перемещения по ним материала и фрезера, и прочих тонкостей. Где-то, в одном станке работают несколько синхронизированных фрезеров, где-то используется сложная система рычагов, которая позволяет рассчитать положение по сложной формуле. Апофеозом конструкторской гениальности считаю вот такое:
Но вернемся к моей идее - она была в том, чтобы раскраивать листовой материал, и фрезеровать в 3d какие-то мягкие формы, например, полистирола.
Конструктив рамы был выбран из соображений жесткости треугольной формы (как водится, ее изменили уже на ходу):
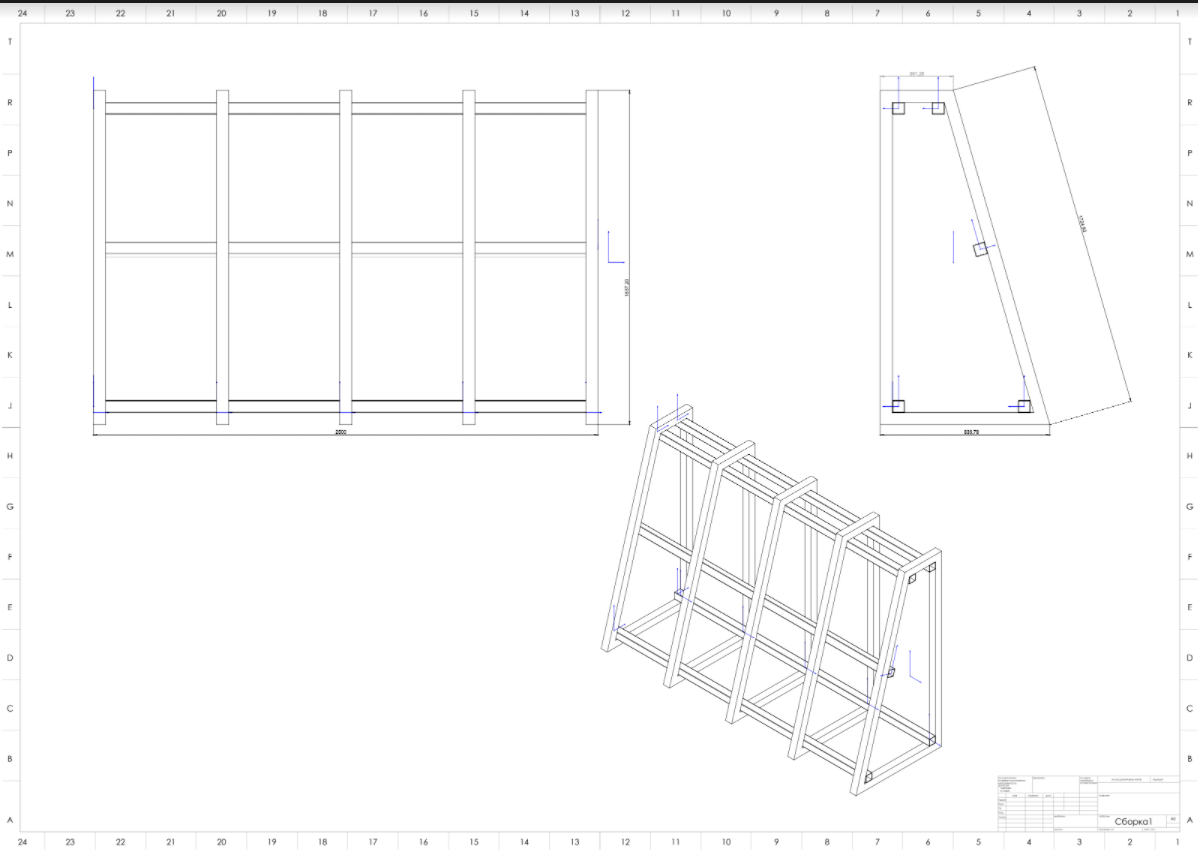
Плюс такой конструкции в том, что станок занимает меньше места, и намного проще установка на него нового листа. Бонус - стружка падает вниз (но ее все равно надо отводить, так что это не очень важно).
Но в чем проблема с этим конструктивом? Дело в том, что ось Z, которая в любом случае достаточно тяжела, ездит вверх под своим весом, и, стало быть, требует более мощного ШД и драйвера. Первой мыслью было установить на тросе через блок противовес, но на форумах не очень хорошо отзываются о тросовых решениях из-за инерции. Но имея площадь, всегда можно завалить станок на длинный катет, и уменьшить этот эффект.
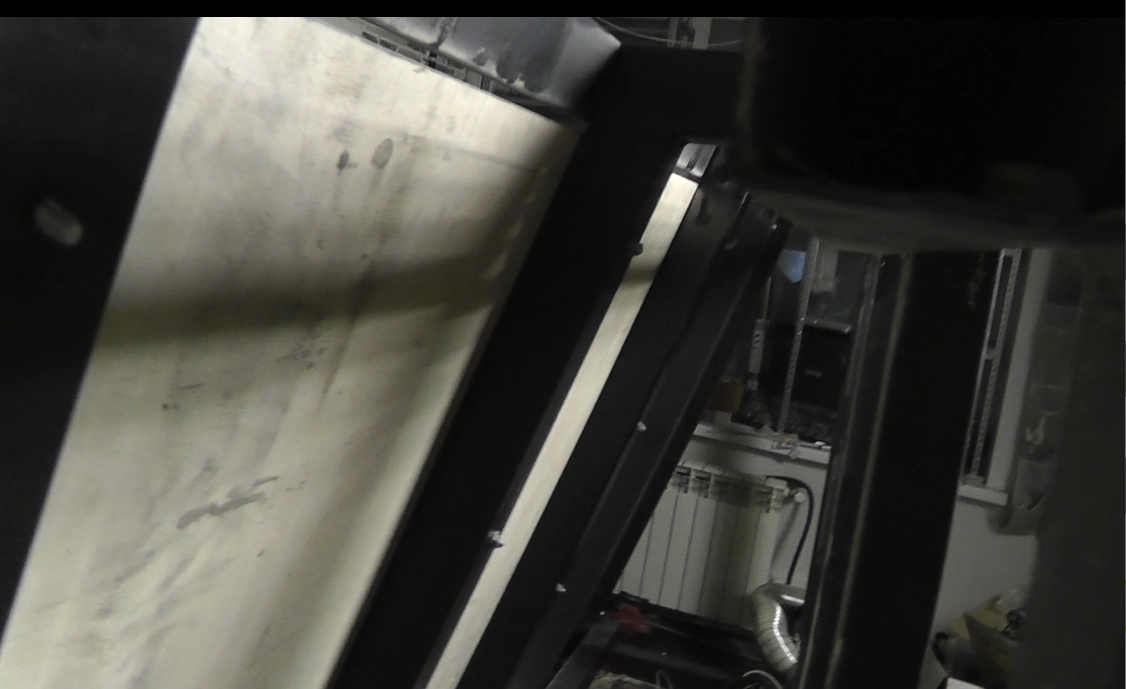
При наличии свободной площади, наверное, идеально было бы разместить треугольники развернутый через один, получился бы такой стол с очень жесткой станиной.
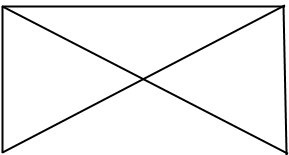
Механика. На оси Z установлена ШВП (шарико-винтовая передача).
ШВП обеспечивает максимальную точность позиционирования инструмента, но медленное перемещение. Имея серводвигатели, которые раскручиваются до серьезных оборотов, это не проблема, а у шаговых двигателей таки есть предел разумного использования. Но есть и еще одна проблема с винтом. Будучи свободным, на больших длинах он деформируется, плюс у него есть инерция, и имеет место явление резонанса. Поэтому я решил остальные 2 оси X,Y делать на зубчатой рейке, что на текущий момент считаю ошибкой. Дело в том, что в интернете мало информации, и только недавно в широкой продаже в РФ появились готовые подвижные гайки с редукторами для ШВП - это, по идее, решает проблему инерции винта (но не резонанса).

Что касается передачи на зубчатой рейке, с ней все неплохо, кроме одного - люфты. Они возникают из-за точности исполнения, и неточности установки. Та рейка, которую я купил, была дешевой и тонкой, поэтому испытывает деформации. Не советую делать так.
Фрезер. Я решил для начала взять чего попроще, с воздушным охлаждением (и так по сей день и оставил). Это, конечно, kress. Дешево, и со вкусом. Видел в интернете схемы переделки на цифровое управление оборотами шпинделя, и даже пневмо автосмену (!) инструмента kress - то есть в случае чего можно ловко наколхозить, и будет как у взрослых дядь на станках за $100K.
Что по механике. Ось X - внезапно это та, по которой ездит Z (хотя как по мне, логичней чтоб по Y), двигается ШД с планетарным редуктором. По дурости, я умудрился свернуть шляпки двух болтов, и поэтому там 2 из 4, но ничего. Шестерня зафиксирована на конус + фиксатор резьбы неразъемный.
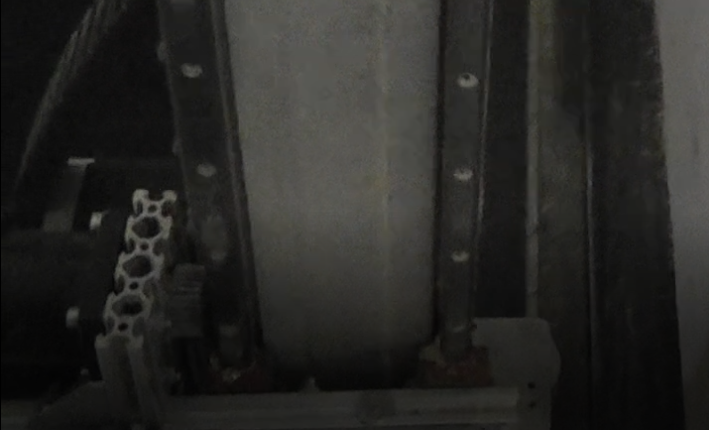
Ось Y Устроена сложнее. Там тоже редуктор, но червячный, итальянский, далее полуоси через карданы от Волги, и на концах еще ременные редуктора. Очень важно застопорить эти редуктора на зубчатой рейке, чтоб не было люфта. По какой-то причине, я решил, что мебельные лифты подойдут (нет). При фрезеровании сила противодействия такая, что лифт отжимает насколько, что перескакивает шестерня. Пришлось поверх этого колхозить прижимающий эксцентрик.
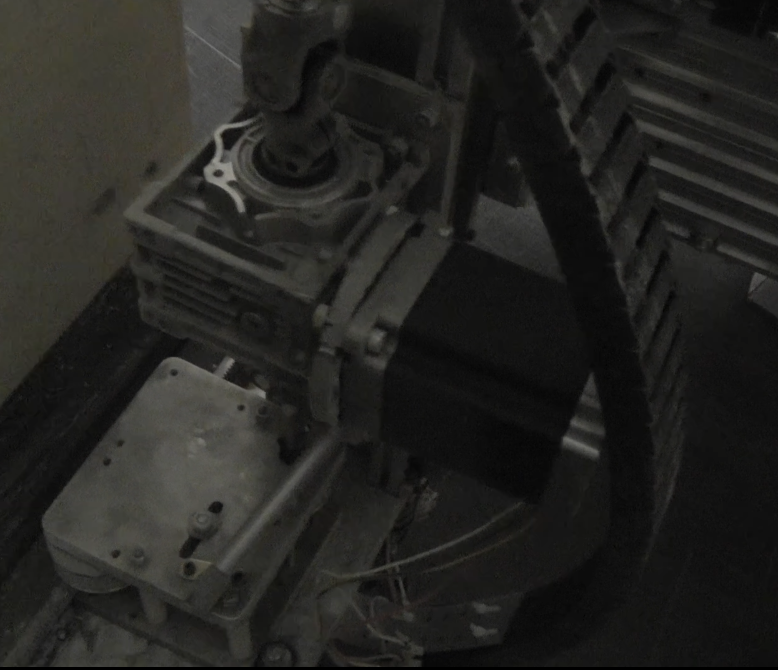
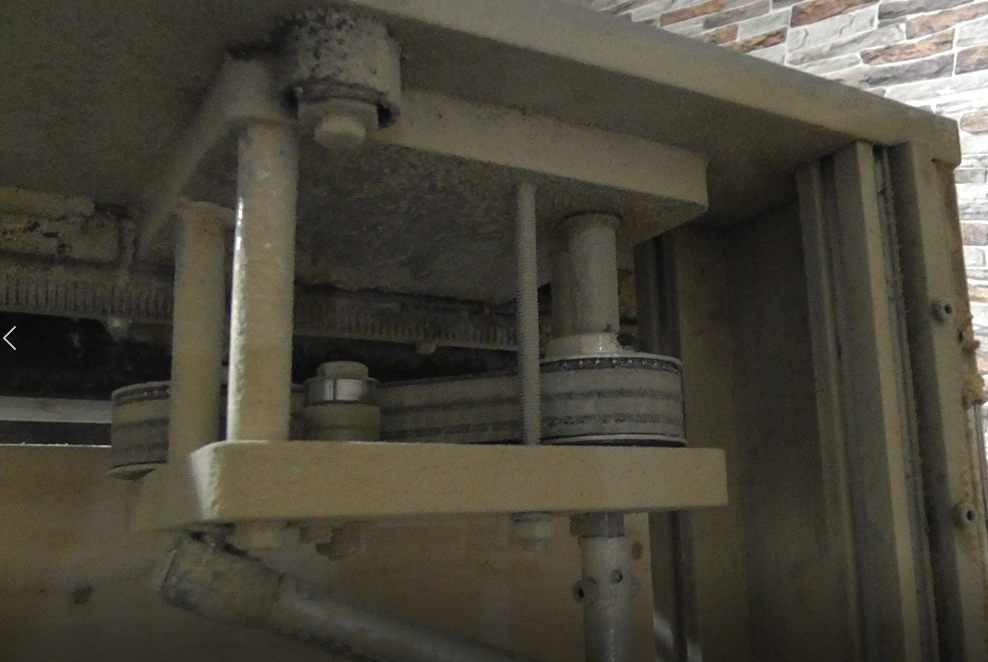
Вообще, ось Z - самое мощное что есть в станке, все остальное, фактически на соплях. Изначально, правда, я вообще хотел взять могучую металлическую балку к качестве X, зафиксировать ее на бетонных колоннах, и гонять под ней подвижный стол - но по причине пыли, от этого решения пришлось отказаться, станок стал более традиционным и переехал в отдельную комнату. Вот эта балка, лежит во дворе под снегом (от нее уже отрезаны куски болгаркой в хозяйственных целях). Если вы решите заняться сооружением промышленных девайсов дома, вряд ли и вы избежите переделок.
Вообще, особое значение имеет система аспирации. Если вы не будете ее делать, готовьтесь, что при работе с деревом мельчайшая пыль накроет ВСЕ что есть в помещении, включая ваши глаза, волосы и кожу, а если вы работаете с фанерой, то она будет еще и с химикатами, что совсем неприятно.
Наиболее простым мне показалось купить циклон на али, и прикрутить к бочке для воды, а на вывод циклона посадить на пену шланг пылесоса. Несмотря на кажущуюся хлипкость конструкции, если ввод с фрезера забьется, мощности пылесоса хватает чтобы сколлапсировать бочку в бараний рог за несколько секунд, а распрямлял я ее полчаса, и был весь в этой пыли - так что советую следить за всем этим через камеру наблюдения, попивая пиво в другой комнате.
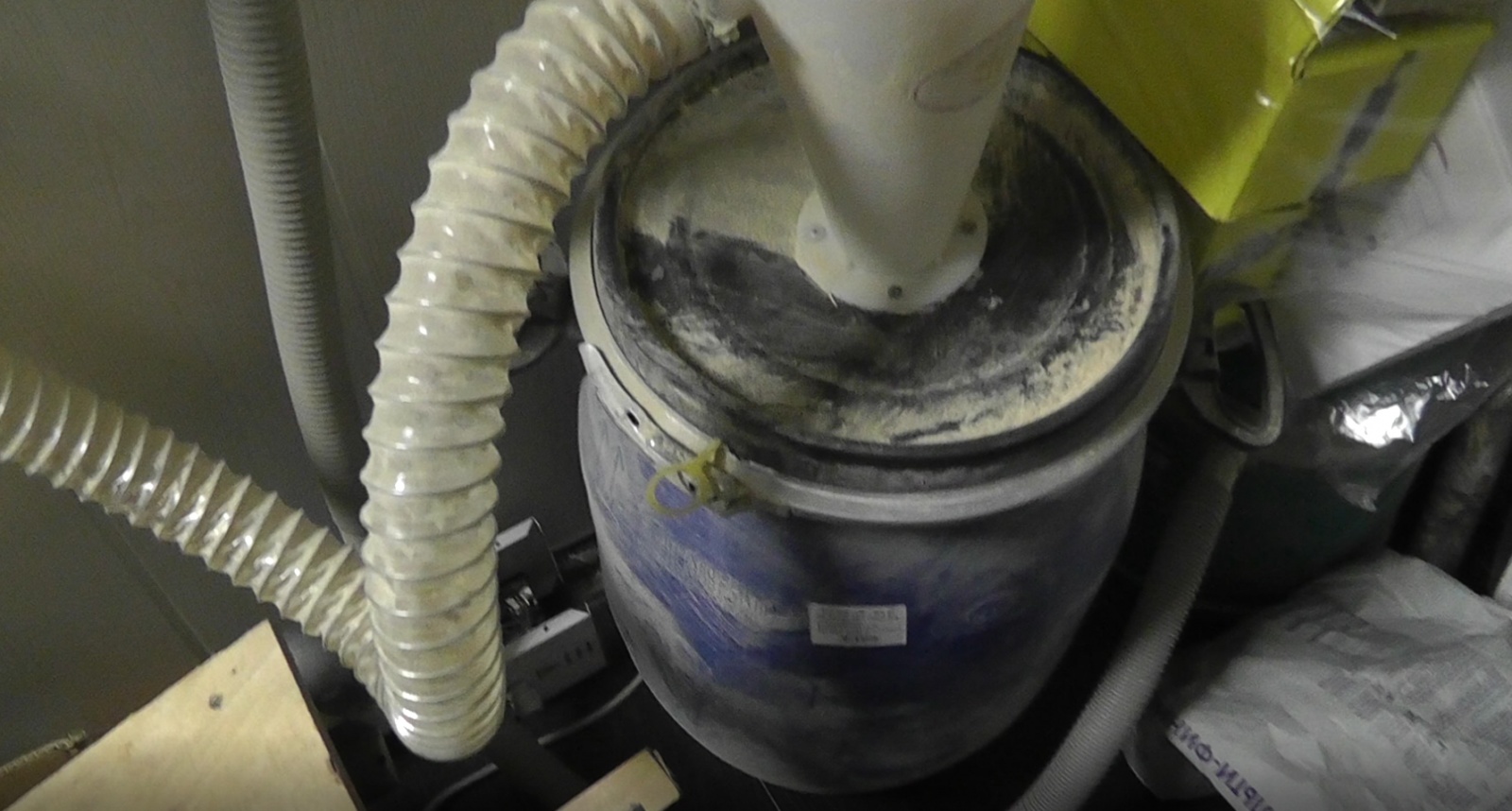
На сладкое я решил оставить электронику. У меня была назойливая идея - запихнуть все в системный блок от компа (и протянуть туда канал чистого воздуха из другой комнаты), и я ее успешно реализовал, но с оговоркой - драйвера под всасывающий вентилятор встали впритык на 3 оси. Как можете видеть, монтаж на стяжках четкий, блок можно поворачивать на 90% не переживая.
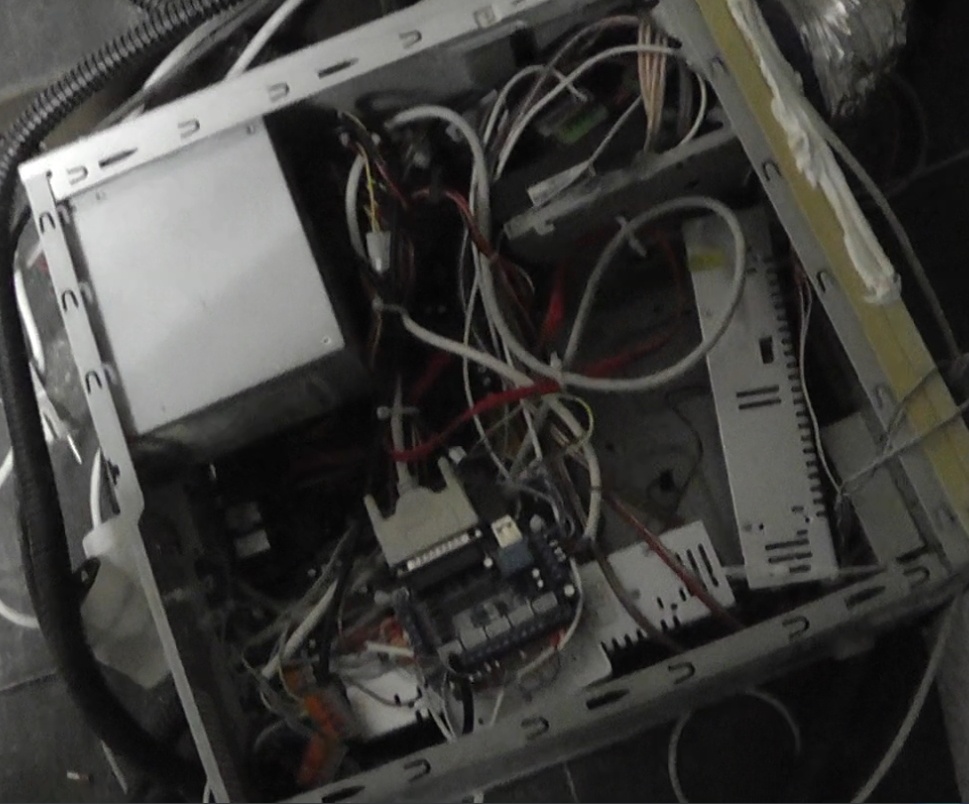
Там, где в оригинале должны стоять CD и жесткие диски, располагаются драйвера, на них я поставил втягивающий вентилятор, и будучи осведомленным о пыли, к нему протянул вентканал и гофру из соседней комнаты (теперь не помешает также щель или клапан на улицу, так как избыток давления, очевидно, тупо выдавливает через дверные щели (это ощущается). В передней и нижней части размещены блоки питания драйверов (несложно понять, что один из них запитывает 2 драйвера, и теоретически можно запихнуть в системный блок все 5 драйверов, купив мощный БП, поскольку отбор максимальной мощности вряд ли будет со всех 5 одновременно, а во время удержания потребляемая мощность ШД не очень большая).
В задней нижней зоне, над материнкой, располагается плата управления, в которую по идее должны заходить 5*4=20 входов только с драйверов, но часть из них идет на один вход, так что все ок. Остальные выводы нужны на всякое - на концевики, питание шпинделя, его обороты (если бы они были цифровыми).
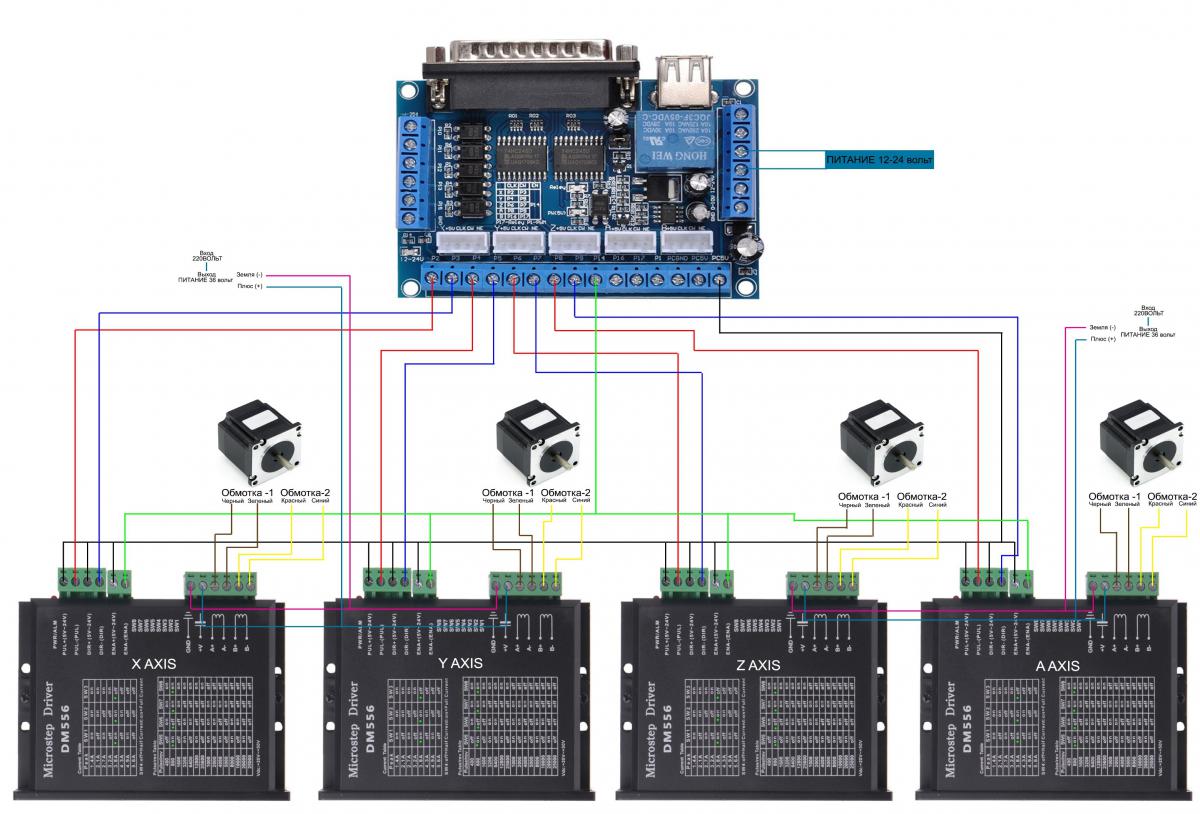
Прямо из ввода 220В в системный блок я сделал питание монитора и пылесоса, чтоб не плодить 10 выключателей (клемы Wago слева внизу).
По факту, для раскроя материала станок пригоден более чем - да, где-то на рейке может вылезти небольшой люфт, но когда толщина материала пару мм, и тонкая фреза с такой же в пару мм высотой рабочей кромки, это не играет особой роли. С длинными фрезами для 3D фрезерования есть вопросы (они и существенно дороже раскройных), я подумываю об усилении оси X и переводе всех осей на ШВП, но это дело будущего.
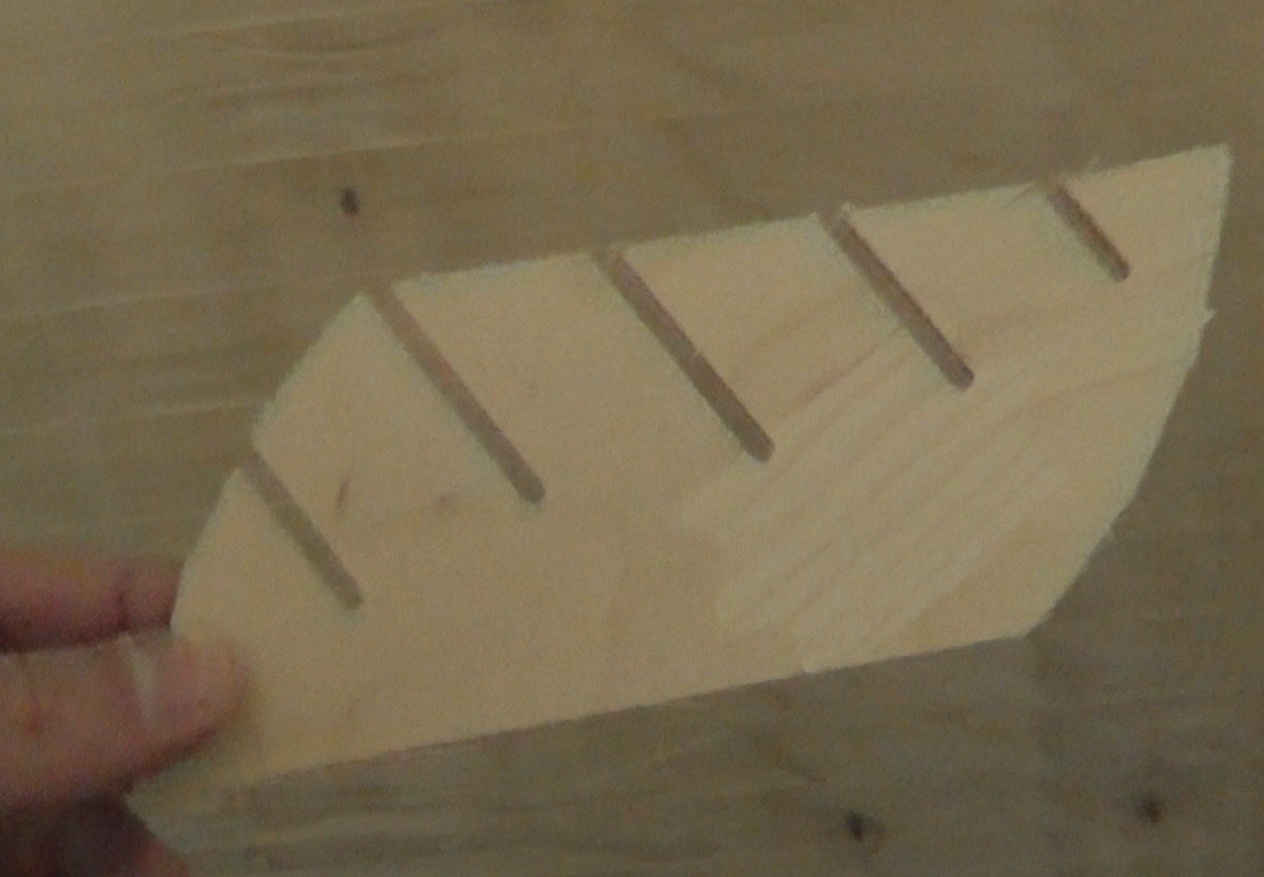
Что хотелось бы сказать в завершение. Если вас что гнетет какая-то идея, а допустим, ваша жена против, следуйте велению своего сердца. Если оно говорит, что надо закончить проект, так и поступайте (если оно говорит - беспрекословно слушаться жену, возможно, это тоже разумный путь).
Всем удачи!
P.S. Пишите в ЛС, на youtube и т.д., если вас сильно интересует тот или иной вопрос.
Автор: Nikita001